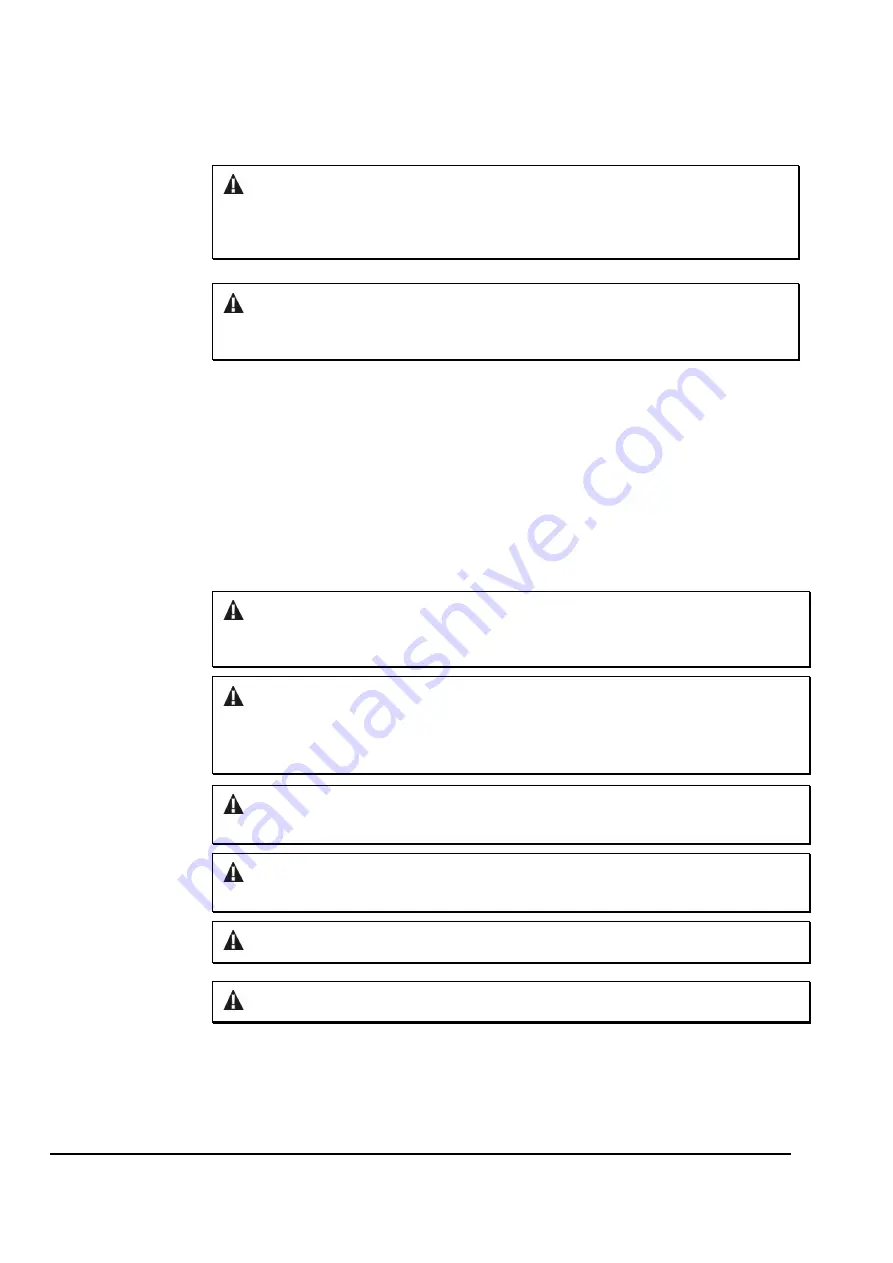
2
••••
Getting Started
TC39 Series Changer Operation Instructions
IMPORTANT SAFETY INSTRUCTIONS
WARNING: This machine stores and uses significant volumes of compressed air.
Disconnect compressed air at the source and drain all compressed air
before servicing. Severe injury or death can occur if service is
attempted on a compressed air chamber while it is charged.
WARNING: This machine uses high voltage electrical power. Shut down and
unplug the machine at the source before servicing. Severe injury or
death can occur if service is attempted on a live electrical circuit.
Read and follow all caution and warning labels affixed to equipment and tools.
Read and understand all instructions before operating this machine.
Misuse of this equipment can cause personal injury and shorten the life of the TC.
To prevent accidents or damage to the TC, use only Hunter recommended procedures and
accessories.
Wear OSHA approved eye protection while operating the TC.
Wear non-slip safety footwear when operating the TC.
Do not wear jewelry or loose clothing when operating the TC.
Wear proper back support when lifting or removing wheel from the TC.
Never stand on the TC.
WARNING:
Keep hands and clothing clear of moving parts. Keep hands clear
of upper roller when bead loosening or rotating clamped wheel.
Do not lean or reach over tire when inflating.
WARNING:
Do not exceed these pressure limitations:
SUPPLY LINE PRESSURE (from compressor) 175 PSI.
OPERATING PRESSURE (gauge on regulator) 145 PSI.
BEAD SEATING PRESSURE (gauge on hose) 40 PSI.
WARNING:
Never mount a tire to a rim that is not the same diameter (e.g., 16
1/2 inch tire mounting on a 16 inch rim).
WARNING:
After loss of air line pressure ALWAYS raise the wheel lift pedal
to prevent the wheel lift from rising quickly during first operation.
DANGER:
Activate blast inflation nozzle only when seating bead.
CAUTION:
Do not hose down or power wash electric tire changers.
Bleed air pressure from system before disconnecting supply line or other pneumatic
components. Air is stored in a reservoir for operation of the blast inflation nozzle. Air
pressure can be bled from the system by pulling up on the knob located on top of the
regulator, and then turning it counterclockwise.
Do not activate the blast inflation nozzle if the tire is not properly clamped.