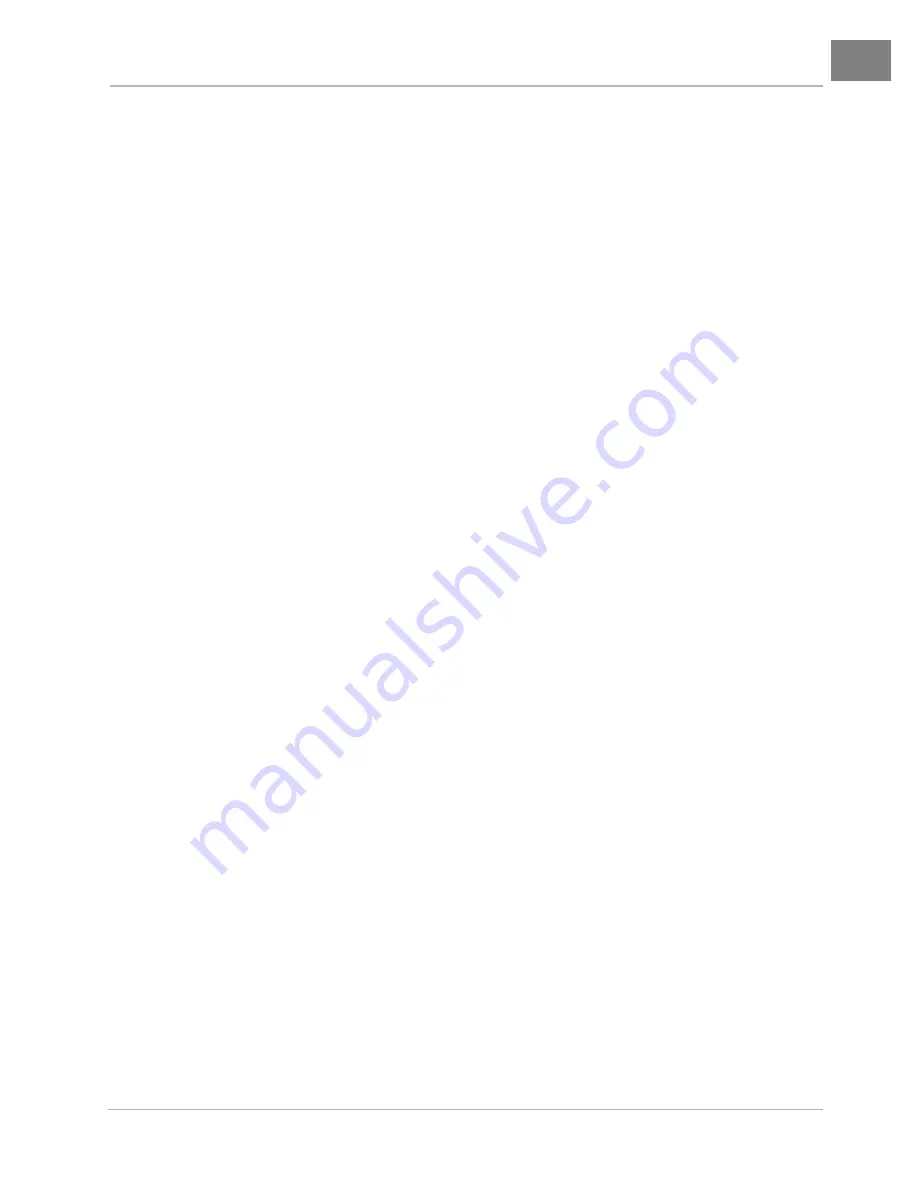
HYDRAULIC AND PARK BRAKE SYSTEMS
Park Brake System
2005 HUV4420 Gasoline and HUV4420-D Diesel Vehicle Maintenance and Service Manual
Page 5-29
5
Lower Frame Pulley Installation
1. Position a new pulley on the lower frame mount, and secure the pulley with four bolts, washers, and lock-
nuts. Tighten the hardware to 4.5 ft-lb (6.0 N·m).
Park Brake Pulleys Installation
1. Position two new pulleys on the pulley mounting plate.
2. Secure each pulley assembly with four bolts, washers, and locknuts. Tighten the hardware to 4.5 ft-lb (6
N·m).
3. Position the pulley mounting plate and the park brake assembly on the front part of the vehicle frame.
4. Secure the pulley mounting plate and park brake assembly with three bolts and locknuts. Tighten the
hardware to 15 ft-lb (20 N·m).
5. Install the front park brake cable.
See Front Park Brake Cable Installation on page 5-27.
6. Install the dashboard.
See Dashboard Installation, Section 4, Page 4-4.
7. Install the front body.
See Front Body Installation, Section 4, Page 4-5.
Summary of Contents for HUV4420
Page 1: ... 5 5 2 4 56 56 3 3 6 3 4 3 26 5 ...
Page 2: ......
Page 16: ...Page xiv 2005 HUV4420 Gasoline and HUV4420 D Diesel Vehicle Maintenance and Service Manual ...
Page 20: ...1 ...
Page 38: ...4 ...
Page 68: ...5 ...
Page 74: ...6 ...