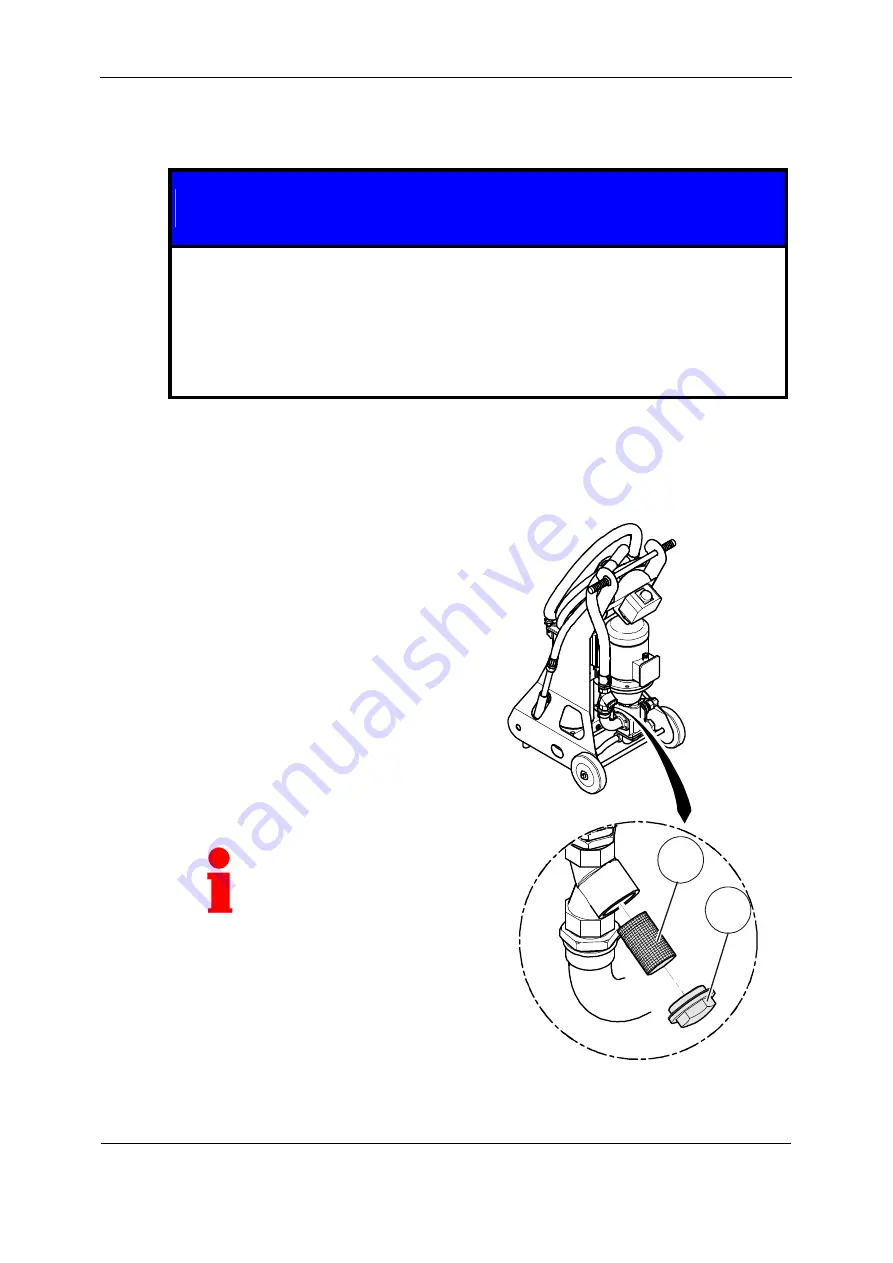
FCM Series
Clean the suction strainer.
Clean the suction strainer.
NOTICE
Operation without a suction strainer
Pump is disrupted
►
The FCU may not be operated without the suction strainer.
►
Clean the suction strainer regularly.
To protect the pump from coarse contamination particles and other foreign bodies, a
dirt trap with a strainer insert is fitted at the pump inlet.
This strainer insert must be cleaned at regular intervals, e.g. by flushing it with
solvent or blow-flushing it with compressed air.
1. Unscrew the screw plug (1)
counterclockwise with an open-jaw
wrench (wrench width 50 mm).
2. Remove strainer insert (2) and
clean it.
3. Check strainer insert (2) and the
seal ring on the screw plug for
damage and replace if necessary.
4. Insert strainer insert (2).
5. Screw in the screw plug clockwise
and tighten it with the open-jaw
wrench (wrench width 50 mm).
6. After start-up, check the suction
strainer fittings for leaks.
The entry of air causes a loud
noise and can damage the pump.
1
2
HYDAC FILTER SYSTEMS GMBH
en(us)
Page 32 / 40
Bewa FCM 3160267d en-us 2012-01-24.doc
2012-01-24