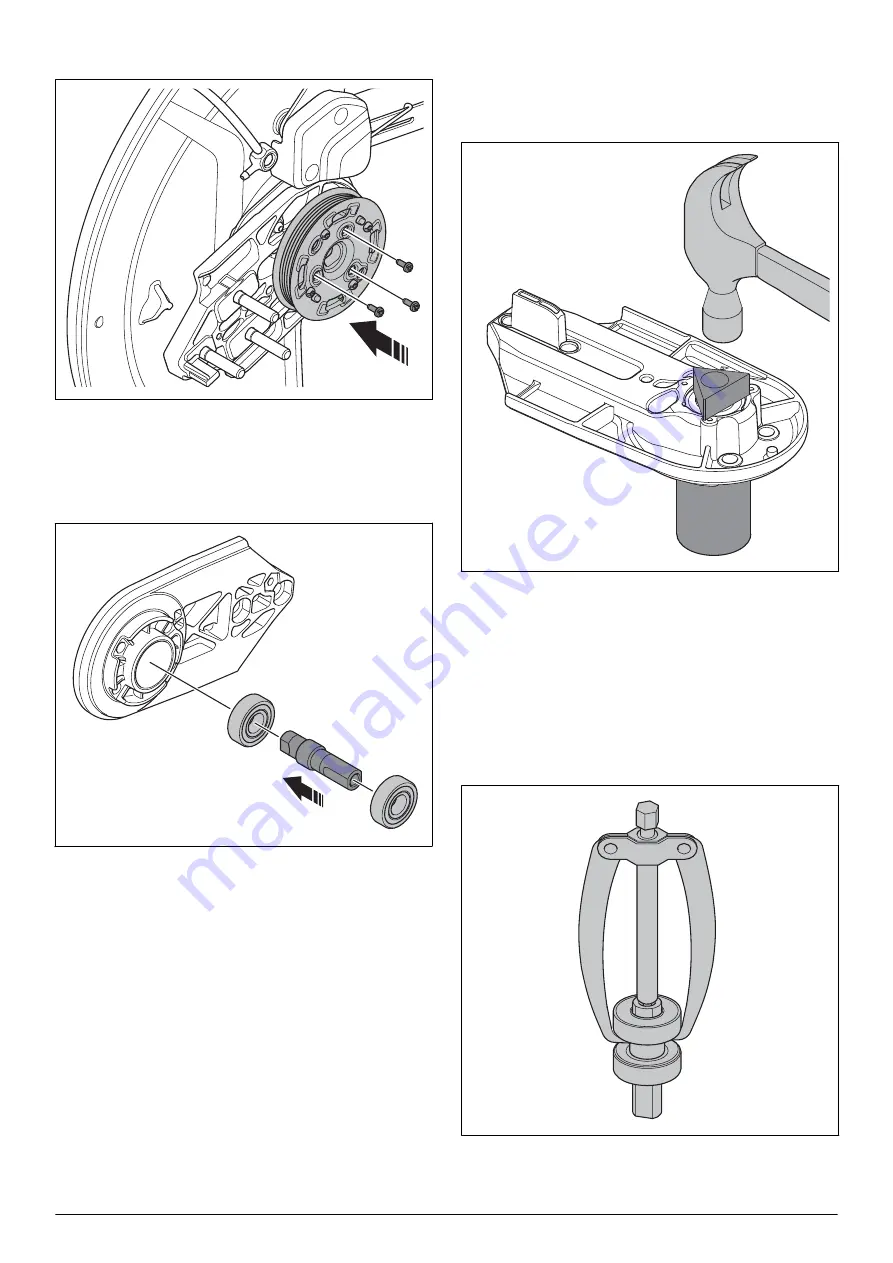
3. Assemble the the brake drum and the bearing
housing.
6.14.8 To remove the blade shaft bearings
The blade shaft bearings are pushed against a spacer
on the blade shaft. The inner rings of the bearing are
installed against the shaft. The outer rings of the
bearings are installed against the bearing housing.
Use a hydraulic press or a bearing press kit to remove
the blade shaft bearings.
•
If you replace the blade shaft bearings with a
hydraulic press, use the Husqvarna press tool. Refer
Servicing tools overview on page 10.
•
If you replace the bearings with a bearing press kit,
use the Husqvarna bearing press kit. Refer to
Servicing tools overview on page 10.
1. Turn the support for assemble with its shoulder up
and put the bearing housing on top of it.
2. Put the triangle from the bearing press kit, or
assembly support from the hydraulic press, on top of
the bearing. Refer to
page 10.
3. Push out the bearing until the triangle is at the edge
of the bearing housing. Then extend with a tool
socket to push out the bearing unit fully from the
bearing housing.
4. Remove the bearings from the blade shaft with a
universal puller.
1451 - 001 - 02.04.2020
Repair and servicing - 63