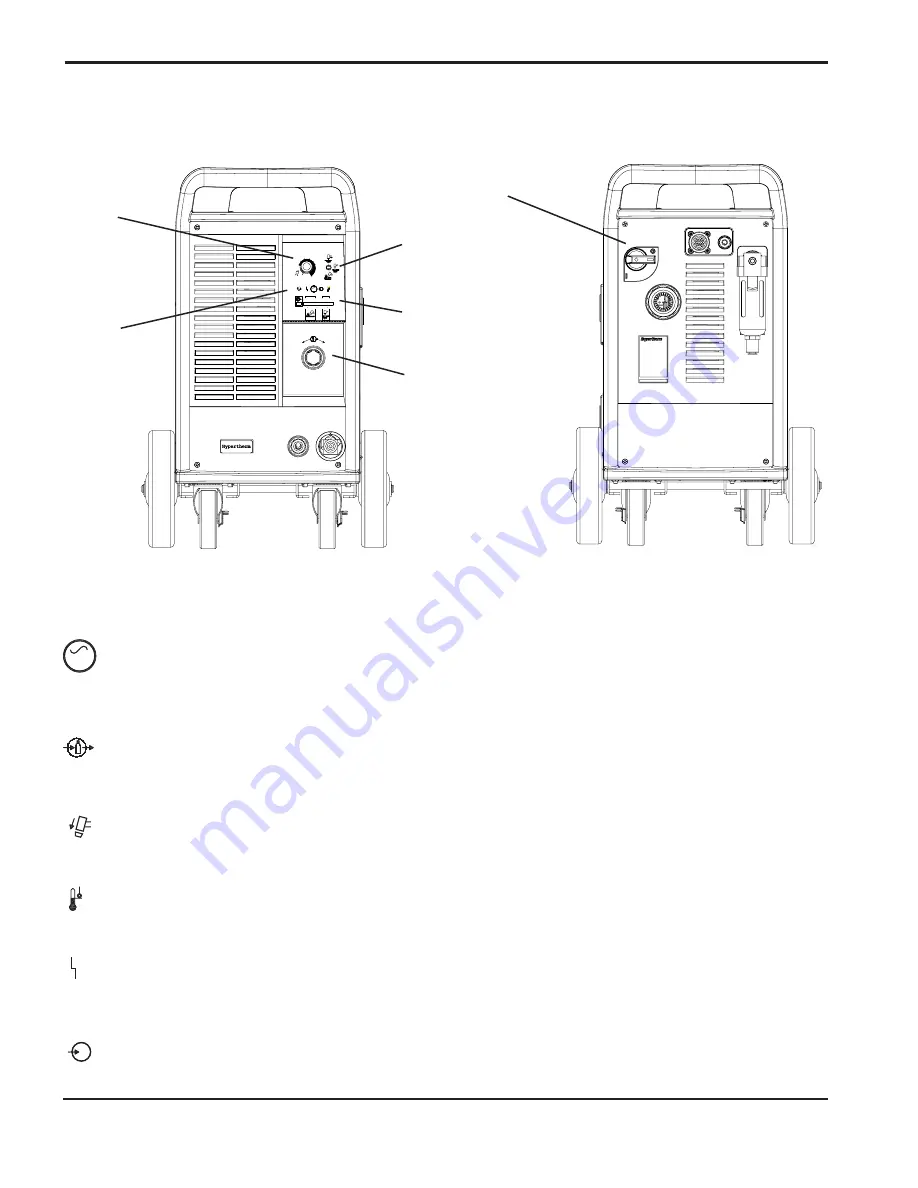
MAINTENANCE
3-2
powermax1650
Service Manual
0
Controls and Indicators
_
+
4.0
5.0
50
60
AC
70
80
V
BAR
6.0
PSI
AMPS
30
40
100
80
60
Current
(Amps)
Adjustment /
Gas Test
Knob
Mode Switch
Indicator
LEDs
Pressure
Gauge
Pressure
Regulator
ON (I) / OFF (0)
Switch
Green Power ON LED
When illuminated, indicates that power is applied to system and power switch is ON ( I ).
Gas Pressure LED
Yellow:
When flashing, indicates that the gas pressure is below 65 psig (4.5 bar) for cutting, or 40 psig
(2.8 bar) for gouging.
Green:
When illuminated, indicates acceptable gas pressure for torch operation.
Yellow Torch Cap LED
When illuminated, indicates that the Retaining Cap is loose or not installed.
NOTE: Condition must be corrected and power turned OFF then ON to clear LED.
Yellow Temp LED
When illuminated, indicates that the power supply temperature has exceeded its operating limit.
Red Fault LED
When illuminated, indicates that a fault condition exists, which prevents system operation. A yellow LED
should also be illuminated that identifies the type of fault.
Yellow Line Voltage LED
When illuminated, indicates that line voltage is below 170 VAC, above 680 VAC, or missing a phase.
AC
V
Indicator LEDs