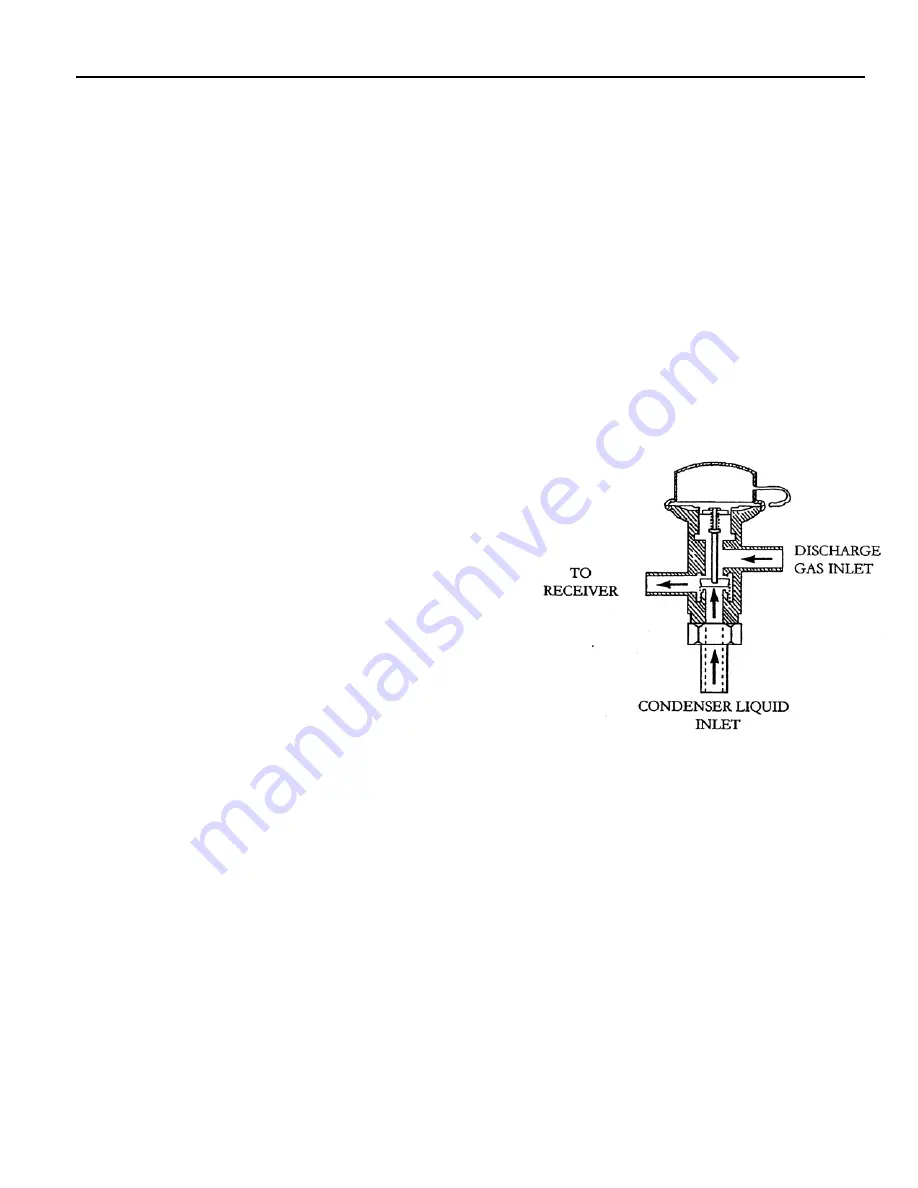
ICE Series
Refrigeration System
Page E6
Remote Condenser (Continued)
If the airflow is restricted or the condenser is dirty, the head pressure will be excessively high, slow
production will result and the compressor may overheat and eventually become damaged. The
condenser coil and fan blades must be kept clean. The condenser can be cleaned with
compressed air or by using a brush. If a brush is used, brush in the direction of the fins taking care
not to bend the fins. If the condenser fins are bent, this will restrict the airflow through the
condenser and the fins will need to be straightened with a fin comb. Problems related to a dirty
condenser or poor airflow will not be covered under warranty. Note: The condenser fan motor runs
continually, it will shut off when the icemaker shuts off.
