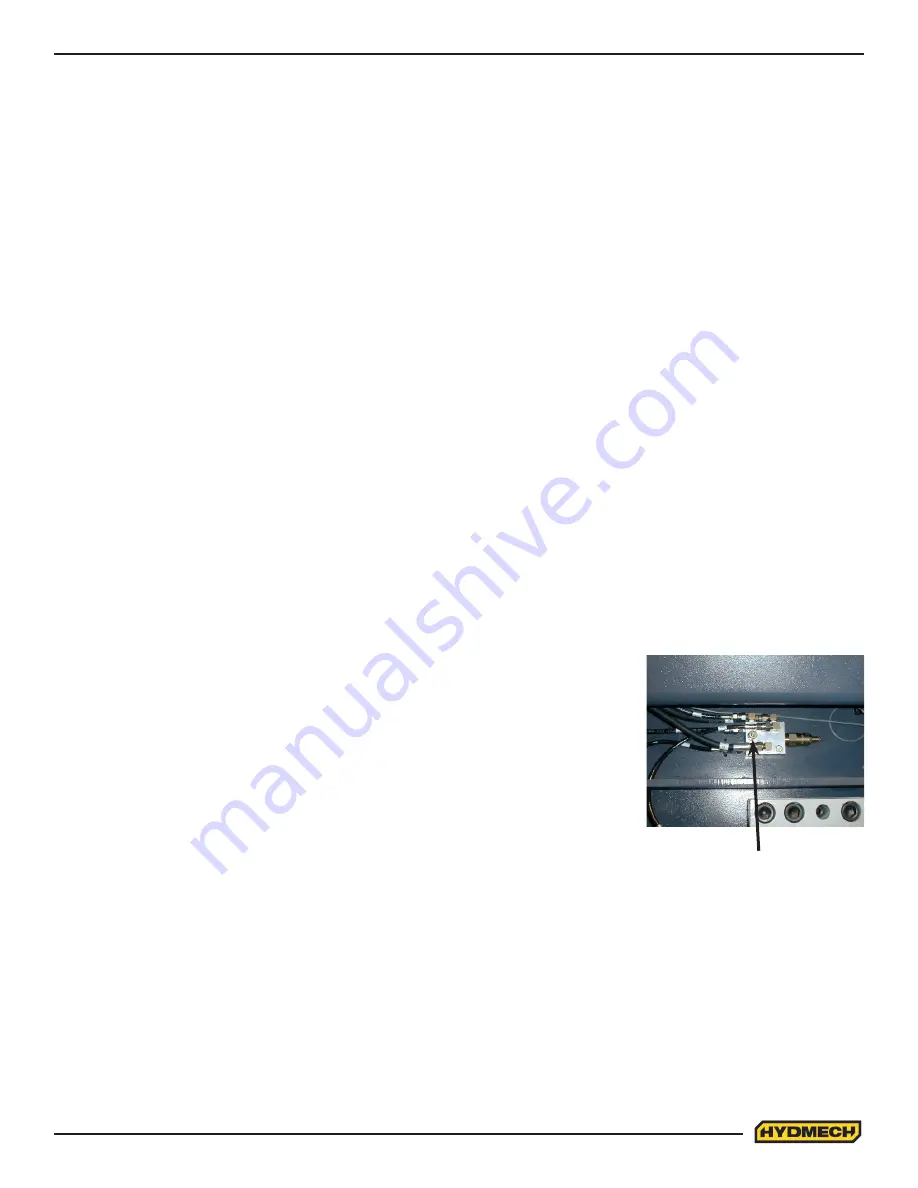
3.7
HYDRAULIC MAINTENANCE
1. OIL FILTER- Ten micron filtration of the oil is provided by a spin on type filter mounted on the tank return line. The
element should be changed after the first 50 hours of operation and then every 500 working hours. See section 5 for
replacement filter element information.
2. HYDRAULIC OIL- Machine hydraulic reservoir is filled with mineral oil Texaco Rando HD46. In case of changing the
brand, hydraulic system should be drained and thoroughly flushed. Following is a list of recommended replacement oils:
•
TEXACO RANDO HD 46
•
CHEVRON ECO Hydraulic oil AW ISO 46
•
MOBIL DTE 25
•
ESSO NUTO H46
•
SHELL TELLUS OIL 46
3. HYDRAULIC OIL LEVEL - Oil level should be maintained in the upper half of the level gauge. Normally the rate of oil
consumption will be very low and it should be unnecessary to add oil more often than at filter changes if at all.
4. HYDAULIC OIL CHANGE - Oil visual inspection should be conducted with every filter change for following signs of
degradation:
•
Milky or hazy oil color
•
Burnt smell
•
Varnish or sludge formation
•
Increased viscosity
If one of the above is observed then oil should be changed. It is recommended to change oil after every 6000
hours of operation or every 2 years.
5. OIL TEMPERATURE - Oil temperature is indicated by a thermometer contained in the level gauge. Oil temperature
during steady operation should stabilize at about 50-55F (28-31 deg C) above room temperature. Thus in a
70F (21 deg C) shop one might expect an oil temperature of about 120F (49 deg C). Oil temperature should never exceed
155F (68 deg C).
6. HYDRAULIC PRESSURE - Hydraulic pressure is factory set and should not require any further attention. For correct
pressure see hydraulic schematic.
7. BLADE TENSION – Blade tension pressure is factory set and should not require
any further attention. For correct pressure see hydraulic schematic.
8. CARBIDE PRESSURE - Carbide lock pressure is factory preset:
•
H-18SV 300 – 400 PSI
•
H-22SV 150 – 200 PSI
The pressure gauge is not provided. There is a separate port to hook up a gauge if
setting needs to be verified or corrected.
CLEANLINESS
The heavy duty design should endure heavy operating conditions and provide the customer with flawless machine
performance. To extend good performance some care is required especially as cleanliness is concerned.
The following areas should be kept clean:
•
Control console free of dirt and grease.
•
Door charts free of dirt and grease.
•
Wheel boxes free of chips.
•
Blade guides free of chips.
•
Out-feed table free of chips.
•
A large chip build-up should be avoided in the base of the saw.
NOTE:
All parts must be cleaned before any repair service can be performed on them.
Gauge Port
Summary of Contents for H18 A
Page 2: ......
Page 12: ...0 8 Item 391938 Chip Augar Item 391335 Item 391340 ...
Page 13: ...0 9 Item 391397 Item 392801 Fixed Vise Shuttle Vise Item 392801 ...
Page 14: ......
Page 16: ...1 2 LIFTING INSTRUCTIONS ...
Page 59: ...4 1 ELECTRICAL SCHEMATICS SEE PDF ON ATTACHED CD SECTION 4 ELECTRICAL ...
Page 60: ...4 2 ...
Page 64: ...6 2 ...
Page 65: ...7 1 SECTION 7 OPTIONS OPTIONAL ASSEMBLY DRAWINGS SEE PDF ON ATTACHED CD ...
Page 66: ...7 2 ...
Page 69: ...8 3 H18SV H22SV LIFTING INSTRUCTIONS ...
Page 70: ...8 4 H18SV LAYOUT ...
Page 71: ...8 5 H22SV LAYOUT ...
Page 72: ...8 6 ...
Page 74: ...9 2 ...