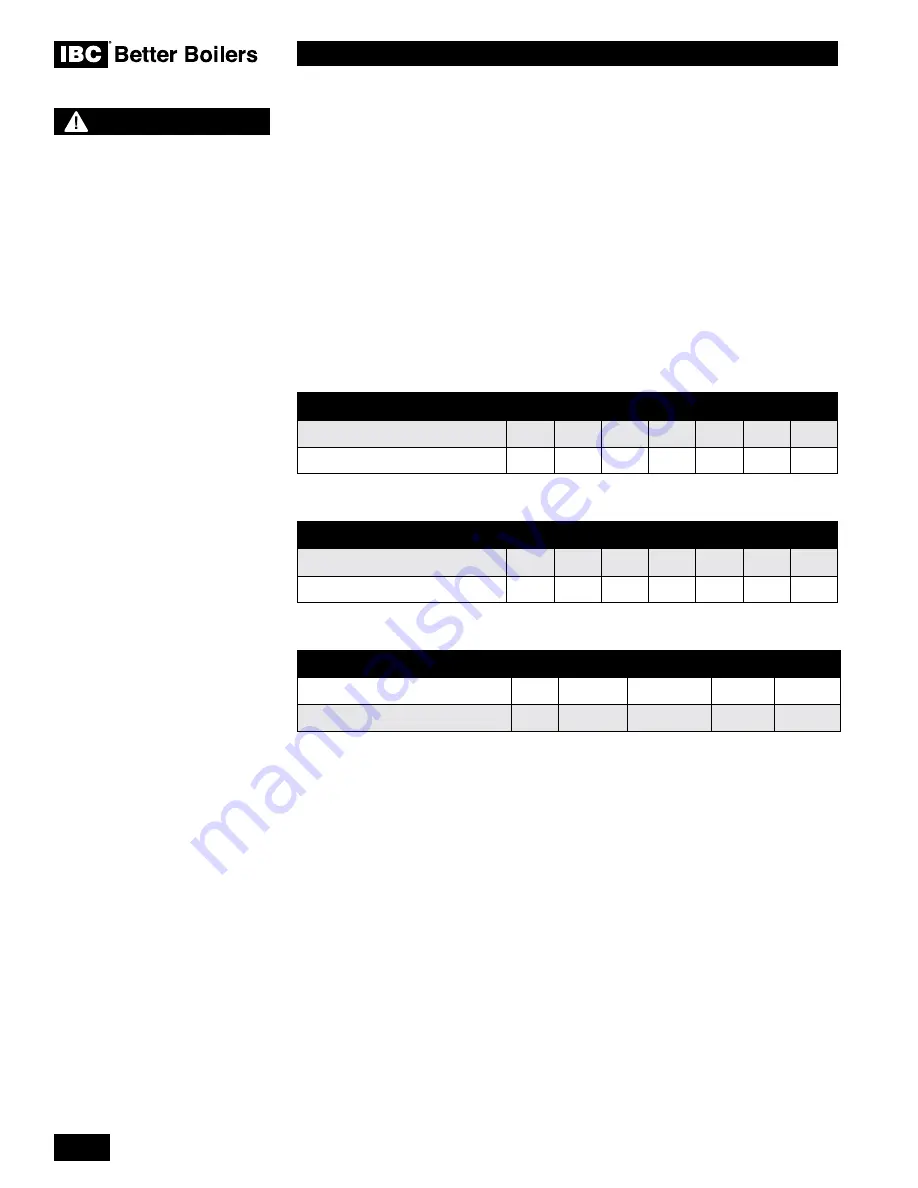
INSTALLATION AND OPERATION INSTRUCTIONS
1-24
SL 10-85 G3, SL 14-115 G3, SL 20-160 G3, SL 30-199 G3 MODULATING GAS BOILERS
The SL series modulating boilers are designed to supply three different heating loads with
temperatures within the range 34°F to 180°F - to meet three separately piped loads. Use
closely spaced tees to connect each pumped “load” (e.g. DHW, baseboards or radiant
floor) to the primary loop, or employ the use of a hydraulic separator to isolate the boiler
loop from the system and pipe the system from the secondary side of the separator. Two-
load systems may be piped with a variant of parallel piping commonly used, including our
unique dual side piping configuration.
