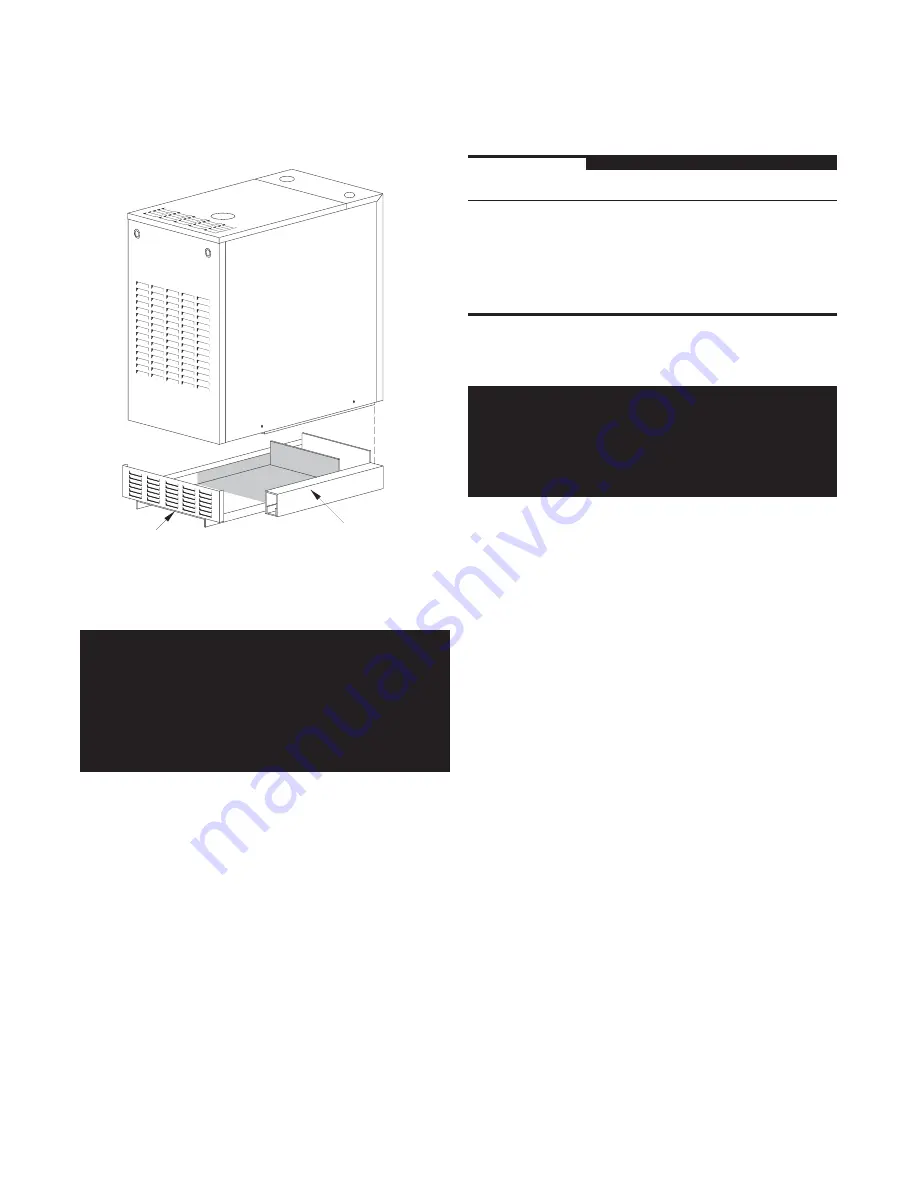
Page 6
HV BOILER
INSTALLATION & OPERATING INSTRUCTIONS
FRONT GRILL
SPECIAL BASE
INPUT BTUH
Fresh Air
1⁄4" Wire
Metal
Wooden
Duct Size
Mesh Screen
Louvers
Louvers
3" x 12"
144,000
108,000
36,000
8" x 8"
256,000
192,000
64,000
8" x 12"
384,000
288,000
96,000
8
1
⁄
2
" x 16"
512,000
384,000
128,000
TABLE 2 Combustion Air Duct Sizing
COMMON VENT SYSTEMS
WARNING
:
Do not connect this boiler or any other
appliance using a mechanical draft system under
positive pressure to a common vent system! Failure
to comply with this warning could result in the
accumulation of carbon monoxide gas which can
cause severe personal injury or death!
If an existing appliance is removed from a common venting
system, the common venting system may then be too large for
the proper venting of the remaining appliances connected to
it. At the time of removal of an existing boiler, the following steps
shall be followed with each appliance remaining connected to
the common venting system placed in operation, one at a
time, while the other appliances remaining connected to the
common venting system are not in operation.
Au moment du retrait d’une chaudière existante, les mesures
suivantes doivent être prises pour chaque appareil toujours
raccordé au système d’évacuation commun et qui fonctionne
alors que d’autres appareils toujours raccordés au système
d’évacuation ne fonction-nent pas: système d’évacuation.
1.
Seal any unused openings in the common vent system.
Sceller toutes les ouvertures non utilisées du sys-tème
d’évacuation.
2.
Visually inspect the venting system for proper size and
horizonal pitch and determine that there is no blockage or
restriction, leakage, corrosion and other deficiencies which
could cause an unsafe condition.
Inspecter de façon visuelle le système d’évacu-ation pour
déterminer la grosser et l’inclinaison horizontale qui
conviennent et s’assurer que le système est exempt
d’obstruction, d’étranglement de fruite, de corrosion et autres
défaillances qui pourraient présenter des risques.
FIG. NO. 3 Special Base Installation
COMBUSTION AIR
WARNING
:
This boiler must be supplied with
combustion air in accordance with Section 5.3, Air for
Combustion & Ventilation, of the latest edition of the
National Fuel Gas Code, ANSI Z223.1/NFPA 54 and
all applicable local building codes. Failure to provide
adequate combustion air for this appliance can result
in excessive levels of carbon monoxide which can
result in severe personal injury or death!
To operate properly and safely this boiler requires a continuous
supply of air for combustion. Oxygen is used by the burners in
the boiler to burn the gas. An adequate supply of outside air
must be available to replace the air used by this process.
Older houses often have enough “leakage” to provide an
adequate amount of combustion air provided that the demand
for combustion air is not too great. Homes that are relatively
new or “tight” will most likely require the installation of a fresh
air duct or other means of providing air for combustion. Any
home utilizing other gas burning appliances, a fireplace, wood
stove or any type of exhaust fan must be checked for adequate
combustion air when all of these devices are in operation at
one time. Sizing of an outside air duct must be done to meet
the requirements of all such devices, see
Table 2
.