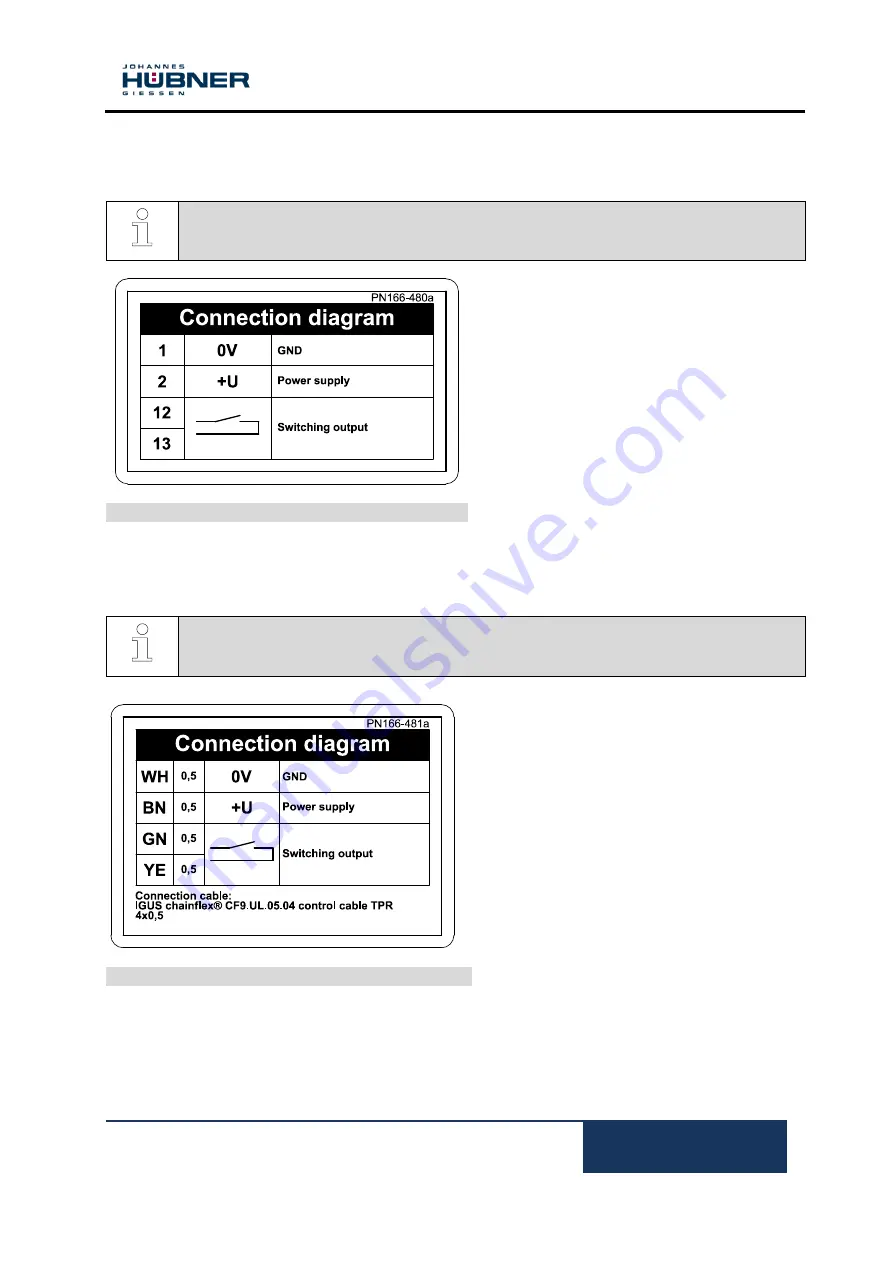
Electronic overspeed switch EGS 2
EGS2_MANUAL-en_R3(2018-11-14)ID74563.docx
23
14
Connection diagrams
14.1
Terminal box
NOTES!
The connection diagrams are displayed in each terminal box cover!
Connection diagram PN166-480a
14.2
Connection cable
NOTES!
The connection diagrams are attached to each cable!
Connection diagram PN166-481a