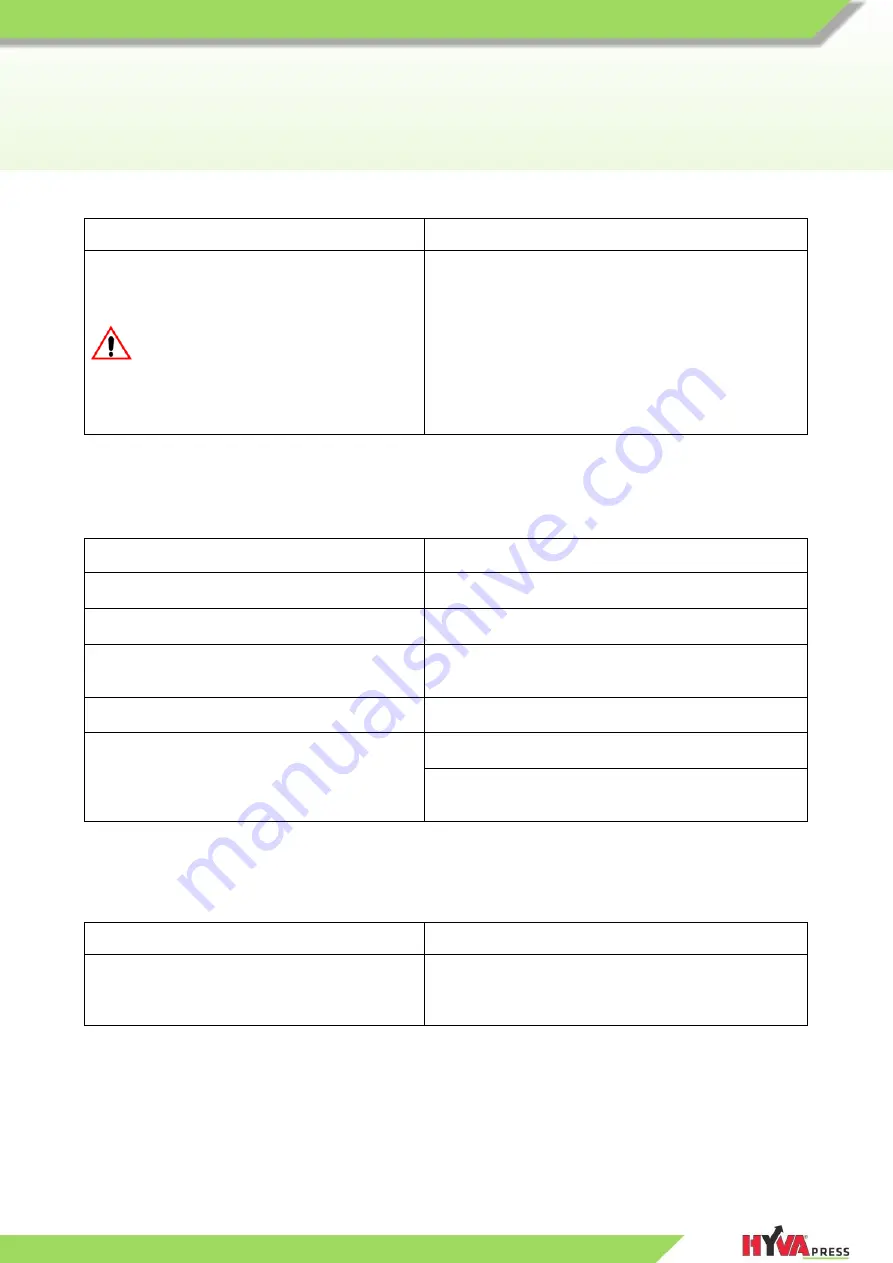
New R-Line Refuse Collection Micro
User Manual RCM10
46
4.9.1 Safety devices: operating checks and signaling tools
Operating checks
Purpose
With the machine functioning:
• Press one of
the
emergency
stop buttons.
ATTENTION
Carry out the same check with the
other emergency stop buttons on the
machine.
Check the movements and functions in progress stop
immediately.
Table 5-1
4.9.2 Electrical system: operating checks and their functions
Operating checks
Function
Check the closure of the electric boxes.
Prevent dangerous situations for any exposed persons,
and allow the work cycle to be performed normally.
Press the electrical power supply button inside
the cab.
Connect the machine and its associated units to the
power supply.
Visually inspect the electrical cables every 250
hours.
If any twisting, stretching, or breakage of the outer
sheathing is encountered, the cable must be replaced
with one that has the same technical characteristics.
Verify the proper tightening of the equipotential
connections every 1000 hours.
If any loose connections are encountered the proper
tightening torque must be restored.
Visually inspect the inside of the electrical boxes
every 250 hours.
Dry them thoroughly if any moisture is encountered.
Replace any parts that show signs of corrosion and
lubricate all the connections with oil for electrical
contacts.
Table 5-2
4.9.3 Hydraulic and pneumatic systems: operating checks and their functions
Operating checks
Function
Regularly check the good condition of the piping,
replacing it if any deterioration is found on the
outer sheath.
The aim of these preventive maintenance operations is
to guarantee the constant efficiency of the hydraulic
and pneumatic circuits, under conditions of maximum
safety.
Table 5-3