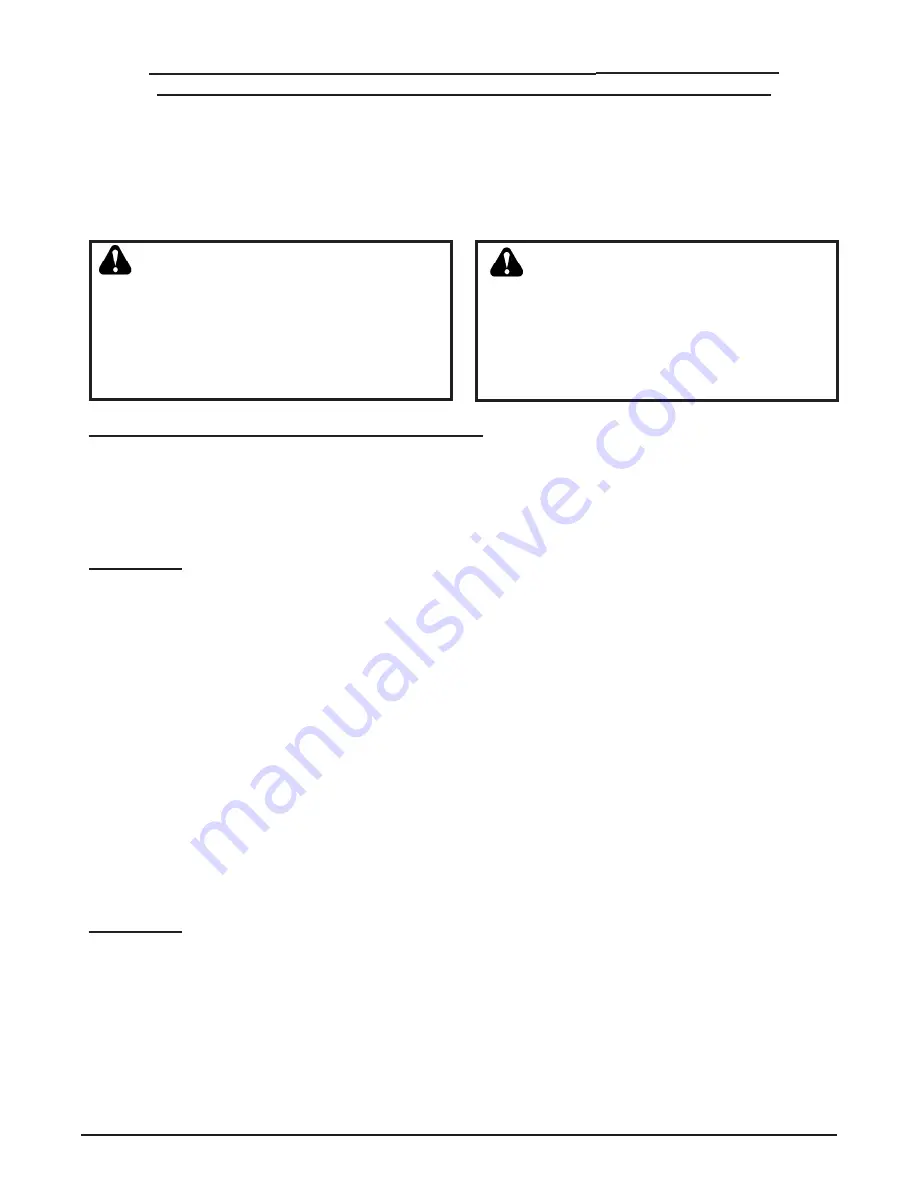
16
P Series
Description: P Series Flow Test Kit (Part Number 70661)
(Part Number 70661 Supersedes Part Numbers 70511 and BB-76810)
Purpose:
The design purpose of the P Series Flow Test Kit is to allow the customer to isolate the pump from the
wheel motor and determine if the pump is acceptable. The following information can be used to install and test the
pump by simulating a wheel motor load.
CERTAIN PROCEDURES REQUIRE THE VEHICLE ENGINE
TO BE OPERATED AND THE VEHICLE TO BE RAISED OFF
OF THE GROUND. TO PREVENT POSSIBLE INJURY TO
WARNING
DO NOT ATTEMPT ANY ADJUSTMENTS WITH THE
ENGINE RUNNING. USE EXTREME CAUTION WHILE
WORKING IN OR AROUND ALL VEHICLE LINKAGE!
WARNING
INSTALLATION AND TESTING PROCEDURES:
1.