Ensure that the pump is rated for the design circulating water temperatures; some pumps
have a minimum water temperature rating above the low temperature potential of the
boiler. Following installation, confirm the actual performance by measuring Δ°T (under high
and low flow conditions)
.
A variety of application drawings showing basic design options are available from the IBC
web site at: www.ibcboiler.com
BOILER HEAD LOSS
BOILER HEAD LOSS SL 10-85 G3, SL 14-115 G3
Flow rate (gpm)
2
4
6
8
10
12
14
Head loss @ flow (ft wc)
0.5’
1.5’
2.5’
3.0’
4.0’
4.5’
6.0’
Table 5A: Boiler Head Loss -
SL 10-85 G3
/
SL 14-115 G3
BOILER HEAD LOSS SL 20-160 G3
Flow rate (gpm)
4
6
8
10
12
14
16
Head loss @ flow (ft wc)
0.5’
1.0’
1.5’
2.0’
3.0’
4.0’
5.0’
Table 5B: Boiler Head Loss - SL 20-160 G3
BOILER HEAD LOSS SL 30-199 G3
Flow rate (gpm)
6
10
15
20
22
Head loss @ flow (ft wc)
2’
3.5’
5.5’
8’
13’
Table 5C: Boiler Head Loss - SL 30-199 G3
We recommend water flow after burner shutdown to utilize legacy heat – this is due to
the mass of the heat exchanger plus its water volume. Default software values will run
the boiler’s primary pump for up to 15 minutes (900 seconds) after burner shutdown.
Secondary pumps can be set to run up to 5 minutes after burner shutdown (for the last
calling load). As shipped, the default software will run the Boiler pump for 5 minutes to
place the legacy heat where it is useful.
The primary pump must be under the control of the boiler to allow pump purge after burner
shut-down.
Schematics for several piping layouts are provided herein, and additional drawings are
available at www.ibcboiler.com. Installers shall conform the piping design to one of the
provided configurations to simplify the control application, promote good loads and flow
management.
WARNING
Water quality has a significant
impact on the lifetime and
performance of an IBC Boiler
heat exchanger.
Improperly prepared water in
a heating circuit may cause
damage to the heat exchanger
through corrosion or fouling.
Repeated or uncontrolled water
fills will increase the potential
for damage.
High levels of dissolved solids
or minerals may precipitate
out of the fluid onto the hottest
part of the heat exchanger,
impairing heat transfer and
resulting in overheating and
premature failure. The amount
of solids that may form on the
heat exchanger will depend
on the degree of hardness and
the total water volume in the
system. A high water volume
system with a low hardness
count may cause as much
damage as a system with less
volume and higher hardness, so
it is recommended to treat water
so as to remove all dissolved
solids. Other water chemistry
allowable limits are as follows:
Acidity pH is to be between 6.6
and 8.5
Chloride is to be less than 125
mg/l
Iron is to be less than 0.5 mg/l
Cu less than 0.1 mg/l
Conductivity is to be less than
400μS/cm (at 25°C)
Hardness is to be 7 Grains or
less
IMPORTANT: Ensure that these
limits are acceptable for the
other water-side components in
the system.
Summary of Contents for SL 20-160 G3
Page 75: ...6 3 DIAGRAMS SL 10 85 G3 SL 14 115 G3 SL 20 160 G3 SL 30 199 G3 MODULATING GAS BOILERS...
Page 77: ...6 5 DIAGRAMS SL 10 85 G3 SL 14 115 G3 SL 20 160 G3 SL 30 199 G3 MODULATING GAS BOILERS...
Page 79: ...6 7 DIAGRAMS SL 10 85 G3 SL 14 115 G3 SL 20 160 G3 SL 30 199 G3 MODULATING GAS BOILERS...
Page 85: ...SERVICE RECORD DATE LICENSED CONTRACTOR DESCRIPTION OF WORK DONE...
Page 86: ...NOTES...
Page 87: ...NOTES...