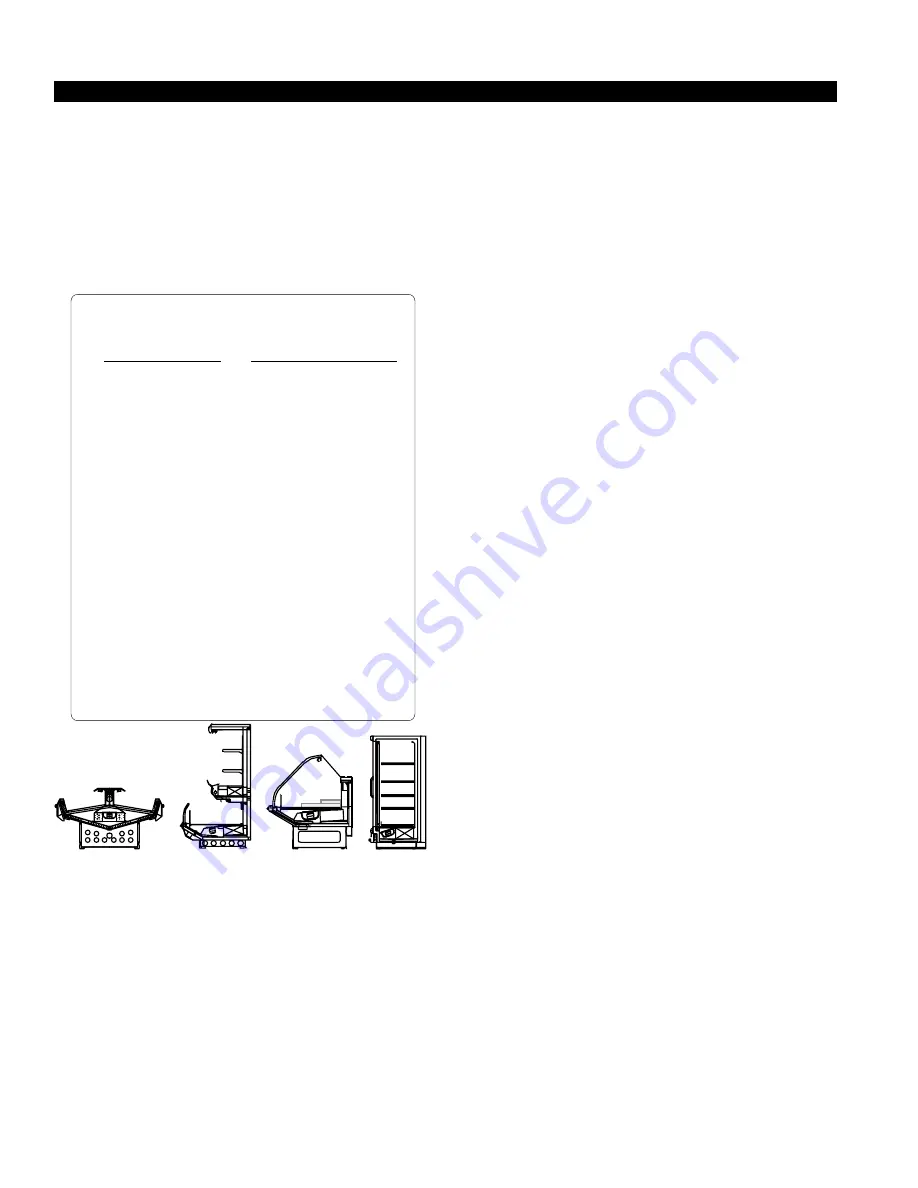
IGSS-RCD-0105
12
APPENDIX A. – Temperature Guidelines
Refrigerated
The refrigerators should be operated according to Hussmann’s
published engineering specifications for entering air temperatures for
specific equipment applications. Table 1 shows the typical temperature
of the air entering the food zone one hour before the start of defrost
and one hour after defrost for various categories of refrigerators.
Refer to Appendix C for Field Evaluation Guidelines.
TABLE 1
TYPE OF
TYPICAL ENTERING
REFRIGERATOR
AIR TEMPERATURE
I. OPEN DISPLAY
A. Non frozen:
1) Meat
28
°
F
2) Dairy/Deli
32
°
F
3) Produce
a. Processed
36
°
F
b. Unprocessed
45
°
F
B. Frozen
0
°
F
C. Ice Cream
-5
°
F
II. CLOSED DISPLAY
A. Non frozen:
1) Meat
34
°
F
2) Dairy/Deli
34
°
F
3) Produce
a. Processed
36
°
F
b. Unprocessed
45
°
F
B. Frozen
0
°
F
C. Ice Cream
-5
°
F
Single Deck
Multi Deck
ServiceCase
Reach-In
I. Open Display Styles
II. Closed Display Styles
APPENDIX B. – Application
Recommendations
Refrigerated
1.0 Temperature performance is critical for controlling bacteria
growth. Therefore, the following recommendations are included in
the standard. They are based on confirmed field experience over
many years.
1.1 The installer is responsible for following the installation instruc-
tions and recommendations provided by Hussmann for the
installation of each individual type refrigerator.
1.2 Refrigeration piping should be sized according to the equipment
manufacturer’s recommendations and installed in accordance with
normal refrigeration practices. Refrigeration piping should be
insulated according to Hussmann’s recommendations.
1.3 A clogged waste outlet blocks refrigeration. The installer is
responsible for the proper installation of the system which
dispenses condensate waste through an air gap into the building
indirect waste system.
1.4 The installer should perform a complete start-up evaluation prior to
the loading of food into the refrigerator, which includes such items as:
a) Initial temperature performance, Coils should be properly fed with
a refrigerant according to manufacturer’s recommendations.
b) Observation of outside influences such as drafts, radiant
heating from the ceiling and from lamps. Such influence should
be properly corrected or compensated for.
c) At the same time, checks should be made of the store dry-
bulb and wet-bulb temperatures to ascertain that they are
within the limits prescribed by Hussmann.
d) Complete start-up procedures should include checking through
a defrost to make certain of its adequate frequency and length
without substantially exceeding the actual needs. This should
include checking the electrical or refrigerant circuits to make
sure that defrosts are correctly programmed for all the
refrigerators connected to each refrigeration system.
e) Recording instruments should be used to check performance.
APPENDIX C. – Field Recommendations -
Refrigerated
Recommendations for field evaluating the performance of retail
food refrigerators and hot cases
1.0 The most consistent indicator of display refrigerator performance
is temperature of the air entering the product zone (Refrigerated
see Diagram 1, Appendix A). In practical use, the precise
determination of return air temperature is extremely difficult.
Readings of return air temperatures will be variable and results
will be inconsistent. The product temperature alone is not an
indicator of refrigerator performance.
NOTE
: Public Health will use the temperature of the product in
determining if the refrigerator will be allowed to display potentially
hazardous food. For the purpose of this evaluation, product
temperature above the FDA Food Code 1993 temperature for
potentially hazardous food will be the first indication that an
evaluation should be performed. It is expected that all refrigerators
will keep food at the FDA Food Code 1993 temperature for potentially
hazardous food.
1.1 The following recommendations are made for the purpose of
arriving at easily taken and understood data which, coupled with
other observations, may be used to determined whether a display
refrigerator is working as intended:
Appendices