Disconnect the system hoses at the wheel motor, or system hoses from the pump and connect the P Series
Flow Test Kit. (Special care should be taken to prevent contamination debris from entering pump or wheel
motor system ports).
Note:
Using the Bi-Directional Flow Test Kit, determination of directional flow is not necessary. The flow meter
may be connected in either direction into the forward and reverse high pressure system lines.
CAUTION:
Ensure all fittings and hoses are attached securely. This test is being completed on the
vehicle’s high pressure system lines. Failure to perform this properly could result in bodily injury.
TESTING PROCEDURES:
1.
Raise the drive tires off the ground. Block the remaining tires on the ground to prevent accidental vehicle
movement.
2.
Open the restriction valve all the way.
3.
Make certain all external pump directional control stops are removed or backed off on the vehicle linkage to
obtain full pump directional control arm travel.
4.
Start the engine and engage the drive pulley if necessary.
5.
Bring the engine to maximum operating speed.
(This should not exceed 3600 rpm input speed on the PC, PL, PG, PE, PJ and PK Series pumps)
(This should not exceed 3400 rpm input speed on the PR Series pumps)
(This should not exceed 2600 rpm input speed when testing the PW and PY Series pumps)
Engine speed adjustment may be necessary to obtain 2600 rpm.
CAUTION:
Damage to the flow meter and/or re-calibration may result from testing at input speeds
that exceed 2600 rpm on the PW and 3400 rpm on the PR Pumps.
6.
With the directional control lever (on the vehicle) for the pump being tested, move the control arm in full
forward motion. (It may be necessary to lock the control arm into full forward position to prevent false
readings).
7.
Operate without any load for approximately 30 seconds to 1 minute. This allows the system oil temperature
to rise.
P-SERIES FLOW TEST KIT INSTRUCTIONS -
BLN-51334 April 2011
(This Instruction Sheet supersedes all previous flow testing instruction)
Summary of Contents for HGM-H Series
Page 1: ...BLN 0043 January 2018 HGM H Series Motor Service and Repair Manual ...
Page 25: ...24 HGM H HGM H MOTOR EXPLODED VIEW ...
Page 29: ...HEMTM Series Motor Service and Repair Manual BLN 0083 January 2018 ...
Page 52: ...PRM MOTOR Service and Repair Manual ...
Page 56: ...PRM 3 EXTERNAL FEATURES PRM MOTOR Figure 1 PRM External Features ...
Page 77: ...24 PRM SECTION 8 PARTS LIST Figure 48 MA04K030 ...
Page 81: ...BLN 50231 January 2018 BDP 10L PL Hydrostatic Pump Service and Repair Manual ...
Page 82: ......
Page 83: ......
Page 84: ......
Page 85: ......
Page 86: ......
Page 87: ......
Page 88: ......
Page 89: ......
Page 90: ......
Page 91: ......
Page 92: ......
Page 95: ......
Page 96: ......
Page 97: ......
Page 98: ......
Page 99: ......
Page 100: ...HGM 12P LSHT Wheel Motor Service and Repair Manual BLN 52197 January 2018 ...
Page 102: ...2 Exploded view HGM P ...
Page 117: ...HGM E LSHT Wheel Motor Service and Repair Manual BLN 52198 January 2018 ...
Page 144: ...2 P Series EXTERNAL FEATURES PC SERIES Figure 1 PC Pump with Standard Charge Pump ...
Page 146: ...4 P Series EXTERNAL FEATURES PJ SERIES Figure 3 PJ Pump with Standard Charge Pump ...
Page 147: ...5 P Series Figure 4 PK Pump With Standard Charge Pump EXTERNAL FEATURES PK SERIES ...
Page 176: ...34 PC Series Figure 16 PC Pump BOXES INDICATE ITEMS INCLUDED IN Kit Number ...
Page 192: ...52 PG PE Series Figure 17 PG PE Pump BOXES INDICATE ITEMS INCLUDED IN KITS Kit Number ...
Page 208: ...70 PJ Series Figure 17 PJ Pump BOXES INDICATE ITEMS INCLUDED IN Kit Number ...
Page 224: ...88 PK Series Figure 17 PK Pump BOXES INDICATE ITEMS INCLUDED IN Kit Number ...
Page 240: ...106 PR Series Figure 17 PR Pump BOXES INDICATE ITEMS INCLUDED IN KITS Kit Number ...
Page 261: ...HGM C LSHT Wheel Motor Service and Repair Manual BLN 52690 January 2018 ...