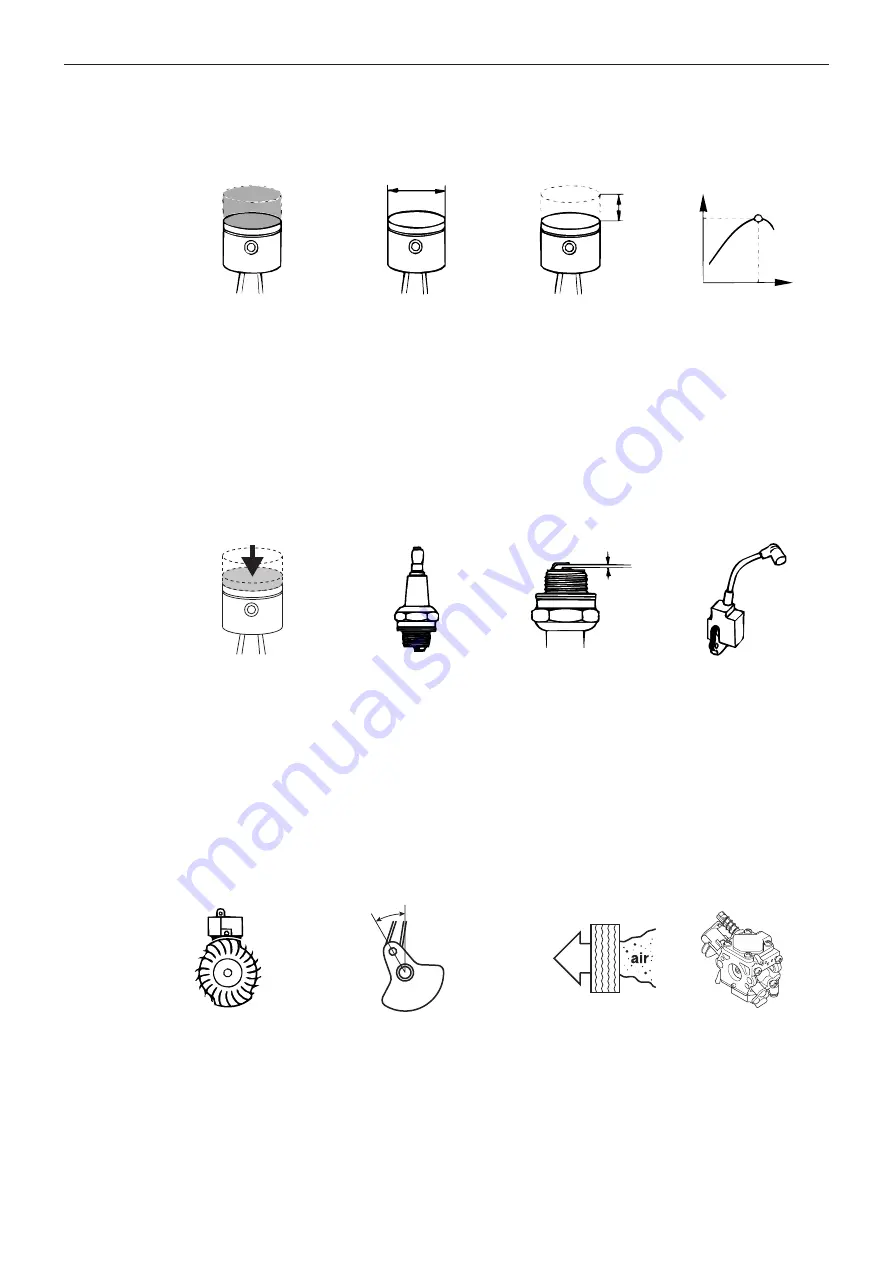
2 Technical data
Displacement
cm3/cubic inch
Cylinder bore
Ø mm/Ø inch
Stroke length
mm/inch
Max. output/speed
kW/hp/rpm
545RXT AT
45.7 / 2.79
42 / 1.65
33.0 / 1.30
2.2 / 2.7 / 9000
545FX AT
45.7 / 2.79
42 / 1.65
33.0 / 1.30
2.2 / 2.7 /9000
545FXT AT
45.7 / 2.79
42 / 1.65
33.0 / 1.30
2.2 / 2.7 9000
Compression ratio
Spark plug
Electrode gap
mm/inch
Ignition system
545RXT AT
9.2
NGK CMR6H
0.5 / 0.02
Walbro
545FX AT
9.2
NGK CMR6H
0.5 / 0.02
Walbro
545FXT AT
9.2
NGK CMR6H
0.5 / 0.02
Walbro
Air gap mm/
inch
Pre-ignition angle
max output
Pre ignition Idle
RPM Range
Air filter type
Carburettor type
545RXT AT
0.3 / 0.012
32°
2° - 27°
Paper
Diaphragm
545FX AT
0.3 / 0.012
32°
2° - 27°
Paper / Nylon
Diaphragm
545FXT AT
0.3 / 0.012
32°
2° - 27°
Paper / Nylon
Diaphragm
Technical data
6 – English
Summary of Contents for 545FX AT
Page 1: ...Workshop manual English 545RXT AT 545FX AT 545FXT AT 545FX 545FXT 545RX 545RXT ...
Page 2: ......
Page 79: ...English 79 ...
Page 80: ...2018 10 04 115 88 11 26 ...