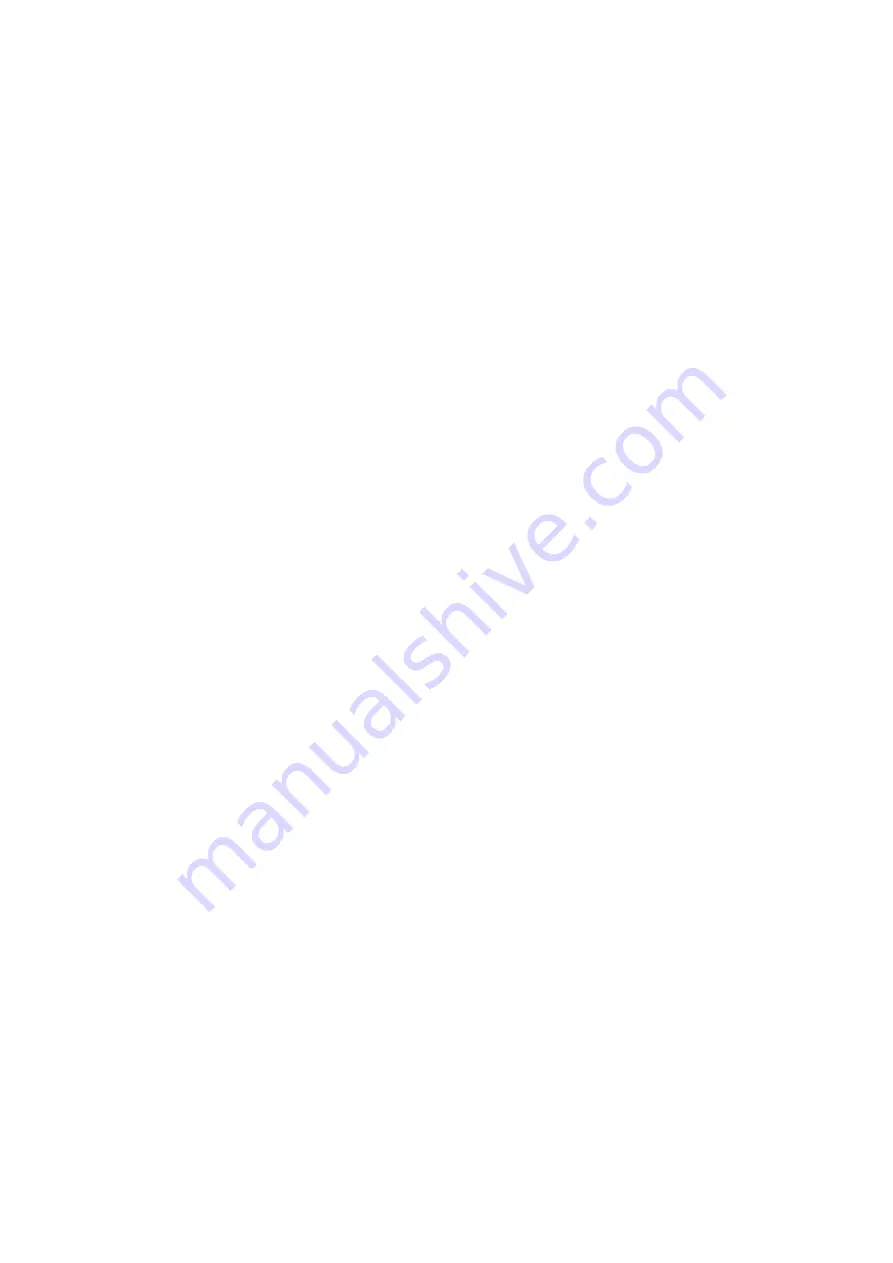
15
5.4 Arc ending
Set arc ending mode switch to “ON”.
The operator shall adjust and set welding current, arc ending current, welding voltage, and arc ending
voltage. (Usually the arc ending current is less then welding current, the valve shall be set according to
the crater.). The procedure is: press torch trigger under high OCV condition for inching feeding, striking
arc, release the trigger and the wire will keep burning (the values on the current meter and voltage meter
is welding current and welding voltage), press the trigger again after welding, then the machine is under
arc ending condition (the values on the current meter and voltage meter is arc ending current and arc
ending voltage), release the trigger after the crater is filled up, then arc stop.
Set arc ending mode switch to “OFF”.
The operator shall adjust and set welding current and welding voltage. The procedure is: press torch
trigger under high OCV condition for inching feeding, striking arc, wire will keep burning (the values on
the current meter and voltage meter is welding current and welding voltage), release the trigger after
welding, then arc stop.
5.5 Waveform control
After setting welding current and welding voltage, please adjust electronic reactance adjustment knob
adjusting knob to reduce the spatter, if the spatter is too big.
ATTENTION:
The outer circle of indicating value of welding voltage and arc ending voltage are not value of voltage. It
is adjusting direction.
The “ON’ and ‘OFF” of arc ending can be used under integrative adjustment and independent
adjustment.
The adjusting indication of waveform is not quantitative value, it is adjusting direction.
5.6 Maintenance and service
* As a Hi-Tech machine, the INVERMIG
III
series welding machine employs many advanced electronic
parts. Proper operation & maintenance conducted by qualified personnel can assure it of good
performance and prolong its operating life. Only the qualified personnel are allowed to be in charge of
repairing. It is strongly recommended customers contact with our company or agent for technical,
repairing, accessories supply and service back-up when they feel unable to work out the technical hitch
or problems.
* Maintenance job should be conducted by the trained personnel. It is never allowable to have hot line
job.
* The newly installed welder or it not in use for some time needs to be surveyed the insulation
resistances between each winding and every winding to case with multimeter, which can not be less
than 2.5MΩ.
* Keep from rain, snow and long term exposing to sunlight when welder is used outdoor.
* If the welder is not in use either for a long time or temporarily, it should be kept dry and have good
ventilation to free it from moisture, eroded or toxic gas. The tolerable temperature ranges from
﹣
25
~
﹢
55
℃
, and the relative humidity can not be more than 90%.
* Dust removal
The professional maintenance personnel should use dry compressed air (use air compressor or bellows)
to remove the dust inside the machine. The part adhering to grease must be cleaned with cloth while
make sure there are no loosing parts existed in the tightened places and connected cable. Usually the
machine should be cleaned once a year if the dust accumulation problem is not very serious, while it