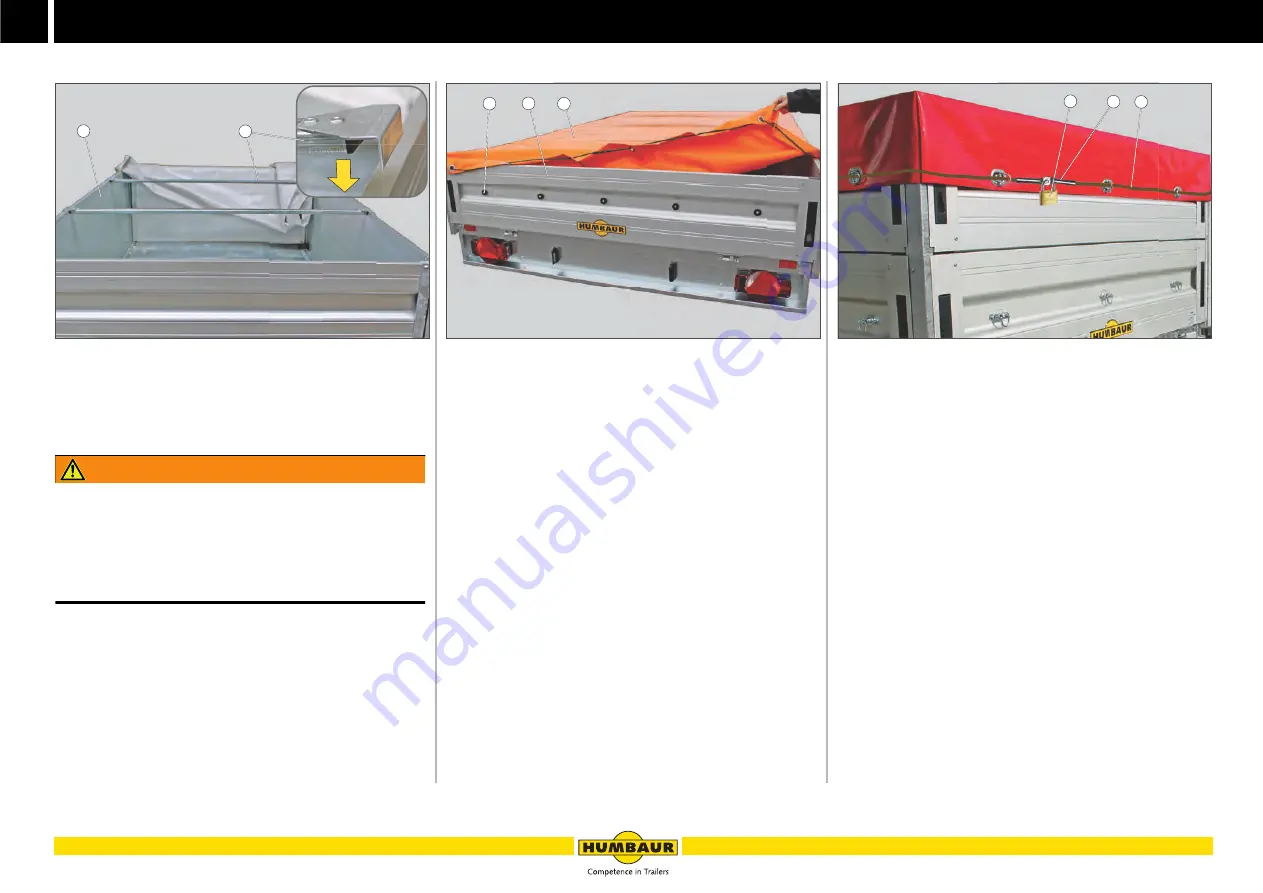
Flat cover
5
118
Body
Positioning lateral bracing
Fig. 58
Lateral bracing positioned
1
Side drop side
2
Lateral bracing
WARNING
Driving with the lateral bracing inserted - without a flat
cover!
The lateral bracing could be thrown off while driving and hit
people – risk of accident!
Remove the lateral bracing before driving without a flat
cover.
Slot the lateral bracing (Fig. 58 /2) onto the side drop
sides (Fig. 58 /1).
Position the lateral bracing at equal distances at a 90°
angle to the side drop sides.
Handling the flat cover
Fig. 59
Pulling on flat cover
1
Securing element
2
Drop side
3
Flat cover
Attachment
Please make sure that the flat cover is not excessively
stressed by the load.
Secure the flat cover with securing elements (Fig. 59 /1).
Removal
Unlock the securing elements (Fig. 59 /1) on the flat
cover.
Pull the flat cover from the rear to the front.
Stow the flat cover without creasing it as far as possible
when not using it.
The flat cover must be clean and dry.
Fastening / duty rope (optional)
Fig. 60
Fastening / duty rope lock as anti-theft device
1
Shackle lock
2
Rope end fastener
3
Fastening rope
Feed the fastening rope (Fig. 60 /3) through all closed
staples.
Connect the rope end fasteners (Fig. 60 /2) to each other
- e.g. with a carabiner.
Use a secure lock such as a shackle lock (Fig. 60 /1).
A - 033
1
2
A - 037
1
2
3
A - 029
1
2
3
Summary of Contents for 1000 Series
Page 1: ...GENERAL CAR Program PART 1 OPERATING MANUAL humbaur com 1000 8400 SERIES EN ...
Page 9: ...1 7 Safety ...
Page 21: ...2 19 General information ...
Page 31: ...3 29 Operation ...
Page 67: ...3 65 Operation Trailer safety ...
Page 75: ...4 73 Chassis ...
Page 103: ...5 101 Body ...
Page 134: ...Cover net 5 132 Body ...
Page 135: ...6 133 Electrical system ...
Page 145: ...7 143 Testing care and maintenance ...
Page 185: ...8 183 Troubleshooting guide ...
Page 194: ...Hydraulics 8 192 Troubleshooting guide ...
Page 195: ...9 193 Proof of inspection ...