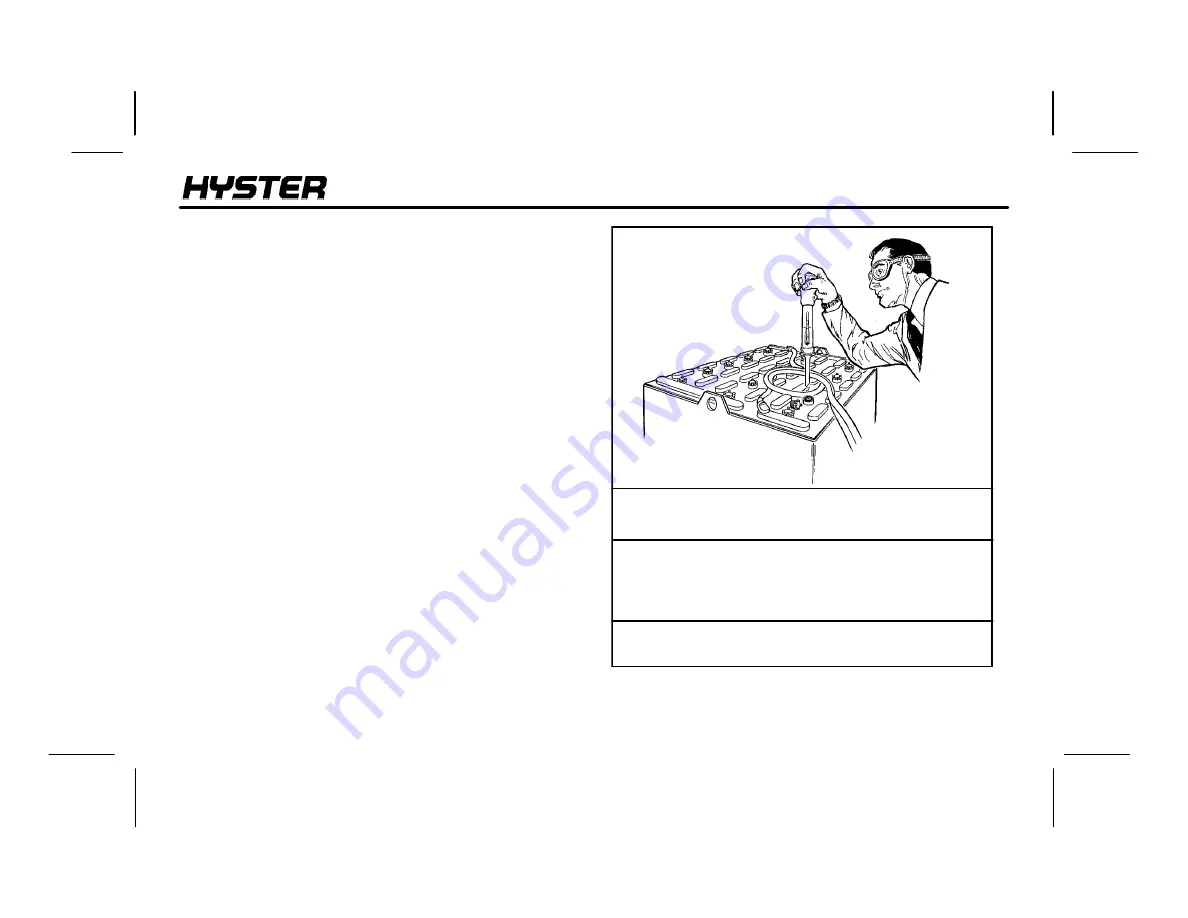
MAINTENANCE
NARROW AISLE
59
Correct use of the hydrometer and proper operation of the
battery charger is important. Follow the instructions of the
charger manufacturer. Never let the battery discharge
below the minimum value given by the battery
manufacturer. A fully charged battery will have a specific
gravity of 1.265 to 1.310 at 25
°
C (77
°
F). Never charge a
battery at a rate that will raise the electrolyte temperature
above 49
°
C (120
°
F). Do not let a battery stay discharged
for a long period of time.
1. Normal Charge:
This charge is normally given to a
battery that is discharged from normal operation. Many
customers charge the battery at regular intervals that
depend on use. This procedure will keep the battery
correctly charged if the battery is not discharged below the
limit. Always use a hydrometer to check the battery if the
battery is charged at regular intervals. Frequent charging of
a battery that has a two-thirds (2/3) or more charge can
decrease the life of the battery.
2. Equalizing Charge:
Is a low rate charge and
balances the charge in all the cells. The equalizing charge
is given approximately once a month. It is a charge at a slow
rate for three to six hours in addition to the regular charging
cycle. Do not give an equalizing charge more than once a
week.
+0.001 or --0.001 for each 2
°
C
from the 25
°
C base value.
FIGURE 13. CHECK SPECIFIC GRAVITY
SPECIFIC
GRAVITY
1.210
1.210
1.210
1.210
ELECTROLYTE
TEMPERATURE
31
°
C (87
°
F)
27
°
C (80
°
F)
25
°
C (77
°
F)
18
°
C (64
°
F)
CORRECTION
POINTS
+0.003
+0.001
0.000
--0.004
CORRECT
VALUE
1.213
1.211
1.210
1.206
Property of American Airlines