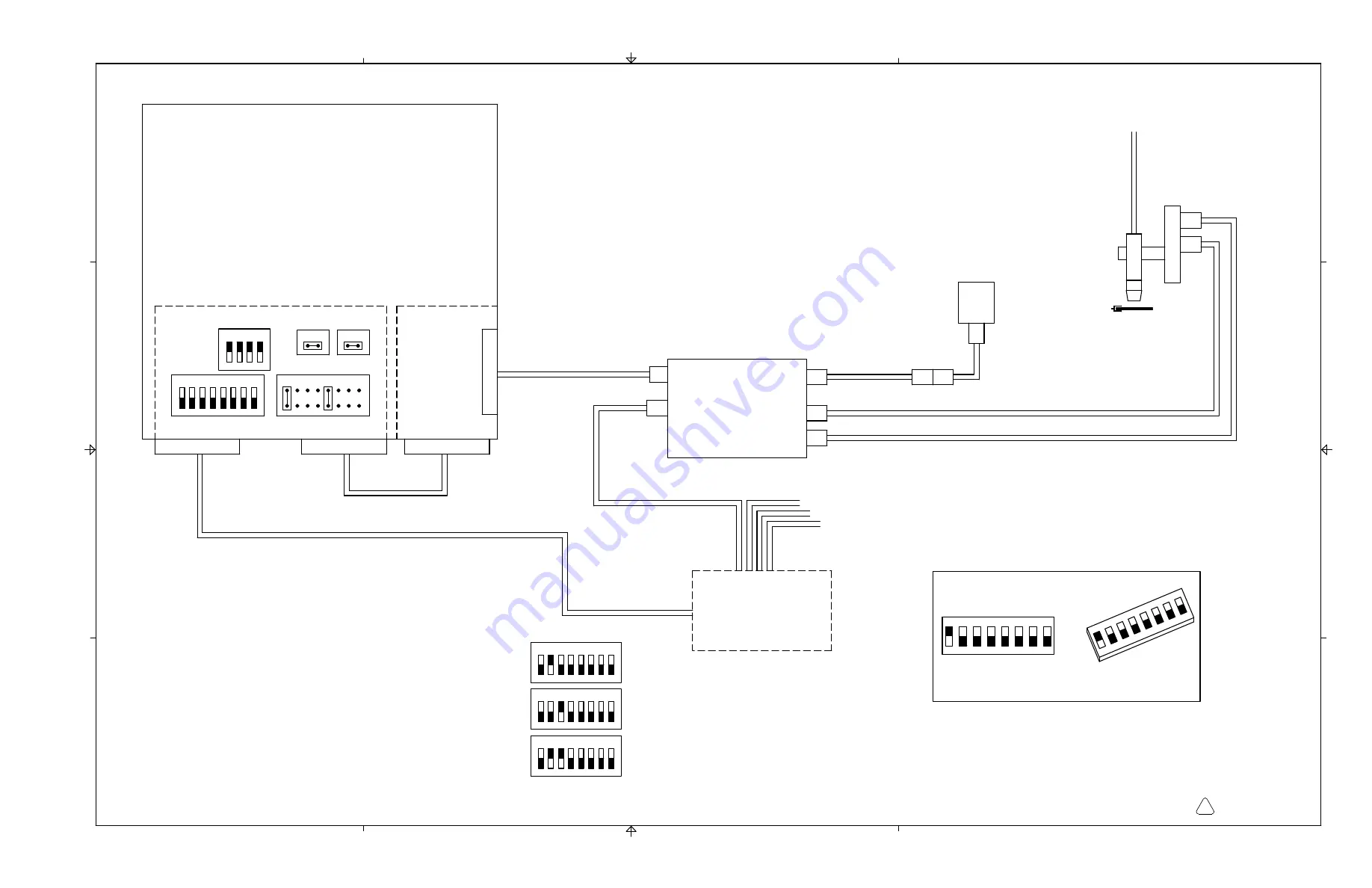
7-25
Interface
CNC
(Customer Supplied)
041993
CONTROL BOARD
S100
J303
J300B
J300A
CNC Interface Cable
CNC Interface Cable
(Optional Unit)
THC
Command
CNC Interface Cable
Pendant Ext. Cable
(Optional Unit)
Operator
Pendant
Lifter
Torch
(Optional Unit)
Motor Drive Cable
Lifter I/O Interface Cable
J2B
J2A
041842
PLASMAINTERFACE
BOARD
Serial ID
Dipswitch
Jumper Block
Machine Motion
CNC Interface Cable
Command I/O Cable-Second THC
Command I/O Cable-Third THC
Command I/O Cable-Fourth THC
1 2
J106
1 2
J107
Optional Command THC Interface
See Command
THC Manual for
internal Power
Supply wiring
Torch
1 2 3 4 5 6 7 8
ON
1 2 3 4
S101
ON
4
3
2
1
2 3 4
1
HPR PAC
Dry Cutting System
4
3
2
1
A
4
3
2
A
B
C
D
B
C
D
Workpiece
Notes:
1) For a single system installation set Serial ID (S100),
Machine Motion (J303), J106 & J107 as shown above.
