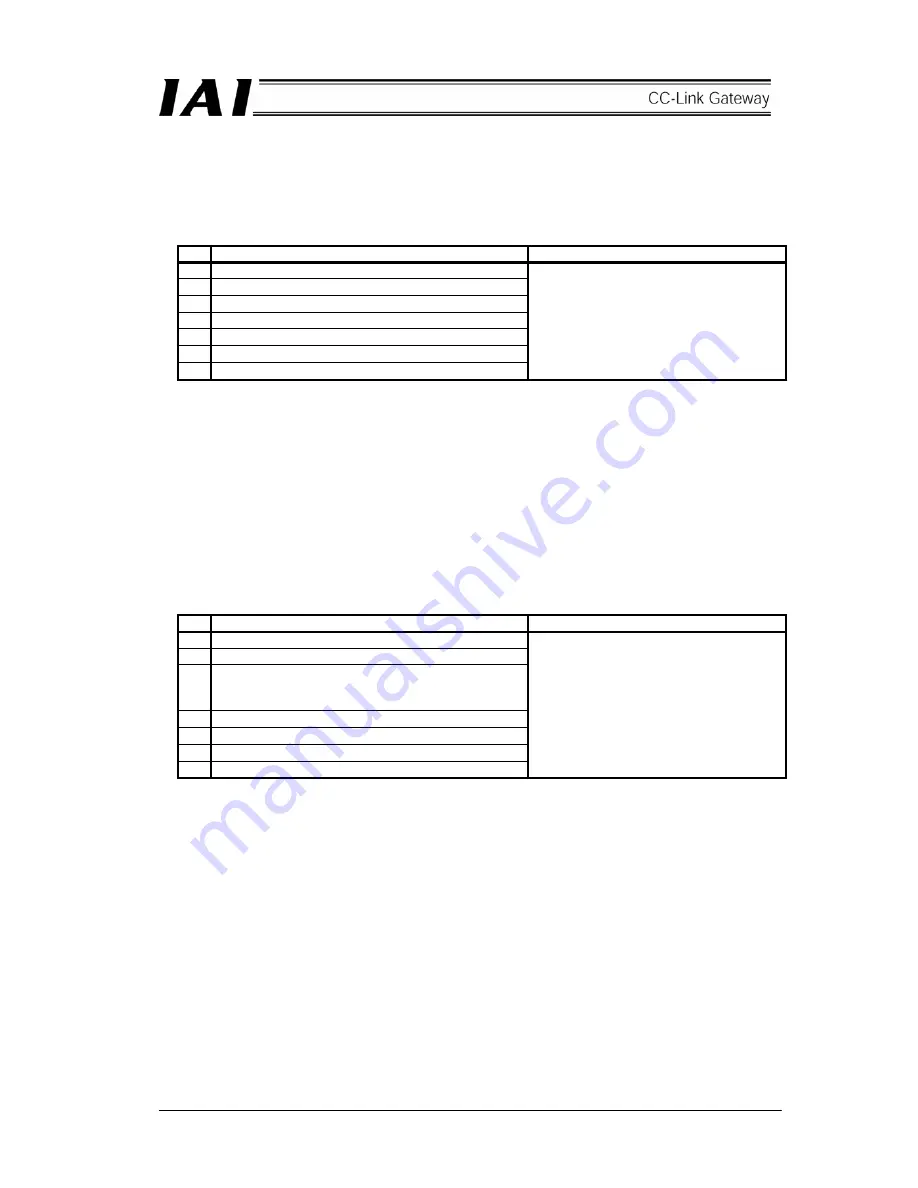
72
[5] Group designated broadcast POS movement start
This command simultaneously starts an axis designated by group No. to a position designated by POS
No. This command performs communication between gateway and controller by broadcast, therefore,
response from the controller does not return.
The response result displayed on the PCL input means that communication to the controller normally
ended, and does not indicate status of the controller. Determine the status from the status signal to each
axis.
*1
PLC output (request)
PLC input (response)
+2 0D03
H
3
POS No. *2
4
Group ID No. *3
5 0
6 0
7 0
8 0
Same value as request at normal
*1) Relative RY and relative RX from the head
*2) Possible values depend on type of robo-cylinder and its setting.
*3) If this is 0, all of the linked axes move regardless of group designation.
Setting of group No. is performed by system parameter setting of personal computer supporting
software.
*4) When movement command is issued by control word for every axis in process of movement by this
command, movement by this command is cancelled and operation is performed by the latest
movement command. Note that each axis has two movement command interfaces.
Use these two interfaces exclusively.
*5) Even if a link to CFG of gateway control signal is eliminated by bit OFF operation, the controller
always receives this command and executes after the link is once established.
[6] PIO/Modbus switching command
*1
PLC output (request)
PLC input (response)
+2 0DA1
H
3 0
4 Coil
ON/OFF
00FF
H
=ON: Modbus (PIO command ineffective)
0000
H
=OFF: PIO (PIO command effective) *2
5 0
6
Axis No. 0 to F
H
7 0
8 0
Same value as request at normal
*1) Relative RY and relative RX from the head
*2) PIO/Modbus switching status is reflected on the status signal PMSS. And, this is not allowed to be
set for the position No. designated movement axis (Invalid request command error (0103H) occurs).
*3) When coil OFF (PIO command effective) is designated, it is also possible to change position data of
axis from the PLC by Modbus communication (The link should be held).
*4) When control right for the controller is on the PIO, do not issue movement command from the
Modbus.
Summary of Contents for RCM-GW-CC
Page 1: ...IAI America Inc CC Link RCM GW CC Gateway Unit Operation ManualFirst Edition...
Page 4: ......
Page 10: ...6 1 5 How to identify model RCM GW CC Basic model For CC Link Gateway unit...
Page 12: ...8 2 2 External dimension drawing Mounting dimension...
Page 78: ...74...
Page 82: ...78 Position data measurement value Present position 1 2 3 4 4 5 6 7...
Page 84: ...80 Speed acceleration and deceleration set value Actuator speed Speed n2 Speed n3 1 2 3...
Page 88: ...84 Command position No Completion position No 1 2 3 4 5 6...
Page 91: ...87...
Page 93: ...89...
Page 125: ...121 No 3 Axis 1 pause No 3 Axis 1 pause lamp No 3 Axis 1 STP...
Page 130: ...126...
Page 131: ......