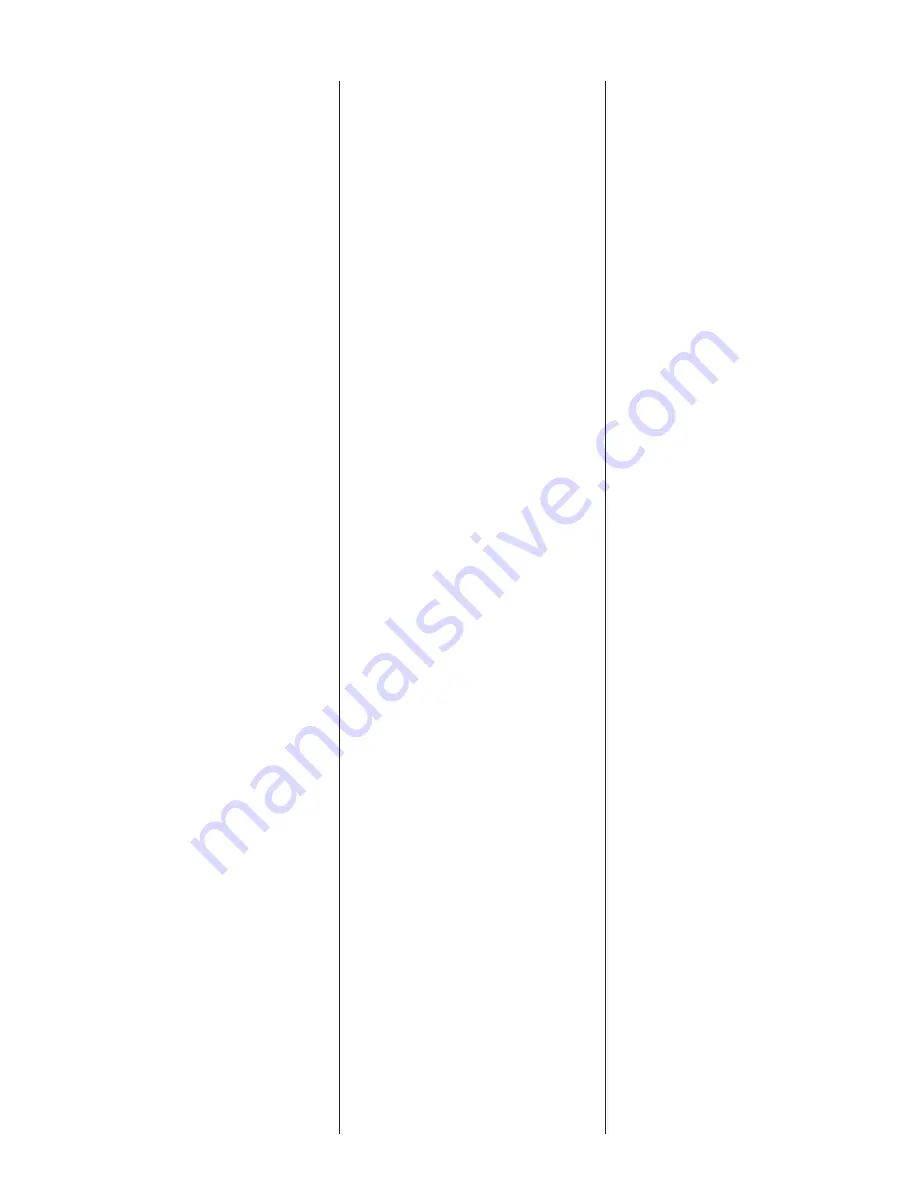
b. Floats may be miswired to
control panel. Check float
type (N.O. or N.C.) and
hook up by re fer ring to the
schematic. If the start and
stop floats are hooked in
reverse, pump will short
cycle and will not pump the
level down.
1. Is water level in the
sys
tem high enough to
ac ti vate the floats?
2. If there is enough water
in the system (with the
power turned off), mark
and disconnect the off
and on floats. Next,
install jumper wires in
the terminal blocks for
off and on floats. Turn
power back on, put H-O-
A switch in Auto and see
if pump runs.
3. If pump runs with
jumper, problem is with
floats. Remove jumpers
and troubleshoot floats
with ohmmeter.
4. If pump does not run
in Auto mode with
jumpers, check Auto
circuit wiring in panel.
3. Pump runs, but run light
does not energize.
a. Re
move light and check
with an ohmmeter.
b. Check run light wir ing.
4. Pump runs but does not
pump down the wet well.
a. On three phase only,
pump rotation may be
wrong. Wiring of pump to
con
trol pan
el may be
reverse sequenced.
b. Impeller may be dragging in
volute due to sol
ids. High
am per age
draw
would
identify this.
c. Refer to the pump manual
for other possibilities such
as closed discharge gate
valve, etc.
5. Severe humming/chat ter ing
of contactors and control
relays.
a. There may be low voltage.
Check voltage at primary
and secondary of control
transformer us
ing a
volt me ter. This low voltage
condition may cause severe
chat
ter
ing and burnout of
contacters and relays.
b. Contactor may have dust
around magnet of coil
struc
ture. Dry or clean
as re quired.
c. Check voltage to the
control panel. Contactors
require a minimum of 85%
of full volt
age to pull
in without chatter. If the
problem is a re
cur
ring
one, measure voltage with
recorder on a 24 hour basis.
d. Make sure the floats are
locat
ed away from any
turbu lence.
e. Dry out the junction box
(if furnished); moisture
in the junction box may
cause relays to energize
intermittent ly.
6. Short cycling pump.
a. Check float controls.
7. Run light stays on.
a. Selector switch may be in
the Hand position.
8. Nuisance tripping of
over
load on motor starters
or cir cuit break ers.
a. Check pump amp draw with
amp probe and compare to
nameplate amps on pump.
b. The impeller may be locked
up due to excessive debris
or solids.
c. Possible motor failure (fault
in windings).
d. Pump may be miswired to
ter mi nal block.
e. Voltage and current
unbalance. Three phase
only.
Voltage un bal ance on three
phase power sources can
cause motor current to
become
un bal anced
and
exces
sive heating will
re sult.
Trip ping
of
the
over
load protectors and
premature motor failures
can be expected if the
current unbalance exceeds
five percent.
Percent Maximum
Current
Current
=
Difference from x 100
Unbalance Average
Current
_______________
Average Current
To determine if motor current
un
bal
ance is a function of the
motor or the power supply:
1. Label the leads and
the ter mi nals 1, 2, and 3
respectively.
2. Record the amperage for
each lead.
3. Move each lead to the
next terminal (1 to 2, 2 to
3, 3 to 1).
4. Again read the amperage
of each lead.
5. Move each lead to the
next terminal (1 to 3, 2
to 1, 3 to 2).
6. Again read the amperage
of each lead.
5
Summary of Contents for Novus 1000 Series
Page 11: ......