2) For a two system installation duplicate a second power supply and Command THC
as illustrated for a single system, set Serial ID as shown for the second system.
3) For a three system installation set up as described above, set Serial ID as shown
for the third system.
4) For a four system installation set up as described above, set Serial ID as shown
for the fourth system.
5) All machine interface cables (Pwr. supply-CNC) used for serial communication between
Pwr. supply-CNC will have a common connection node with the CNC.
6) The CNC will need a dedicated I/O port for each Command THC.
7) If a Hypertherm Automation controller is being used, and there are intermittent communication
failures (PS Link Failure), try removing the jumpers on J106 and J107 on the control board,
and the termination jumper (J6 or J8) on the serial isolation board in the controler.
Only remove the termination jumper on the serial isolation board that is connected
to the HPR power supply. See figure on Sheet 19 for details.
Dipswitch
Serial ID
S100
for second system
S100
Dipswitch
Serial ID
for third system
S100
Dipswitch
Serial ID
for fourth system
Switches 2-8 are in the Off position
Switch 1 is in the On position
Dipswitch setting example:
S100
1
ON
4
2 3
7
5 6
8
1 2 3 4 5 6 7 8
ON
1 2 3 4 5 6 7 8
ON
1 2 3 4 5 6 7 8
ON
1 2 3 4 5 6 7 8
ON
ELEC SCH:HPR130XD POWER SUPPLY W/AUTO
D
013376
SHEET 21 OF 22
1
Summary of Contents for HyPerformance HPR130XD
Page 1: ...HyPerformance Plasma HPR130XD Auto gas Instruction manual 806330 Revision 3 ...
Page 16: ...Table of Contents viii HPR130XD Auto Gas 806330 ...
Page 26: ...Specifications 2 2 HPR130XD Auto Gas 806330 ...
Page 38: ...Specifications 2 14 HPR130XD Auto Gas 806330 ...
Page 48: ...Installation 3 10 HPR130XD Auto Gas 806330 ...
Page 59: ...Installation HPR130XD Auto Gas 806330 3 21 1X1 J103 J300 Female Male 5 6 5 6 3X1 3X2 3X3 3X4 ...
Page 94: ...Installation 3 56 HPR130XD Auto Gas 806330 ...
Page 101: ...Operation HPR130XD Auto Gas 806330 Revision 2 4 7 Diagnostics screen ...
Page 102: ...Operation 4 8 HPR130XD Auto Gas 806330 Revision 2 Test screen ...
Page 103: ...Operation HPR130XD Auto Gas 806330 Revision 2 4 9 Cut chart screen ...
Page 152: ...Operation 4 58 HPR130XD Auto Gas 806330 Revision 2 ...
Page 236: ...7 4 HPR130XD Auto Gas 806330 Discrete output functionality ...
Page 294: ...Appendix B CNC Interface Protocol b 28 HPR130XD Auto Gas 806330 Revision 1 ...
Page 302: ...4 HPR130XD Auto Gas 806330 ...