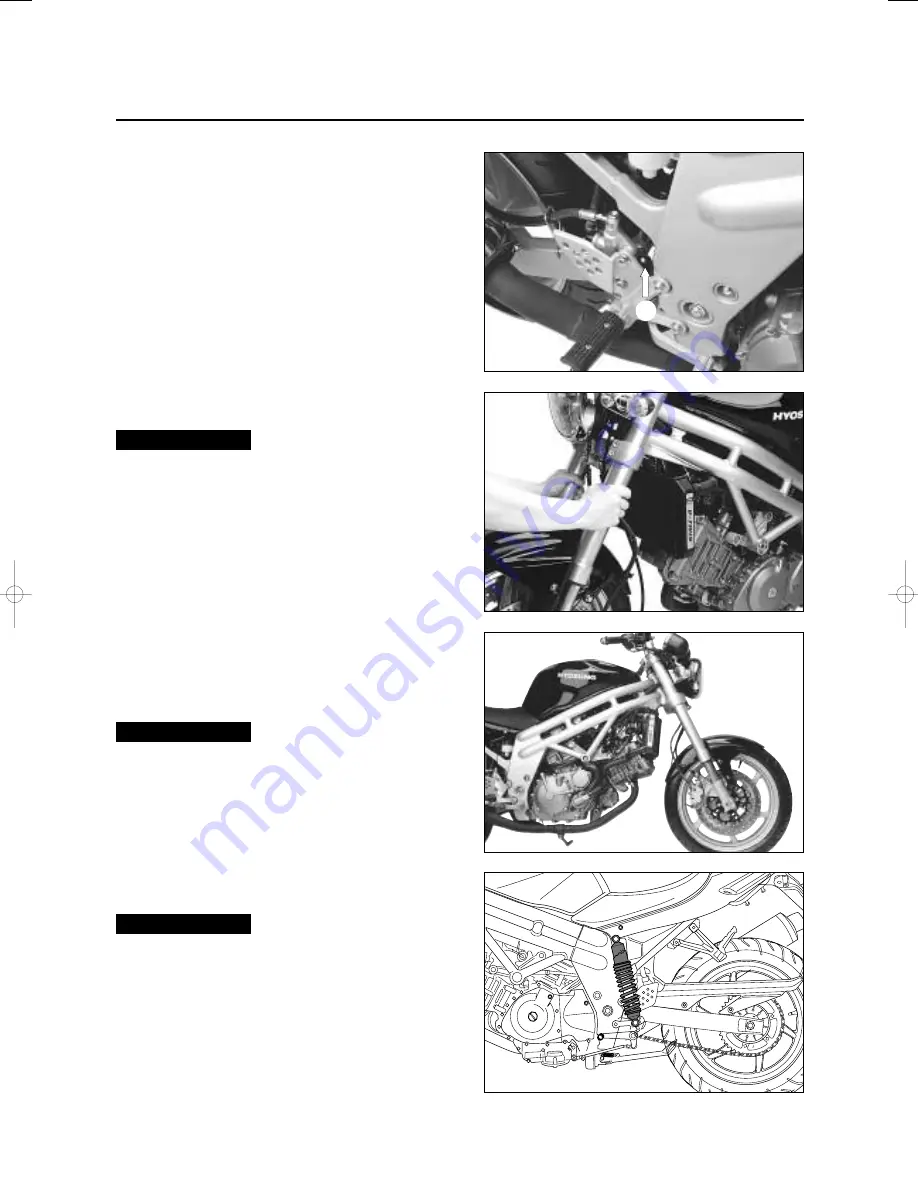
STEERING
Steering should be adjusted properly for smooth turning
of handlebars and safe running. Overtight steering pre-
vents smooth turning of the handlebars and too
loose steering will cause poor stability. Check that
there is no play in the steering stem while grasping
the lower fork tubes by supporting the machine so that
the front wheel is off the ground, with the wheel straight
ahead, and pull forward. If play is found, perform
steering stem nut adjustment as described in page
7-25 of this manual.
FRONT FORK
Inspect the front forks for oil leakage, scoring or scratch-
es on the outer surface of the inner tubes. Replace any
defective parts, if necessary.
REAR SUSPENSION
Inspect the rear shock absorber for oil leakage and
mounting rubbers including engine mounting for wear
and damage. Replace any defective parts, if neces-
sary.(Refer to page 7-32)
Inspect Interval
Inspect Initial 1,000 km and Every 6,000 km.
Inspect Interval
Inspect Every 6,000 km.
Inspect Interval
Inspect Every 6,000 km.
PERIODIC MAINTENANCE 2-18
◉
FRONT BRAKE LAMP SWITCH
The front brake lamp switch is located beneath the front
brake lever. Loosen the switch fitting screws and adjust the
timing by moving the switch body forward or backward.
(Refer to page 6-1)
◉
REAR BRAKE LAMP SWITCH
Adjust the rear brake lamp switch
①
so that the brake
lamp will come on just before pressure is felt when the
brake pedal is depressed.
①
Summary of Contents for GT 650
Page 5: ...NOTE Difference between photographs and actual motorcycles depends on the markets ...
Page 13: ...1 7 GENERAL INFORMATION EXTERIOR ILLUSTRATION ...
Page 102: ...CARBURETOR 4 3 FUEL SYSTEM ...
Page 138: ...LAMP HEADLAMP TURN SIGNAL LAMP TAIL BRAKE LAMP ELECTRICAL SYSTEM 6 16 ...
Page 158: ...7 15 CHASSIS FRONT FORK ...