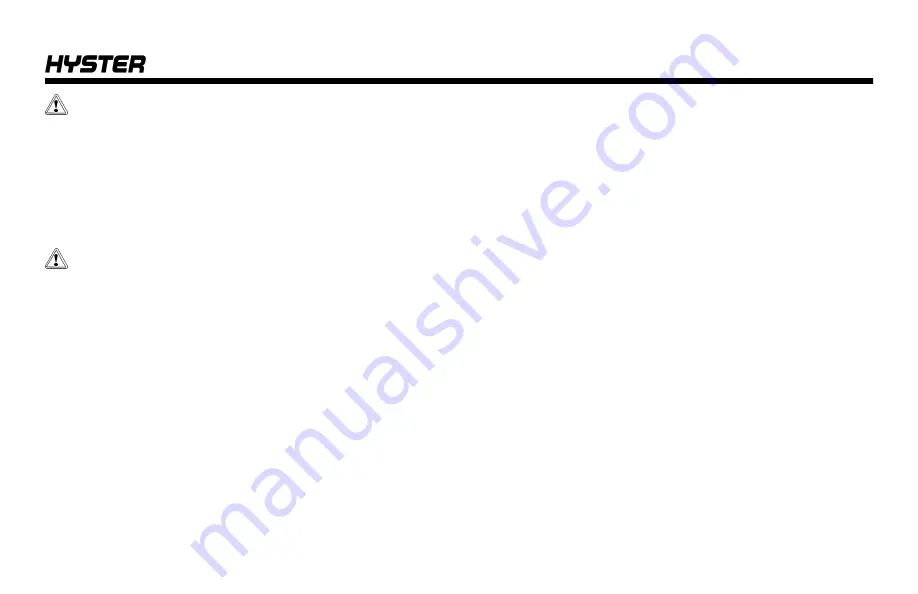
CAUTION
Never connect the battery charger plug to the plug of
the lift truck. You can damage the traction control cir-
cuit. Make sure the charger voltage is the correct volt-
age for the battery.
Use only battery chargers approved by the battery
manufacturer or dealer.
CAUTION
Always make sure the color in the window of the
charger connector is the same as the color in the win-
dow of the battery connector.
NOTE:
This series of trucks can have one of two types of
batteries. One type has removable cell caps. A green key
for battery voltage shows in the window of the battery con-
nector for batteries with call caps. The other type has
sealed cells and the electrolyte cannot be checked. A gray
key for battery voltage shows in the window of the battery
connector for sealed batteries. These sealed batteries also
require a different charger.
NOTE:
Many installations have battery chargers that can
follow a program to automatically charge a battery accord-
ing to recommendations of the battery manufacturer. Use
the recommendations of the battery manufacturer for
charging the battery.
Correct use of the hydrometer and proper operation of the
battery charger is important. See
. Follow the
instructions of the charger manufacturer. Never let the bat-
tery discharge below the minimum value given by the bat-
tery manufacturer. A fully charged battery will have a
specific gravity of 1.265 to 1.310 at 25 °C (77 °F). See
. Never charge a battery at a rate that will raise the
electrolyte temperature above 49 °C (120 °F). Never let a
battery stay discharged for long periods.
Normal Charge:
This charge is normally given to a battery
that is discharged from normal operation. Many customers
charge the battery at regular intervals that depend on use.
This procedure will keep the battery correctly charged if the
battery is not discharged below the limit. Always use a
hydrometer to check the battery if the battery is charged at
regular intervals and has cell caps. Frequent charging of a
battery that has a 2/3 or more charge can decrease the life
of the battery.
NOTE:
Some batteries are maintenance-free and do not
require checking the electrolyte. DO NOT attempt to check
electrolyte in batteries with sealed cells.
Maintenance
191
Property of American Airlines