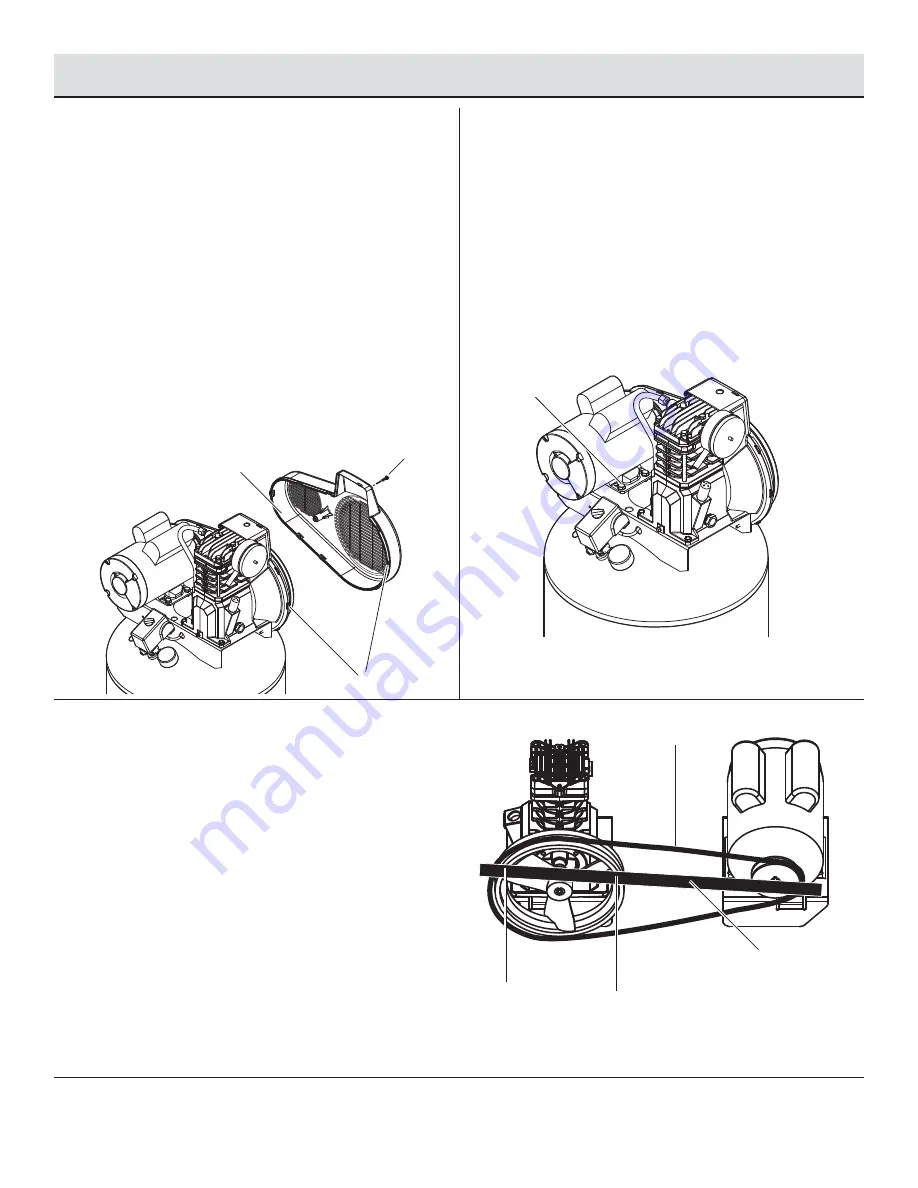
20
Maintenance (continued)
4
Checking the belt
□
Remove the beltguard screw (1).
□
Remove the front beltguard (2). The beltguards are held
together by pressure snap-latches (3). Wedge a fl athead
screwdriver between the beltguards at the snap-latches.
□
Wedge a screwdriver at the other snap-latch junctions.
Twist and separate the snap-latches until the front
beltguard comes completely off.
□
If the belt appears to be in working order and has no
signs of damage, return the front beltguard to the original
position and snap it back in place. Tighten the beltguard
screw.
□
If the belt needs to be replaced, move on to the next step.
□
If the belt does not need to be replaced, move to step 6.
5
Removing the belt
□
Loosen (but do not remove) the four bolts (1) holding the
motor in place.
□
Shift the motor towards the pump. The belt should be slack
and easily removed.
□
Replace the belt.
□
Move the motor back to the original position to create belt
tension.
□
Tighten the motor bolts.
6
Aligning / tensioning the belt
□
Lay a straightedge (1) against the face of the fl ywheel
touching the rim at two places (2,3).
□
Adjust the flywheel or motor pulley so that the belt (4) runs
parallel to the straightedge. Use a gear puller to move the
pulley on the motor shaft. Tighten the setscrew after the
pulley is positioned.
□
Adjust the motor’s distance from the pump if needed.
□
Belt tension is determined by how much the belt moves
when weight is applied. The belt should move no more
than 3/8 to 1/2 in. downward if normal thumb pressure is
placed on it.
□
Tighten the motor bolts once the proper belt tension is
achieved.
□
Reattach the belt guard.
1
2
4
3
1
2
3
1