Mixing Valve
When the temperature at the condenser is above 70°F (21°C), the refrigerant flow from the
compressor is directed by the mixing valve through the condenser and into the receiver. When the
temperature at the condenser drops below 70°F (21°C), the pressure in the bellows of the mixing
valve becomes greater than the pressure of the liquid refrigerant coming from the condenser. This
change allows the valve to partially restrict the flow of
refrigerant leaving the condenser and allows discharge
gas to by-pass the condenser and flow directly into the
receiver, mixing with the liquid refrigerant from the
condenser. The amount of discharge gas that
bypasses the condenser increases as the ambient
temperature decreases. This action of the mixing
valve allows the discharge pressure to be maintained
at approximately 240 psi (16.5 bar) during low ambient
conditions. If the refrigerant system is undercharged
and the ambient temperature is below 70°F (21°C), the
mixing valve will not work properly. The mixing valve
will allow too much refrigerant to bypass the
condenser.
Problem
Possible Cause
Remedy
1 Head pressure low, Line between
A. Valve Defective, not allowing A. Replace valve
valve and receiver cold. Ambient
discharge gas into receiver
condenser temp. below 70°F (21°C)
2 Head pressure low, Line between
A. System low on charge.
A. Leak check. Recover
valve and receiver hot.
B. Valve defective, not
refrigerant and weigh
allowing liquid
in proper charge.
into
receiver.
B.
Replace
valve
3. Head pressure low, Line
A. Valve defective not
A. Replace valve.
returning from condenser
allowing refrigerant
is cool. Ambient condenser
to circulate through
temperature is above 70°F (21°C)
condenser.
Summary of Contents for 16
Page 19: ...ICE Series General Information Page A17 Electrical and Plumbing Requirements ICE1506 Remote ...
Page 86: ...ICE Series Wiring Diagram Page G1 ICEU150 200 205 206 Air and Water Wiring Diagram ...
Page 87: ...ICE Series Wiring Diagram Page G2 ICEU150 200 205 206 Air and Water Wiring Schematic ...
Page 88: ...ICE Series Wiring Diagram Page G3 ICEU150 220 225 226 Air and Water Wiring Diagram ...
Page 89: ...ICE Series Wiring Diagram Page G4 ICEU150 220 225 226 Air and Water Wiring Schematic ...
Page 90: ...ICE Series Wiring Diagram Page G5 ICE0250 Air and Water Wiring Diagram ...
Page 91: ...ICE Series Wiring Diagram Page G6 ICE0250 Air and Water Wiring Schematic ...
Page 92: ...ICE Series Wiring Diagram Page G7 ICE0400 Air and Water Wiring Diagram ...
Page 93: ...ICE Series Wiring Diagram Page G8 ICE0400 Air and Water Wiring Schematic ...
Page 94: ...ICE Series Wiring Diagram Page G9 ICE0405 0406 Air and Water Wiring Diagram ...
Page 95: ...ICE Series Wiring Diagram Page G10 ICE0405 0406 Air and Water Wiring Schematic ...
Page 96: ...ICE Series Wiring Diagram Page G11 ICE0500 Air and Water Wiring Diagram ...
Page 97: ...ICE Series Wiring Diagram Page G12 ICE0500 Air and Water Wiring Schematic ...
Page 98: ...ICE Series Wiring Diagram Page G13 ICE0500 Remote Wiring Diagram ...
Page 99: ...ICE Series Wiring Diagram Page G14 ICE0500 Remote Wiring Schematic ...
Page 102: ...ICE Series Wiring Diagram Page G17 ICE0605 0606 0805 0806 1005 1006 Remote Wiring Diagram ...
Page 103: ...ICE Series Wiring Diagram Page G18 ICE0605 0606 0805 0806 1005 1006 Remote Wiring Schematic ...
Page 104: ...ICE Series Wiring Diagram Page G19 ICE1007 Air and Water Wiring Diagram ...
Page 105: ...ICE Series Wiring Diagram Page G20 ICE1007 Air and Water Wiring Schematic ...
Page 106: ...ICE Series Wiring Diagram Page G21 ICE1007 Remote Wiring Diagram ...
Page 107: ...ICE Series Wiring Diagram Page G22 ICE1007 Remote Wiring Schematic ...
Page 108: ...ICE Series Wiring Diagram Page G23 ICE1405 1406 1806 2005 2106 Air and Water Wiring Diagram ...
Page 109: ...ICE Series Wiring Diagram Page G24 ICE1405 1406 1806 2005 2106 Air and Water Wiring Schematic ...
Page 110: ...ICE Series Wiring Diagram Page G25 ICE1405 1406 1806 2005 2106 Remote Wiring Diagram ...
Page 111: ...ICE Series Wiring Diagram Page G26 ICE1405 1406 1806 2005 2106 Remote Wiring Schematic ...
Page 112: ...ICE Series Wiring Diagram Page G27 ICE1407 1807 2107 Air and Water Wiring Diagram ...
