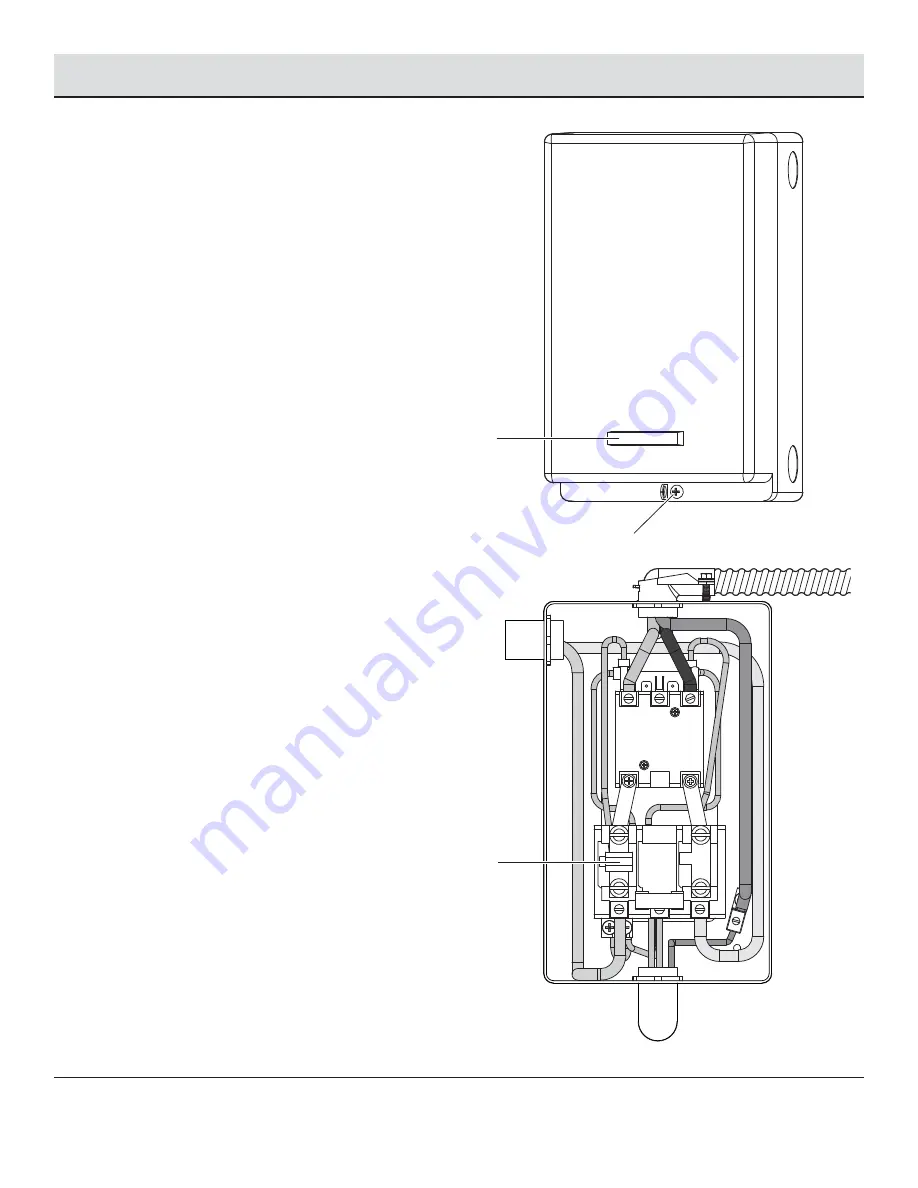
22
Maintenance (continued)
7
Reseting the thermal overload
Allow the air compressor unit (A) to cool down after thermal
overload of the magnetic starter is tripped.
□
Disconnect, tag, and lock out the power source for the air
compressor unit (A).
□
Push the external reset switch (1). The internal overload
switch (2) will be pushed back into place and return
contact for the electrical current.
□
Return power to the air compressor unit (A).
If the air compressor unit (A) does not return to normal operation,
other maintenance may be required.
□
Disconnect, tag, and lock out the power source for the air
compressor unit (A).
□
Remove the magnetic starter cover by loosening the
screw (3), as shown. Use a Phillips screwdriver.
□
Lift the cover upwards from the bottom and off the base.
Set the cover aside.
□
Remove the internal overload switch (2) and replace.
Contact Husky Customer Service at 1-888-43-HUSKY for
assistance.
THERMAL OVERLOAD CAUSES
In normal operation, the starter requires no attention. If an overload
occurs, the compressor motor will not restart, even when the tank
pressure drops. It is important to find the cause of the overload and
correct it. Overloads can be caused by one of the following:
1. Pressure setting too high:
Check to make sure the pressure
switch opens at or before the maximum rated operating
pressure of the air compressor unit. If the pressure switch
fails to operate correctly, contact Husky Customer Service at
1-888-43-HUSKY for assistance.
2. Low voltage condition:
Voltage at the motor terminals must
be within 10% of the rated voltage during start-up and while
the motor is running. Have a qualified electrician check this
and correct it as needed.
3. Loose connections or open fuse:
Loose connections or
blown fuses cause high currents in the remaining wires of
the circuit. Have a qualified electrician check and correct
these conditions.
4. Unloader valve or check valve malfunction:
The motor will
overload if it starts against the air trapped in the discharge
tube. Replace valves that are not working correctly. Contact
Husky Customer Service at 1-888-43-HUSKY for assistance.
3
1
2