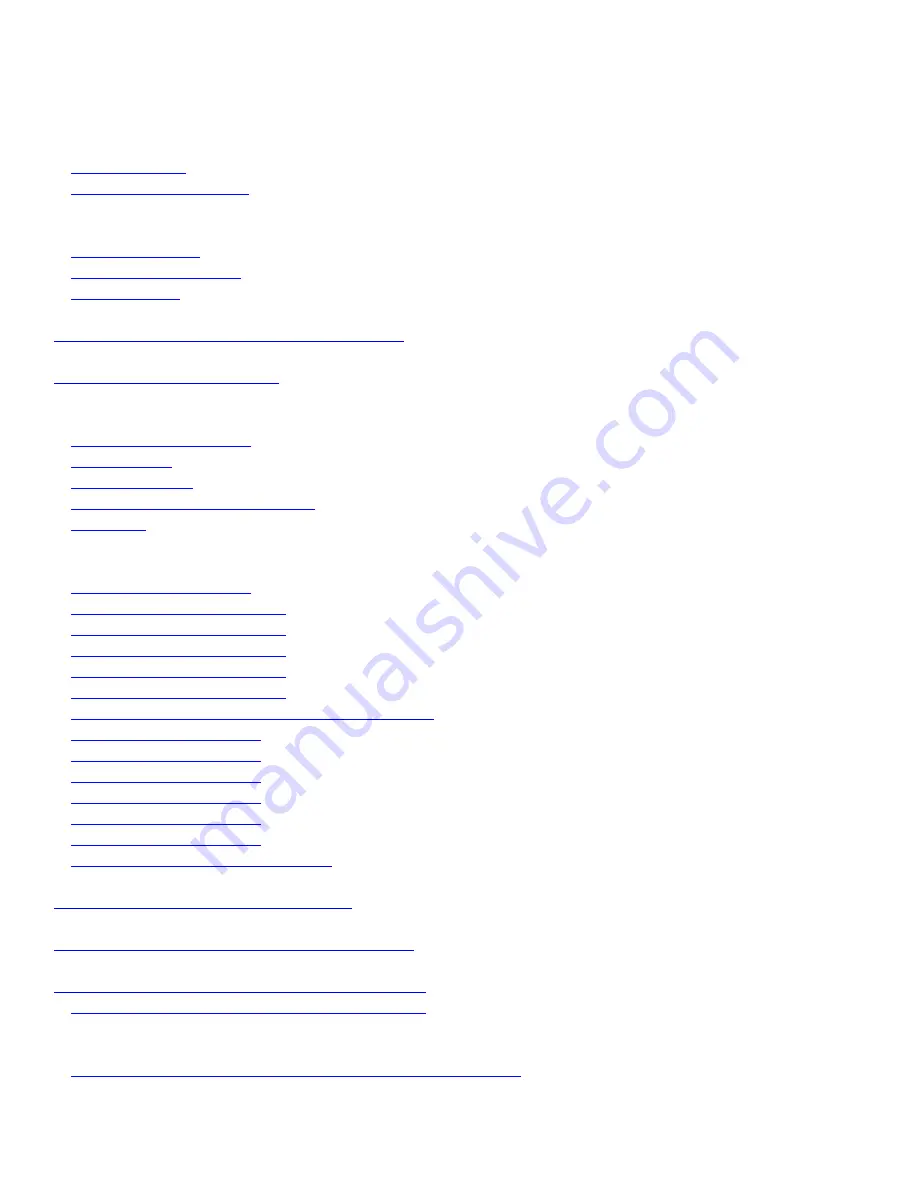
HYDRO-GEAR 310-0500/0750 SERVICE MANUAL
Table of Contents – Page 1 of 1
INTRODUCTION/GENERAL DESCRIPTION
MAINTENCE
TROUBLESHOOTING DIAGRAM 310-500/0750 IHT
MINOR REPAIRS
MAJOR REPAIRS
RECONDITIONING AND REPLACEMENT OF PARTS
OIL FILL & START-UP PROCEDURES
310-0500 PARTS DRAWING & PARTS LIST
310-500/0750 IHT PARTS DRAWING & PARTS LIST
PARTS DRAWING & PARTS LIST 310-0500/0750 IHT
PARTS DRAWING & PARTS LIST 310-500/0750 IHT
PRODUCT LINE - HYDRO-GEAR