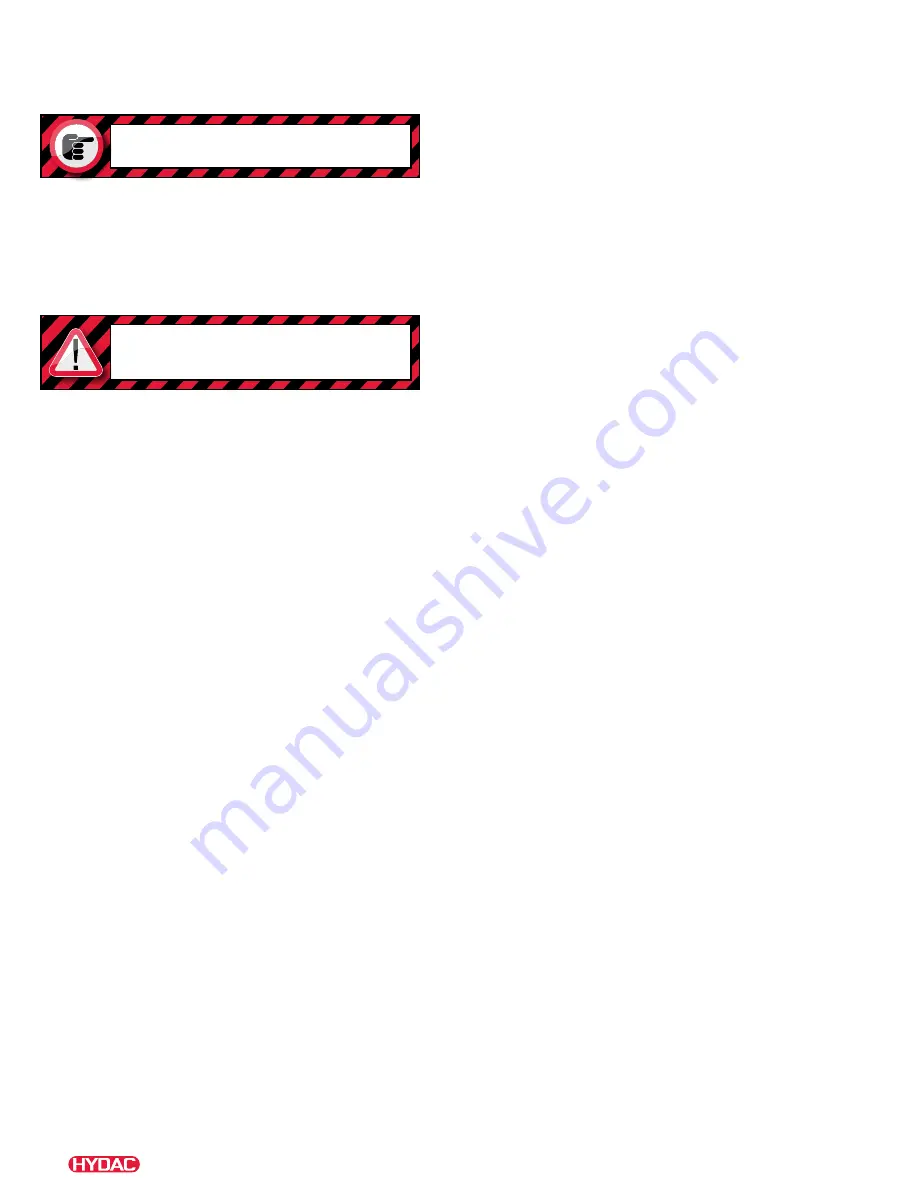
4
FIL1609-1828 / 04.19
FILTER MAINTENANCE
6. Maintenance Instructions
6.1 User Instructions for Filters
This symbol is followed by user tips and
particularly useful information.
•
This pressure equipment must only be put into operation in
conjunction with a machine or system.
•
The pressure equipment must only be used as stipulated in the
operating instructions of the machine or system.
