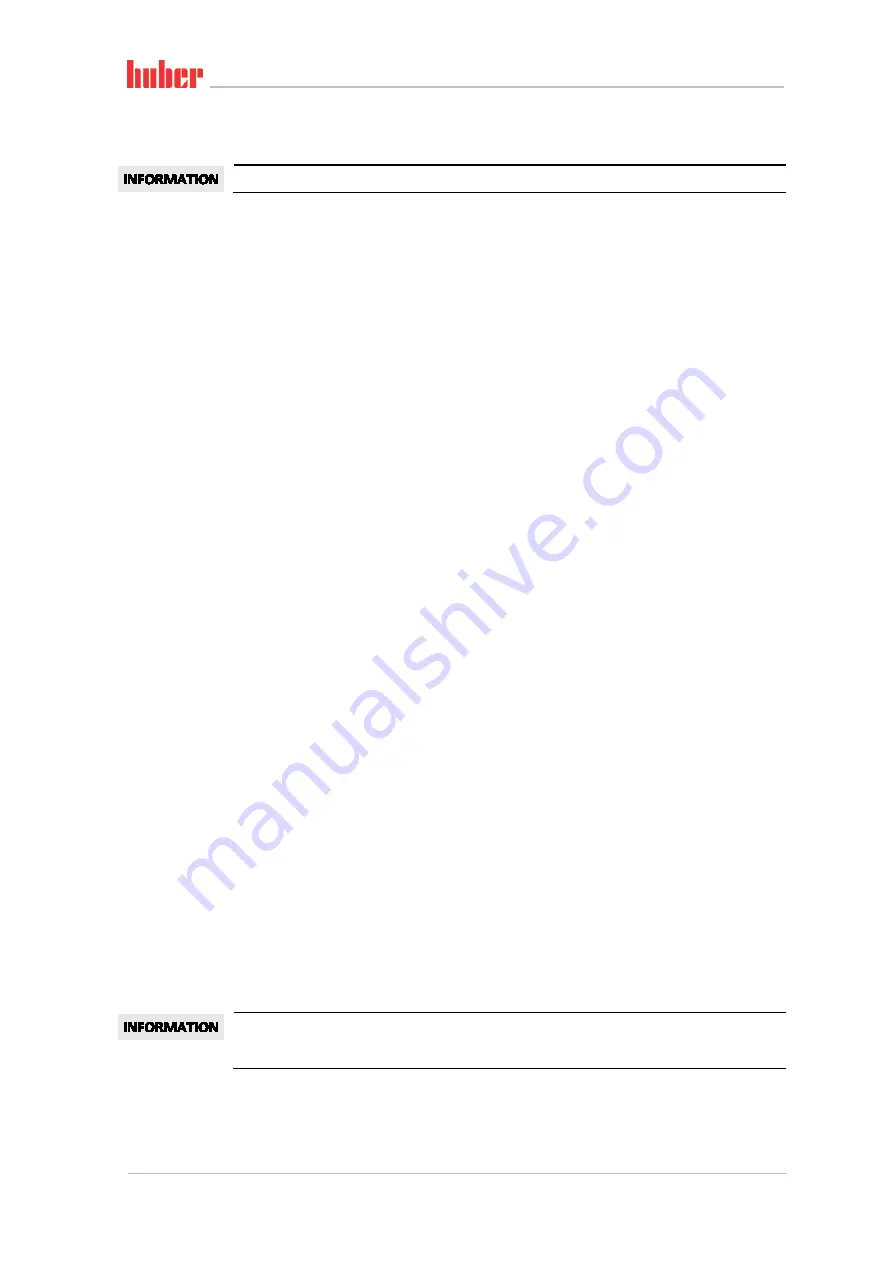
Function description
OPERATION MANUAL
Chapter 3
Unichiller®
V2.3.0en/07.06.19//17.12
36
3.3
To be noted when planning the test
Also observe page 13 in section
.
The focus is on your application. Bear in mind that system performance is influenced by heat trans-
fer, temperature, thermal fluid viscosity, volume flow, and flow speed.
▪
Make sure that the electrical connection is adequately dimensioned.
▪
The installation location of the temperature control unit should be selected so as to ensure ade-
quate fresh air, even with water-cooled chillers.
▪
The maximum forward flow pressure of a temperature control unit must be taken into account in
case of pressure-sensitive applications, such as glass reactors.
▪
Cross-section reduction or shut-off in the thermal fluid circuit must be avoided. Take correspond-
ing measures to limit the pressure in the system; see data sheet from page 85 in the section
and the data sheet for your glass apparatus.
▪
Check whether it is necessary to use an external bypass for temperature control units without
pressure limitation.
▪
In order to prevent the risk of overpressure in the system, the thermal fluid must always be ad-
justed to room temperature before switching off. This will prevent damage to the temperature
control unit or the application. Any isolating valves must remain open (pressure equalization).
▪
The temperature and the dynamics of the process are determined by the flow temperature. A
differential temperature (Delta T) forms between flow temperature and process temperature.
This temperature difference may have to be limited, because Delta T might exceed limits of the
application (glass apparatus) and cause bursting. Adjust the Delta T value to your application.
▪
Select the thermofluid to be used in such a way that it not only permits the minimum and maxi-
mum working temperature but is also suitable with regard to combustion point, boiling point, and
viscosity. In addition, the thermofluid must be compatible with all the materials in your system.
▪
Avoid bending the temperature control and cooling water hoses (if required). Use suitable angle
pieces and lay the hose connections with a large radius. Take the minimum bending radius from
the data sheet of the temperature control hoses used.
▪
The selected hose connections must be able to withstand the thermal fluid, the working tempera-
tures and the admissible maximum pressure.
▪
Check the hoses at regular intervals for any material fatigue (e.g. cracks, leaks).
▪
Keep the temperature control hoses as short as possible
-
The inside diameters of the temperature control hoses must correspond at least to the
pump connections. Select bigger inside diameters for longer line lengths to compensate
for pressure loss in the piping.
-
The viscosity of the thermal fluid determines the pressure drop and influences the tem-
perature control result, especially at low working temperatures.
-
Too small connectors and couplers and valves can generate significant flow resistance.
Your application will therefore be slower to reach its design temperature.
▪
Basically, you should only use the thermofluid recommended by the manufacturer and only with-
in the usable temperature and pressure range.
▪
The application should be roughly at the same height of or below the temperature control unit if
the thermoregulation is close to the boiling temperature of the thermofluid.
▪
Fill the temperature control unit slowly, carefully and evenly. Wear the necessary personal pro-
tective equipment, such as goggles, heat-proof and chemical-resistant gloves, etc.
▪
The temperature control circuit must be vented after filling and setting all required parameters.
This is required to ensure trouble-free operation of the temperature control unit and hence your
application.
For water-cooled temperature control units, please take the cooling water temperature necessary
for perfect operation and the required differential pressure from the data sheet from page 85
onward in the Section
.