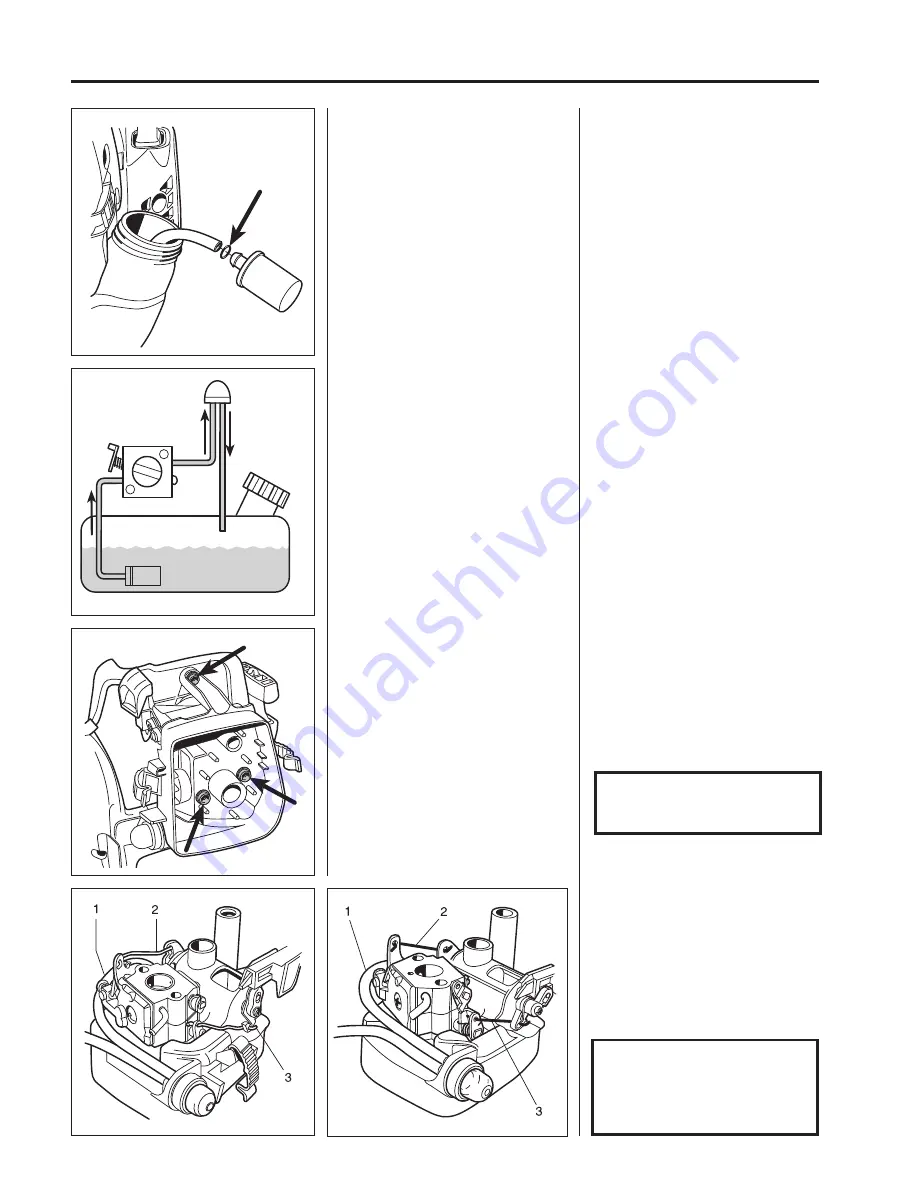
20
3
Fuel system
333/335
336
333/335
Clean the fi lter externally if it is not too
dirty.
Replace the fi lter if required.
If the fi lter is not too dirty, its surface can
be cleaned with a brush.
Otherwise it must be replaced.
Check the fuel hose for cracks and
leaks.
Make sure that the fi lter’s connection
neck is inserted as far as possible into
the fuel hose and that the O-ring (model
333/335) is suffi
ciently tight so that the
fi lter cannot slide off the hose.
NOTE!
Note how the pressure rods (2) and
(3) are fi tted to make it easier when
assembling after a service.
Carburettor
Dismantling
Blow clean the carburettor compartment
and remove the screws holding the car-
burettor and the air fi lter housing.
Carburettor
Dismantling
1. Remove the air fi lter cover and cylin-
der cover and blow clean the carbu-
rettor compartment using compressed
air.
2. Remove the three screws holding the
carburettor and the air fi lter housing.
NOTE!
Do not lose the washer under the
head of the upper screw.
3. Lift off the carburettor and the air fi lter
housing from the cylinder and discon-
nect the throttle cable, the fuel hose
from the carburettor and pull up the
fuel hose, which joins the tank and the
fuel pump, from the tank.
Remove the remaining fuel hose (1) and
both pressure rods (2) and (3).
Fuel pump
The fuel pump facilitates cold starts.
The pump cannot be repaired and must
be replaced if it stops working.
Note how the fuel hoses are connected
to simplify assembly.
Fuel pump
The fuel pump has the task of facilitating
the start of the engine when cold. The
pump fi lls the carburettor with fuel
before attempting to start the engine.
This also prevents vapour bubbles from
blocking the narrow fuel channels.
If the pump does not work it must be
replaced.
Note how the fuel hoses are connected
to simplify assembly.
Summary of Contents for FR335
Page 9: ...8 1 Starter ...
Page 17: ...16 2 Electrical system ...
Page 35: ...34 3 Fuel system ...
Page 41: ...40 4 Centrifugal clutch ...
Page 65: ...64 8 List of tools ...
Page 68: ...504 54 34 26 2018W35 ...