•
This pressure equipment must only be operated using hydraulic or
lubricating fluid.
•
It is the responsibility of the operator to comply with the water
regulations of the country concerned.
This symbol denotes safety precautions,
the non-observance of which can endanger
persons and the environment.
CAUTION
•
The user must take appropriate action (e.g. venting) to prevent the
formation of air pockets.
•
Repairs, maintenance work and commissioning must only be carried
out by trained personnel.
•
Allow the pressure equipment to cool before handling.
•
The stipulations of the operating instructions of the machine or the
system must be followed.
•
Statutory accident prevention regulations, safety regulations and
safety data sheets for fluids must be observed.
•
Filter housing must be grounded.
•
When working on, or in the vicinity of, hydraulic systems, open flames,
sparks and smoking are forbidden.
•
Hydraulic oils and water-polluting fluids must not be allowed to
enter the soil or watercourses or sewer systems. Please ensure safe
and environmentally friendly disposal of hydraulic oils. The relevant
regulations in the country concerned with regard to ground water
pollution, used oil and waste must be complied with.
•
Whenever work is carried out on the filter, be prepared for hot oil
to escape which can cause injury or scalding as a result of its high
pressure or temperature.
DANGER!
•
Caution: pressure equipment! Before any work is carried out on the
pressure equipment, ensure the pressure chamber concerned (filter
housing) is depressurized.
•
On no account must any modifications (welding, drilling, opening by
force...) be carried out on the pressure equipment.
•
When using electrical clogging indicators, the electrical power supply
to the system must be switched off before removing the clogging
indicator connector.
6.2 Maintenance, General
This section describes maintenance work which must be carried out
periodically. The operational safety and life expectancy of the filter, and
whether it is ready for use, depend to a large extent on regular and careful
maintenance.
6.3 Maintenance Measures
•
Spare parts must fulfil the technical requirements specified by the
manufacturer.
This is always ensured when using original HYDAC spare parts.
•
Keep tools, working area and equipment clean.
•
After disassembling the filter, clean all parts, check for damage or
wear and replace parts if necessary.
•
When changing a filter element, a high level of cleanliness must be
observed.
6.4 Interval Between Element Changes
In principle we recommend that the filter element is changed every 6
months or upon indication, whichever occurs first.
We recommend installing the filter with a clogging indicator (visual and/or
electrical or electronic) to monitor the filter element.
When no clogging indicator has been installed, we recommend changing
the elements at specific intervals.
(The frequency of changing the filter
elements depends on the filter design and the conditions under which the filter
is operated)
. When filter elements are subject to high dynamic loading it
may prove necessary to change them more frequently. The same applies
when the hydraulic system is commissioned, repaired or when the oil is
changed
The standard clogging indicators only respond when fluid is flowing
through the filter. With electrical indicators the signal can also be
converted into a continuous display on the control panel. In this case
the continuous display must be switched off during a cold start or after
changing the element.
If the clogging indicator responds during a cold start only, it is possible
that the element does not yet need to be changed.
Customer Information in respect of Machinery Directive 2006/42/EC
Hydraulic filters are defined as fluid power parts / components and are
therefore excluded from the scope of the Machinery Directive, sections
1.4.1 - 1.4.3. They do not bear the CE mark.
Before using these components, ensure compliance with the
specifications provided by HYDAC Technology Corporation. The
specifications also contain information on the relevant essential health
and safety requirements (based on Machinery
Directive 2006/42/EC).
We hereby declare that the filters are intended to be incorporated into
machinery within the terms of the Directive 2006/42/EC. It is prohibited to
put the filters into service until the machinery as a whole is in conformity
with the provisions of the Machinery Directive.
Service address
HYDAC Technology Corporation
Filter Division
2260 City Line Road
Bethlehem, PA 18017
+1.610.266.0100
NOTE
The information in this brochure relates to the operating conditions and applications
described.
For applications or operating conditions not described, please contact the relevant
technical department.
Subject to technical modifications.