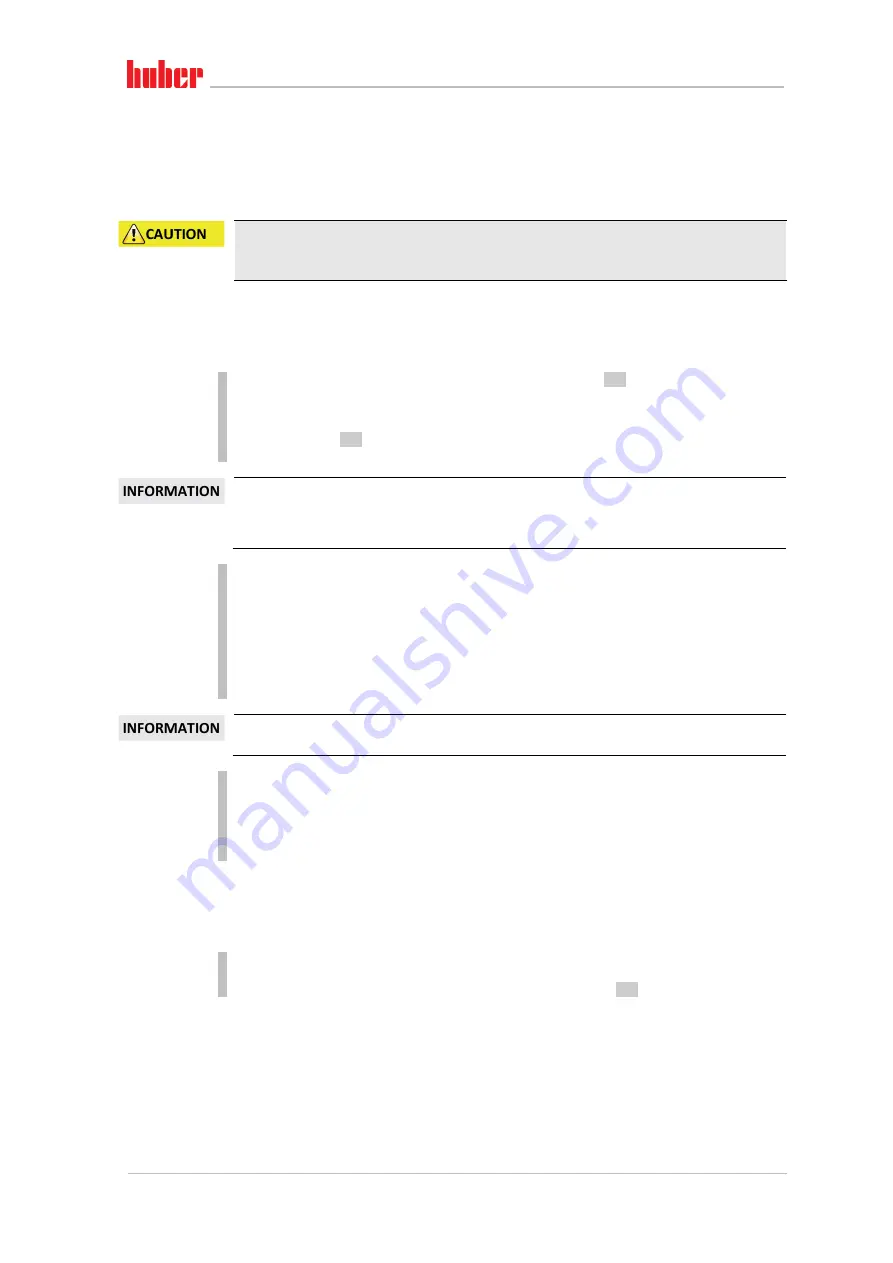
Setup mode
OPERATION MANUAL
Chapter 4
Unichiller® eo Desktop
V2.2.0en/09.08.21//17.12
44
4
Setup mode
4.1
Setup mode
Moving the temperature control unit during operation
SERIOUS BURNS/FREEZING OF THE HOUSING PARTS/ESCAPING THERMAL FLUID
Do not move temperature control units that are in operation.
4.1.1
Turning on the temperature control unit
PROCEDURE
Turn on the temperature control unit using the
>Mains switch<
[37].
First, a system test is conducted to test the full functionality of the temperature control unit. All
sensors, the all-pole disconnecting power disconnect relay for the power supply and the power
electronics of the main heater and the main heater itself are checked. A message appears on the
>Touchscreen<
[88] in case of an error or if a warning is issued. In case of doubt, please contact
Customer Support.
→
The following data entry is required only for:
a.) Initial start-up
b.) resetting the temperature control unit to the factory settings.
→
After switching on the temperature control unit, tap on the required system language.
Touch "OK" to confirm your selection.
Tap on the thermal fluid used.
Touch "OK" to confirm your selection.
Read the message and confirm by tapping on “OK”.
Enter the volume using the number keypad that appears.
Touch "OK" to confirm your entry.
Set the setpoint limits to the thermal fluid used.
→
→
»Setting the setpoint thresholds«
If your temperature control unit is not integrated into a network, confirm the preset IP address
(0.0.0.0) by tapping on “OK”. This skips the network settings.
Enter the required IP address using the number keypad that appears.
Confirm your entry by tapping on “OK”.
Enter the required Subnet Mask using the number keypad that appears.
Confirm your entry by tapping on “OK”.
Tap on the required remote control mode.
Confirm your choice by tapping on “OK”.
4.1.2
Turning off the temperature control unit
PROCEDURE
Warm the thermofluid to room temperature.
Stop the thermoregulation.
Switch off the temperature control unit using the
>Mains switch<
[37].