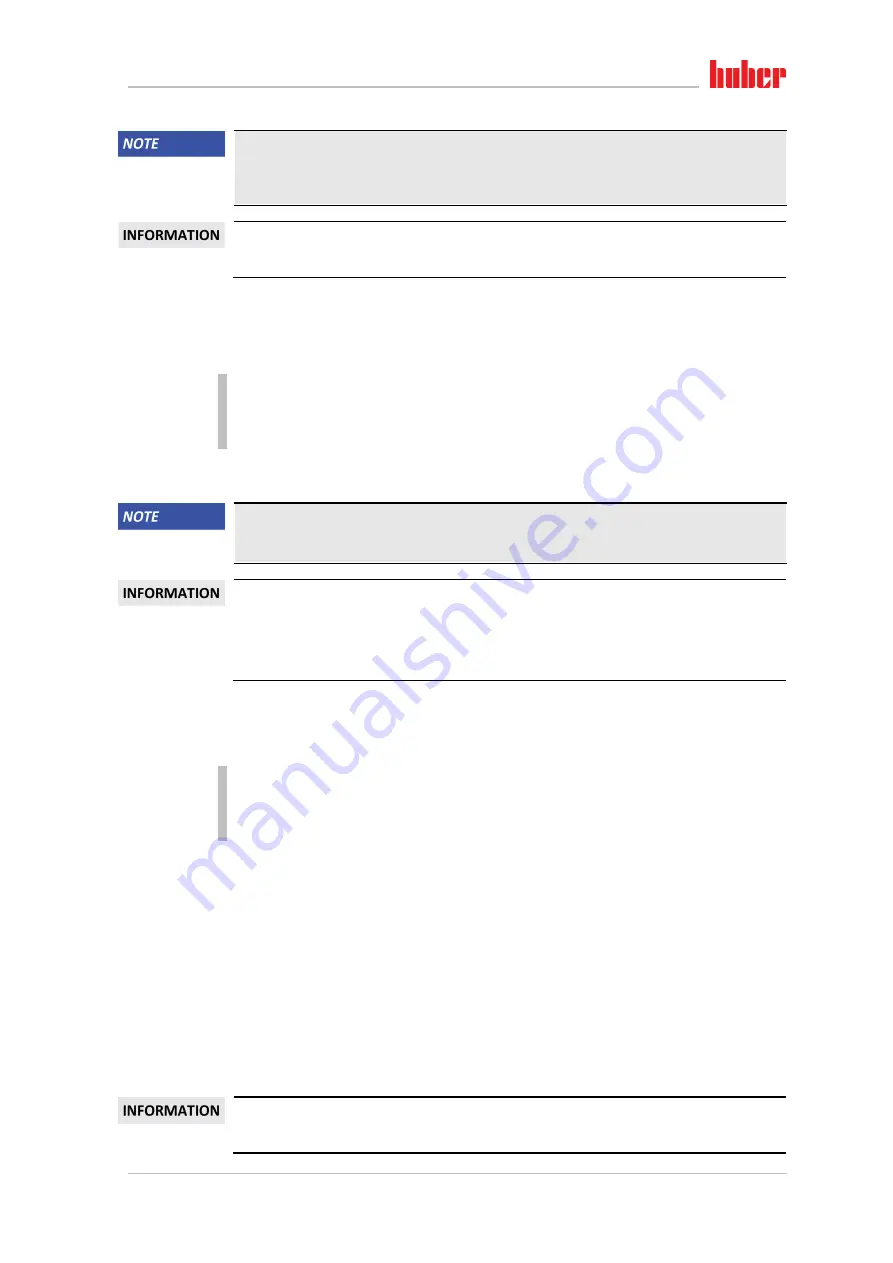
Setup mode
Chapter 4
OPERATION MANUAL
V2.2.0en/09.08.21//17.12
Unichiller® eo Desktop
47
The steps below are carried out without permanent monitoring of the temperature control unit
DAMAGE TO AND IN THE VICINITY OF THE TEMPERATURE CONTROL UNIT
The following actions may only be carried out while constantly monitoring the temperature
control unit and the application!
Run the test only if the temperature of the thermal fluid used is about 20 °C. You must
NOT leave
the temperature control unit unattended
during the entire test of the overtemperature protec-
tion.
The Pilot ONE controller contains a description for carrying out the overtemperature protection test.
PROCEDURE
Go to the “Categories Menu”.
Tap on the category “Safety”.
Tap on the category “OT Test”.
The description for carrying out the overtemperature protection test is displayed.
Tap on the “OK” touch button after you have read the information.
4.1.5
Adjusting the Delta T limiter
The Delta T limiter has not been adjusted to the used glass apparatus
DAMAGE CAUSED BY GLASS APPARATUS BURSTING
Adjust the Delta T value to your application.
The temperature dynamics inside the reactor/process temperature are dictated by the flow tem-
perature. A differential temperature (Delta T) occurs between the flow temperature and the tem-
perature inside the reactor. The greater the permitted Delta T, the better the energy transmission
and hence the faster the speed reaches the setpoint. However, damage could result if the temper-
ature difference limits are exceeded (bursting of the application e.g. glass apparatus). This differ-
ence in temperature may have to be restricted depending on the application (glass apparatus).
4.1.5.1
Changing the Delta T limiter
PROCEDURE
Go to the “Categories Menu”.
Tap on the category “Protection Options”.
Tap on the sub-category “Delta T limiter”.
Set the value of Delta T in line with the glass apparatus.
Confirm your entry by tapping on the “OK” touchbutton.
4.2
The temperature control circuit
Every temperature control unit with a Pilot ONE control panel has its own PID controller for internal
and process temperature control. For many temperature control tasks it is sufficient to use the
factory-set control parameter. Our years of experience and current developments in control tech-
nology are used in these control parameters.
If a process control system is used, ideally send the specification of the temperature setpoint digital-
ly to the temperature control unit. For this purpose, an Ethernet and USB port is available at the
Pilot ONE and a RS232 interface at the temperature control unit. With the optional Com.G@te, an
additional RS485 interface is added to your temperature control unit. Optionally you can integrate
the temperature control unit in a Profibus environment.
→
From page 65, section
The capacity adjustment of the temperature control unit is optimized so that the specified pro-
cesses are run through in the fastest possible time. This increases the productivity of the system as
a whole and thus saves energy in the long term.