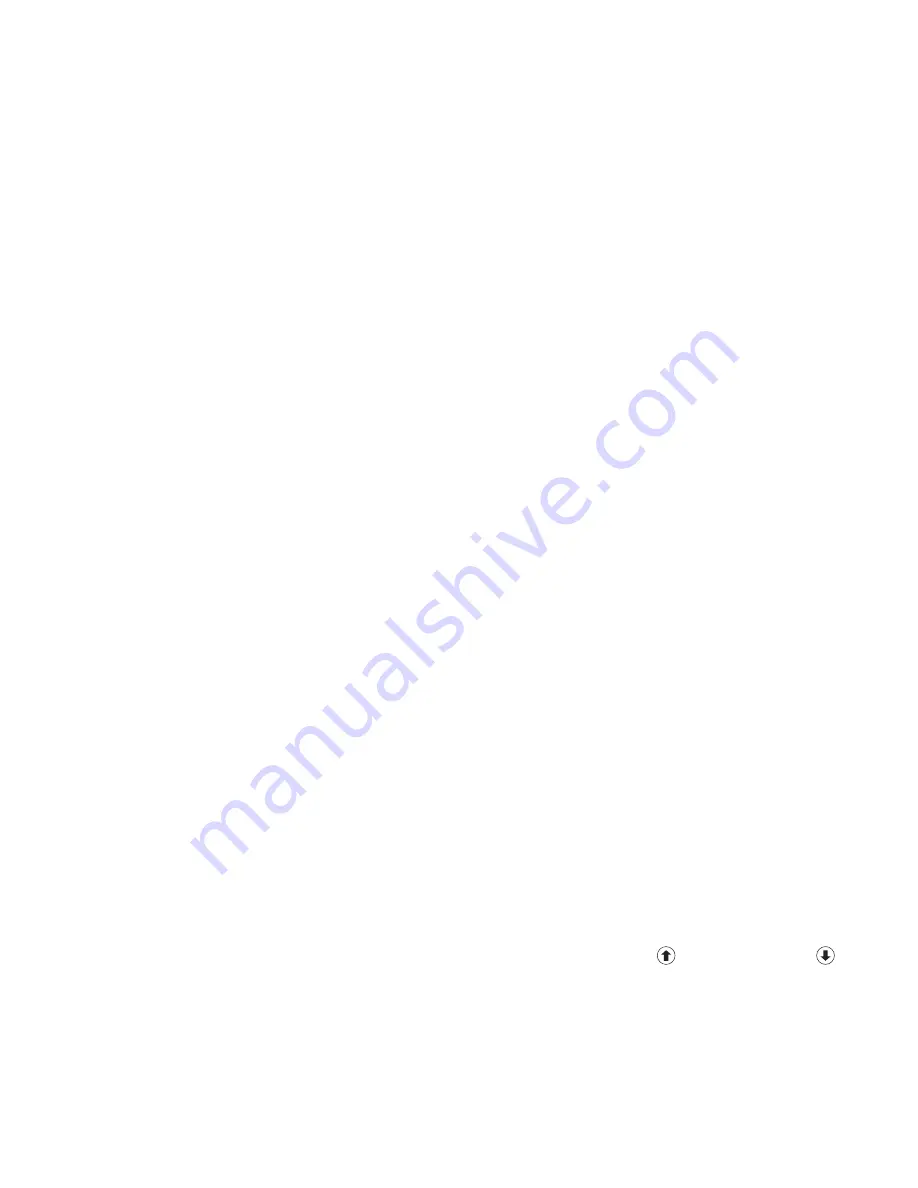
13
VII. REFERENCE TERMS
1.
Contact
– On/off channel used as an alarm output. Also referred to as a relay.
2.
Compound Loop Control
– Refers to the P.I.D. control method. This method controls chemical feed rate
using both fl ow and residual/other (proportional and setpoint) inputs. The method essentially reacts in
proportion to the fl ow input, while it also adjusts the chemical feed rate to maintain a (residual/other) set
point.
3.
Dead Band
– This is a dead band around the set point. As long as the residual/other reading is within (+ or -)
this amount from the set point, the device will consider the system to be at set point. This is used to avoid
excessive, continual adjustment of the valve position that would reduce the life of the mechanical parts.
4.
Dosage
– In the context of fl ow control dosage this is a factor that is multiplied to the incoming fl ow signal.
For example, if incoming fl ow signal is at 50% (12 mA) and the dosage is set to 2.0 then the HC-220 will
adjust chemical feed to 100% (in Flow Pacing Control) or in the same example if dosage is set to 0.5 the
HC-220 will adjust chemical feed to 25% (in Flow Pacing Control).
5.
Filter
– In the context of input signal (PV1 or PV2) fi lter time this is a time over which the signal will be
continually averaged. This is used to smooth out the input signal and reduce motion of the valve that
could be caused by rapid fl uctuations of the input signals (electrical noise or other rapid signal fl uctuations).
6.
Flow Pacing Control
– Refers to the proportional control method. In this method the valve adjusts
chemical feed rate in proportion to input signal.
7.
Full Scale (In terms of Input Full Scale)
– The value (in %, Flow, Residual, or other expressed in appro-
priate units) represented by a 20 mA (or 5 V) input signal.
8.
Integral
– A factor used in calculation of adjustments to chemical feed rate in both Residual/Other and
Compound Loop Control. This value ranges between 0 and 100%. Essentially the program makes a
calculation of how much the chemical feed rate needs to be adjusted in order to reach set point and this
factor. The integral setting determines what percentage of this adjustment will be done in each step (i.e.,
if it is set to 15% then the valve will move 15% of the calculated amount). If the integral is set at 0% it
will never move. If the integral is set at 100% it will probably adjust too much each time and continually
overshoot the set point.
9.
Lag Time
– In the context of Residual/other lag time this is the time that elapses between a change in
chemical feed rate and the change in input signal PV2 from the Residual/Other analyzer (considering a
constant water fl ow). This time is the sum of the time it takes the water to travel from the injection point
to the analyzer plus the time it takes the analyzer to react to a change.
10.
Minimum (In terms of Input Minimum)
– The value (in %, Flow, Residual, or Other expressed in ap-
propriate units) represented by a 4 mA (or 1 V) input signal.
11.
Mode
– In terms of the three modes of the HC-220. (See Section I.1)
12.
ORP
– Oxidation Reduction Potential. The units of measure are mV. It can be positive and negative.
In terms of the HC-220, discussion is focused on the 4-20mA or 1-5V signal representing the ORP value.
13.
Parameter
– In this manual, this term refers to that which is shown on the display screen simultaneously.
The HC-220 is moved from one parameter to the next using the “up arrow”
and “down arrow”
keys.
14.
PO1 (Process Output 1)
– Represents the chemical feed through the valve.
15.
Proportional
– Equivalent to Flow Pacing. The valve reacts in proportion to the incoming signal on
channel PV1.
16.
PV1 (Process Variable 1)
– Refers to analog input one. Normally this is used for the proportional input
signal.