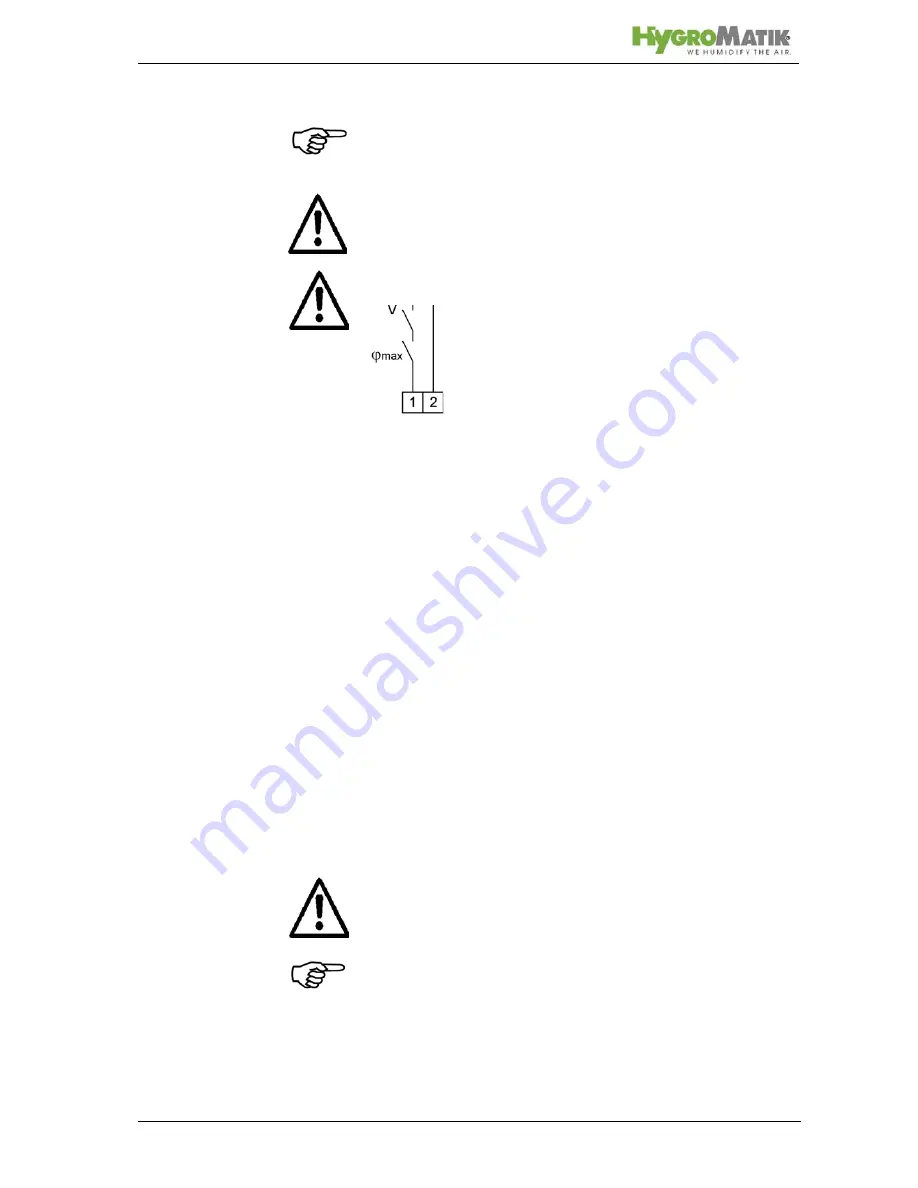
Page 40
7.2
Safety Interlock
Note:
Install contact interlocks, i.e. max. hygrostat, vane relay,
pressure controller, air interlock, in series between terminals 1
and 2.
Warning:
A max-hygrostat should be installed in the safety inter-
lock. The max-hygrostat acts as a safety device in case the
humidity sensor malfunctions.
Warning:
Contacts laid between terminals 1 and 2 must be
potential free and rated for 230V switches.
7.3
Wiring Diagram
Please remove the wiring diagram from the technical manual
supplied with the control used with your humidifier. Every steam
humidifier comes with one technical manual for the unit and one
for the control.
7.4
Electrical Installation Checklist
Perform electrical installation checks in compliance with cus-
tomer site requirements and public power utility regulations:
Is the power grid voltage compatible with the voltage on
the name plate?
Have all electrical connections been made according to
the terminal connection diagram?
Have all electrical cable and plug connections been
properly tightened?
Are all electrical socket connections secure?
Is the unit grounded?
After this check the unit can be switched on.
Warning:
The unit must be closed and locked. This guarantees
that the cover is grounded. (only humidifier type HyLine and
MiniSteam)
Note:
For initial operation, control, service, malfunctions, and
circuit diagrams, consult the operation instructions for the Hygro-
Matik-controls.