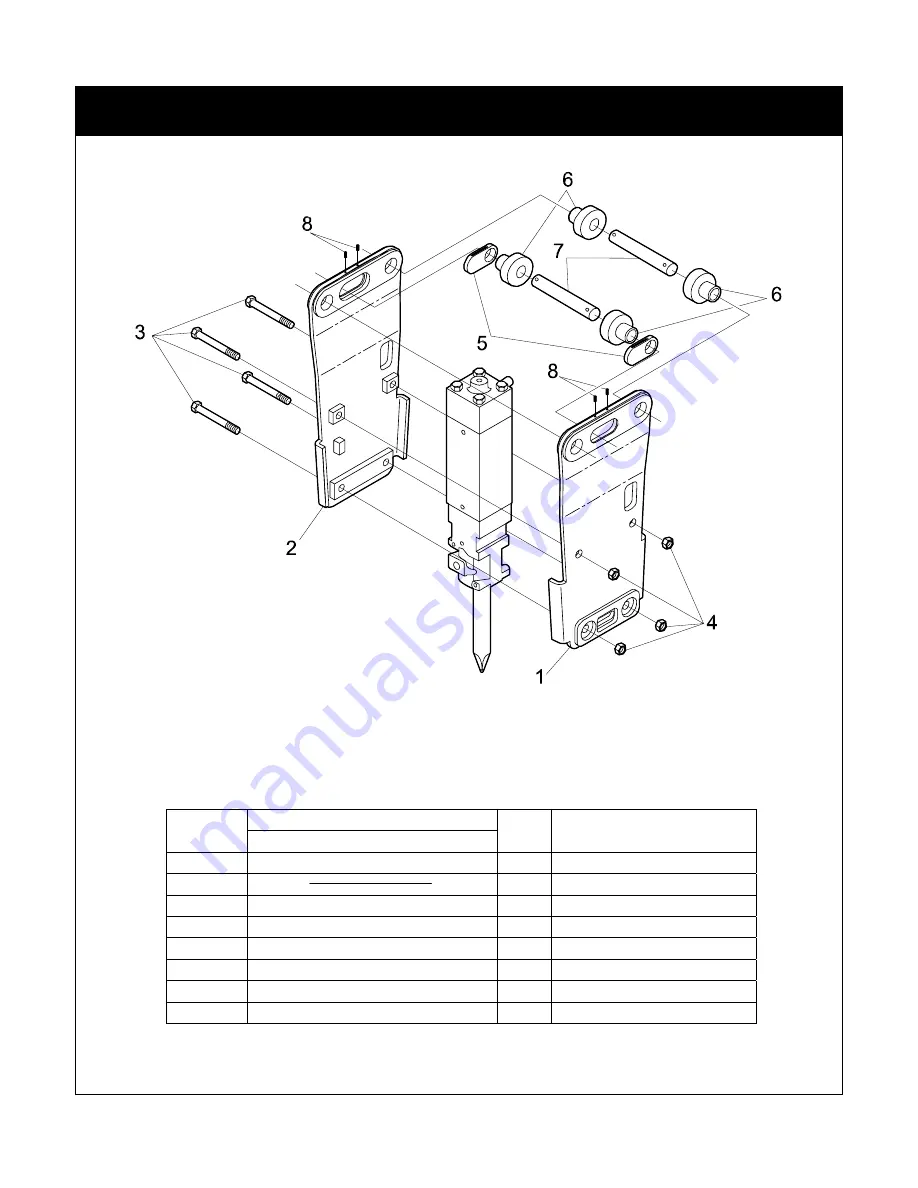
45
BRACKET ASSEMBLY PARTS LIST
PART NO.
ITEM
MODEL HH300-2
QTY
DESCRIPTION
1.
3D02-312021MFV
1
Hammer Bracket (R)*
2.
1
Hammer Bracket (L)*
3.
3D01-312051MF
4
Bracket Bolt w/ nut
4.
Assembly of Item 3
4
Nut
5.
By Carrier Model
2
Variable Plate
6.
By Carrier Model
4
Bushing
7.
By Carrier Model
2
Pin
8. 3Z01-5161834
4
Set
Screw
*Sold as matched set w/ hardware Effective 07/09
HH300-2 MULTI-FIT VARIABLE
Summary of Contents for HH100
Page 1: ...HUSKIE HYDRAULIC HAMMERS SERVICE MANUAL HH100 HH150 2 HH300 2 HH500 2 HH750 2 HH1000 2 ...
Page 2: ...2 ...
Page 33: ...33 9 PARTS LIST AND ILLUSTRATIONS HH100 HH150 2 HH300 2 HH500 2 HH750 2 HH1000 2 ...
Page 35: ...35 HH100 HAMMER Effective 07 09 ...
Page 37: ...37 ...
Page 39: ...39 HH150 2 HAMMER S N 001 099 2B2 1000 UP Effective 07 09 ...
Page 41: ...41 ...
Page 43: ...43 HH300 2 HAMMER S N 001 099 2E2 1000 UP Effective 07 09 ...
Page 47: ......
Page 49: ...49 HH500 2 HAMMER S N 001 099 2R2 1000 UP Effective 07 09 ...
Page 55: ...55 HH750 2 HAMMER S N 001 099 2F2 1000 UP Effective 07 09 ...
Page 59: ...59 ...
Page 61: ...61 Effective 07 09 HH1000 2 HAMMER S N 001 099 2H2 1000 UP ...