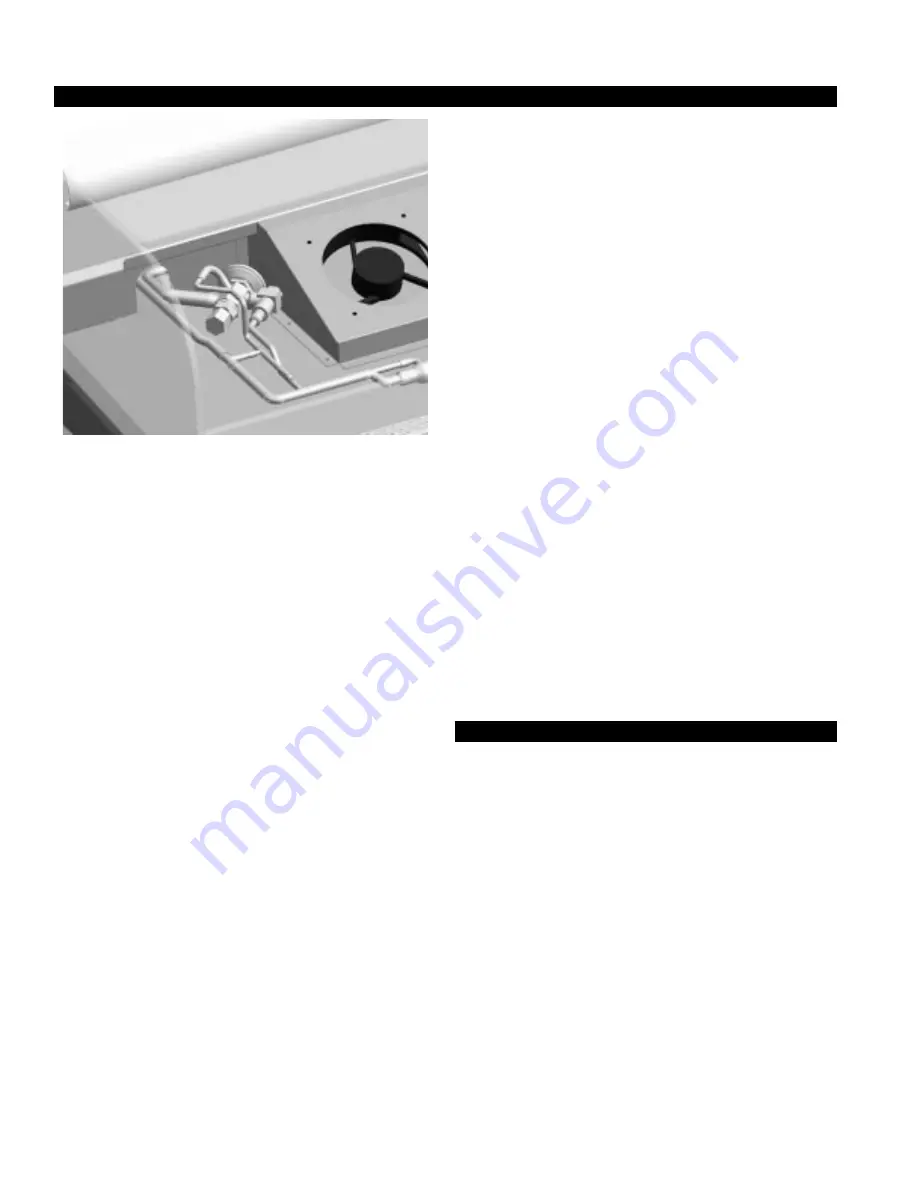
IGSSB-SHVSS-0302
6
REFRIGERATION
Unless otherwise specified on the factory order, remote
and self-contained merchandisers are equipped for
operation on R134A refrigerant. The correct type of
refrigerant will be stamped on each merchandiser’s serial
plate located inside the merchandiser.
Refrigerant Piping
Connection Sizes:
Liquid Line
1/4” OD
Suction Line
3/8” OD
The refrigerant line connections are behind the rear
close-off panel, underneath the drain tub, on the left
hand end of the merchandiser as viewed from the rear.
After connections have been made, seal this outlet
thoroughly. Seal both inside and the outside. We recom-
mend using an aerosol dispensed urethane type of
insulation.Case specification section in the back of the
book for proper duration and frequency. Self contained
cases have individual defrost time clocks. When power
has been applied, set the time clock to the proper
duration and frequency.
The time clock is located behind the front panel under
the case. Turn the clock dial counterclockwise until the
pointer is directed to the current time of day.
Multiplexing - Piping of merchandisers operating on
the same refrigeration system may be run from merchan-
diser to merchandiser through the end frame saddles
provided for this purpose. DO NOT RUN REFRIG-
ERANT LINES THROUGH MERCHANDISERS
THAT ARE NOT THE SAME REFRIGERATION
SYSTEM as this may result in poor refrigeration
control and compressor failure.
Line Sizing - Refrigerant lines should be sized as shown
on the refrigeration legend that is furnished for the store
(not furnished by Hussmann). If a legend has not been
furnished, refer to the Hussmann Application Engineering
Manual for guidance.
Oil Traps - P-traps (oil traps) must be installed at the
base of all suction line vertical risers.
Pressure Drop - Pressure drop can rob the system of
capacity. To keep the pressure drop to a minimum, keep
the refrigerant line run as short as possible using a
minimum number of elbows. Where elbows are required,
use long radius elbows only.
Insulation - The suction and liquid lines should be
clamped or taped together and insulated for a minimum
of 30’ from the merchandiser. Additional insulation is
recommended wherever condensation drippage is
objectionable.
CONTROLS AND ADJUSTMENTS
The objective of the controls and settings listed in this
section is to maximize product shelf life. Not complying
with these instructions will increase spoilage rate due to
drying of the product and could cause sweating on the
front glass if operated too cold.
Allow bakery products to reach store ambient condi-
tions after preparation just prior to display. This is
essential to maximize the shelf life of perishables.