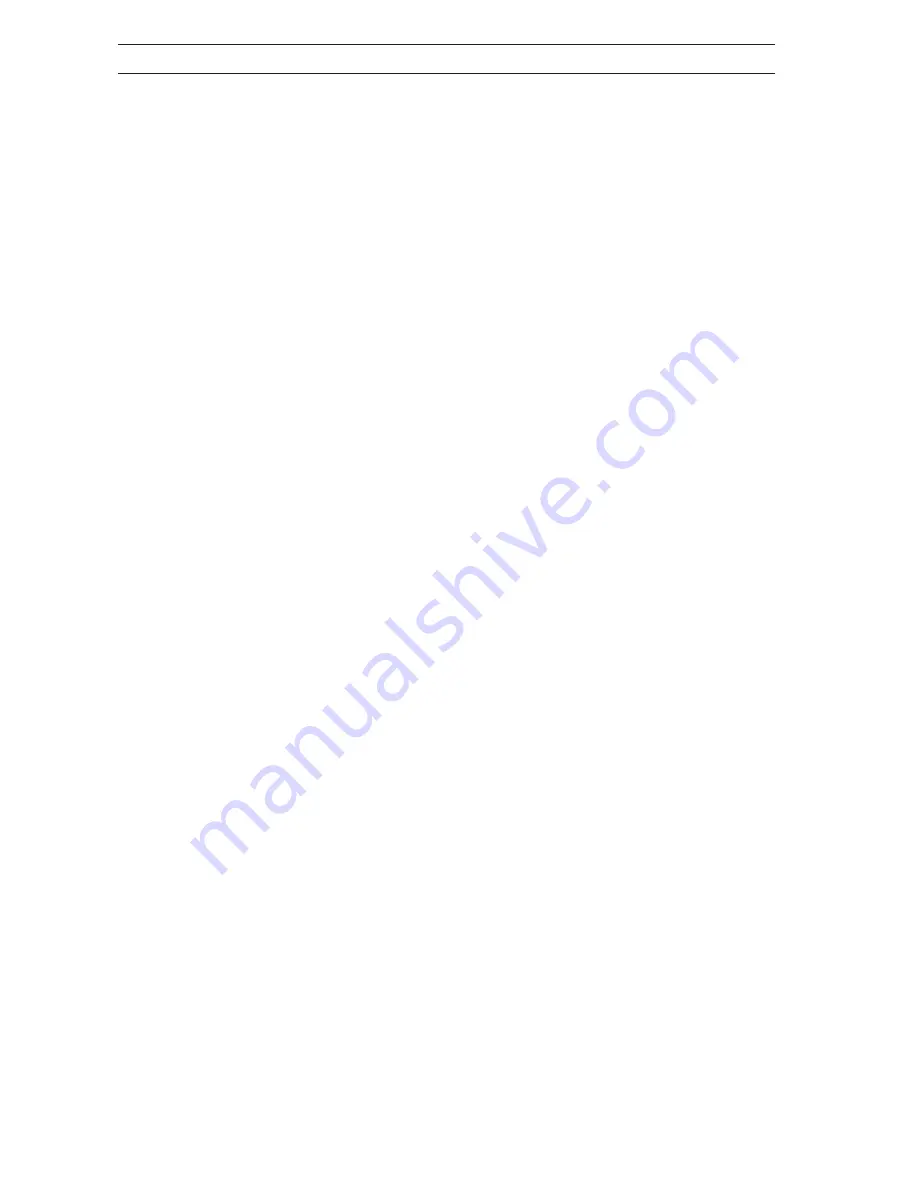
2
– English
TABLE OF CONTENTS
Introduction ....................................... 3
Symbols ............................................. 4
Warning Signs ................................... 4
Safety Regulations ............................ 5
Description ........................................ 7
Installation ....................................... 16
Fuel Handling .................................. 23
Starting and Stopping ..................... 24
Use .................................................... 26
Maintenance .................................... 30
Technical Data ................................. 36