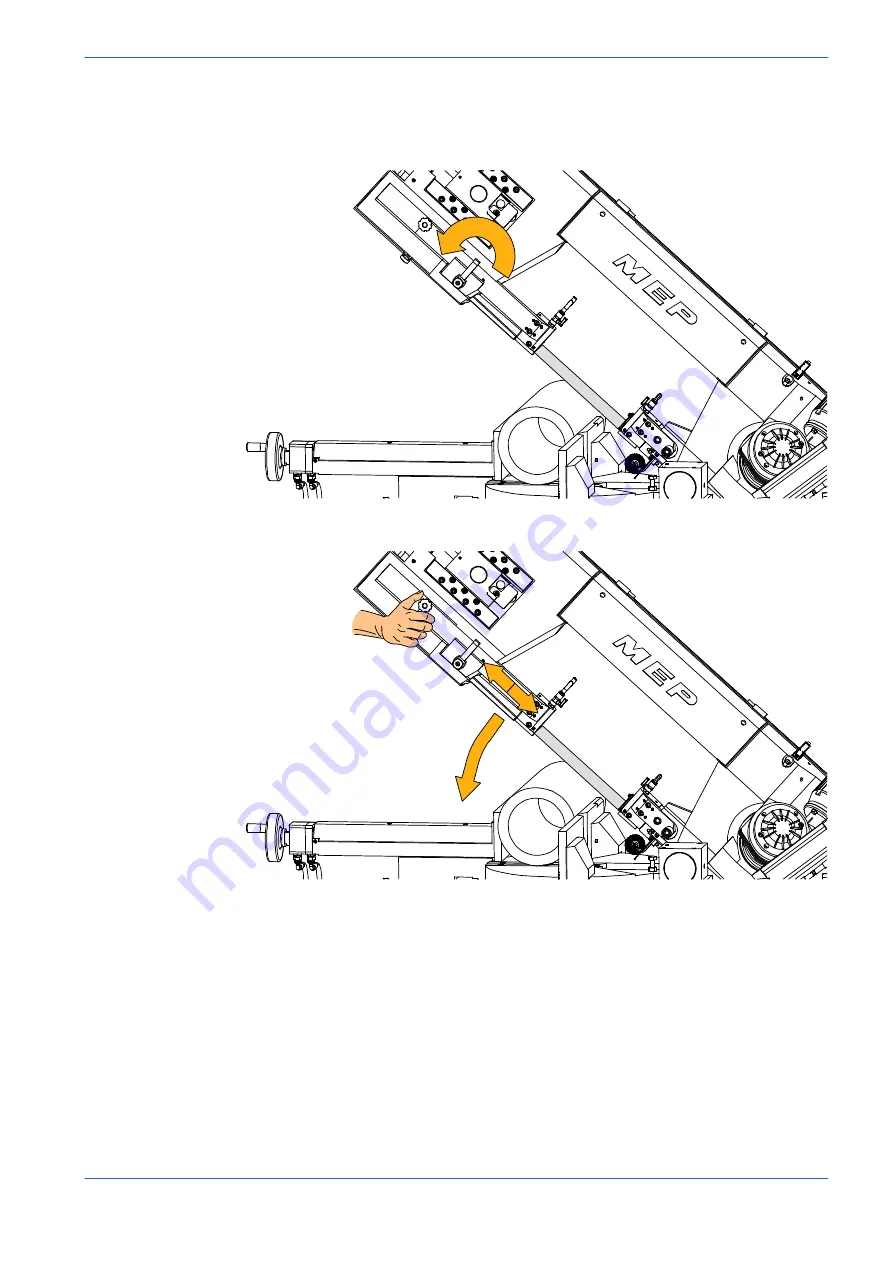
5
−
5
38
Description of machine operation
Position the workpiece on the work table in proximity to the blade down
stroke trajectory and clamp it in the vice;
Slacken the ratchet lever on the sliding shaft of the front blade guide head.
Position the mobile front guide head near the workpiece so that the down
stroke trajectory exceeds the mobile vice jaw.
Tighten the ratchet lever to lock the head slide.
Preliminary check list for cutting operation
To guarantee complete safety during cutting cycles, the operator should work
through a check list of the entire apparatus, checking:
blade tension;
that the blade guide head bracket is locked in the correct position;
that the cutting angle is correct and that the surface to be cut is blocked;
that the work piece is properly clamped in place;
that the blade teeth are correct for the job to be begun;
that the speed selected is right for the kind of piece to be cut;
that all protections are in place and correctly locked;
Summary of Contents for DM-1215
Page 1: ...USE AND MAINTENANCE MANUAL YEAR OF MANUFACTURE ______________ DM 1215 EN ...
Page 2: ......
Page 4: ......
Page 34: ......
Page 53: ...6 7 52 Diagrams exploded views and replace Standardised Wiring Diagrams ...
Page 54: ...6 8 53 Use and maintenance manual DM 1215 ...
Page 55: ...6 9 54 Diagrams exploded views and replace ...
Page 56: ...6 10 55 Use and maintenance manual DM 1215 F6 F7 F8 F3 F4 F5 RT4 ...
Page 57: ...6 11 56 Diagrams exploded views and replace F1 F2 F9 ...
Page 58: ...6 12 57 Use and maintenance manual DM 1215 S4 KSTO S8 S4 K01 ...
Page 59: ...6 13 58 Diagrams exploded views and replace KSTO KSTO RT4 ...
Page 61: ...6 15 60 Diagrams exploded views and replace ...
Page 62: ...6 16 61 Use and maintenance manual DM 1215 ...
Page 63: ...6 17 62 Diagrams exploded views and replace ...
Page 64: ...6 18 63 Use and maintenance manual DM 1215 ...
Page 65: ...6 19 64 Diagrams exploded views and replace ...
Page 66: ...6 20 65 Use and maintenance manual DM 1215 ...
Page 67: ...6 21 66 Diagrams exploded views and replace ...
Page 68: ...6 22 67 Use and maintenance manual DM 1215 ...
Page 69: ...6 23 68 Diagrams exploded views and replace ...
Page 70: ...6 24 69 Use and maintenance manual DM 1215 ...
Page 71: ...6 25 70 Front flywheel assembly ...
Page 74: ...6 28 73 Use and maintenance manual DM 1215 Motor flywheel assembly ...
Page 77: ...6 31 76 Cutting head cover ...
Page 79: ...6 33 78 Vice assembly ...
Page 81: ...6 35 80 Base assembly ...
Page 83: ...6 37 82 Control panel ...
Page 85: ...6 39 84 Fixed work table and turntable ...
Page 88: ...6 42 87 Use and maintenance manual DM 1215 Cylinder unit ...
Page 90: ...6 44 89 Use and maintenance manual DM 1215 Laser and lamp group ...
Page 92: ......
Page 132: ......
Page 136: ......