Page 113: ...ICE Series Wiring Diagram Page G28 ICE1407 1807 2107 Air and Water Wiring Schematic ...
Page 114: ...ICE Series Wiring Diagram Page G29 ICE1407 1807 2107 Remote Wiring Diagram ...
Page 115: ...ICE Series Wiring Diagram Page G30 ICE1407 1807 2107 Remote Wiring Schematic ...
Page 116: ...ICE Series Wiring Diagram Page G31 ICE1606 Remote Wiring Diagram ...
Page 117: ...ICE Series Wiring Diagram Page G32 ICE1606 Remote Wiring Schematic ...
Page 118: ...ICE Series Wiring Diagram Page G33 ICE0320 Air and Water Wiring Diagram ...
Page 119: ...ICE Series Wiring Diagram Page G34 ICE0320 Air and Water Wiring Schematic ...
Page 120: ...ICE Series Wiring Diagram Page G35 ICE0520 Air and Water Wiring Diagram ...
Page 121: ...ICE Series Wiring Diagram Page G36 ICE0520 Air and Water Wiring Schematic ...
Page 122: ...ICE Series Wiring Diagram Page G37 ICE0325 0525 Air and Water Wiring Diagram ...
Page 123: ...ICE Series Wiring Diagram Page G38 ICE0325 0525 Air and Water Wiring Schematic ...
Page 124: ...ICE Series Wiring Diagram Page G39 ICE0305 Air and Water Wiring Diagram ...
Page 125: ...ICE Series Wiring Diagram Page G40 ICE0305 Air and Water Wiring Schematic ...
Page 126: ...ICE Series Wiring Diagram Page G41 ICE1506 Remote ...
Page 127: ...ICE Series Wiring Diagram Page G42 ICE1506 Remote ...
Page 128: ...ICE Series Wiring Diagram Page G43 ICEU300 Air and Water ...
Page 129: ...ICE Series Wiring Diagram ICEU300 Air and Water Page G44 ...
Page 130: ...ICE Series Wiring Diagram Page G45 ICEU305 Air and Water ...
Page 131: ...ICE Series Wiring Diagram Page G46 ICEU305 Air and Water ...
Page 132: ...ICE Series Wiring Diagram Page G47 ICE0500 Remote Wiring Diagram R3 ...
Page 133: ...ICE Series Wiring Diagram Page G48 ICE0500 Remote Wiring Schematic R3 ...
Page 134: ...ICE Series Wiring Diagram ICE0605 0606 0806 1006 Remote Wiring Diagram R3 Page G49 ...
Page 135: ...ICE Series Wiring Diagram Page G50 ICE0605 0606 0806 1006 Remote Wiring Schematic R3 ...
Page 136: ...ICE Series Wiring Diagram Page G51 ICE1007 Remote Wiring Diagram R3 ...
Page 137: ...ICE Series Wiring Diagram Page G52 ICE1007 Remote Wiring Schematic R3 ...
Page 146: ...ICE Series Wiring Diagram ICE0500 Air3 and Water3 Wiring Diagram Page G61 ...
Page 147: ...ICE Series Wiring Diagram Page G62 ICE0500 Air3 and Water3 Wiring Schematic ...
Page 148: ...ICE Series Wiring Diagram Page G63 ICE0500 Remote4 Wiring Diagram ...
Page 149: ...ICE Series Wiring Diagram Page G64 ICE0500 Remote4 Wiring Schematic ...
Page 151: ...ICE Series Wiring Diagram Page G66 ICE0606 Air3 and Water3 ICE0605 Air3 and Water3 ...
Page 152: ...ICE Series Wiring Diagram ICE0606 Remote4 and ICE0605 Remote4 Wiring Diagram Page G67 ...
Page 153: ...ICE Series Wiring Diagram Page G68 ICE0606 Remote4 and ICE0605 Remote4 Wiring Schematic ...
Page 154: ...ICE Series Wiring Diagram Page G68 ICE0606 Remote4 and ICE0605 Remote4 Wiring Schematic ...
Page 155: ...ICE Series Wiring Diagram ICE1405 6A3 W3 ICE1806W3 and ICE2106W3 Wiring Diagram Page G69 ...
Page 156: ...ICE Series Wiring Diagram Page G70 ICE1405 6A3 W3 ICE1806W3 and ICE2106W3 Wiring Schematic ...
Page 157: ...ICE Series Wiring Diagram ICE1407A3 W3 ICE1807W3 and ICE2107W3 Wiring Diagram Page G71 ...
Page 158: ...ICE Series Wiring Diagram Page G72 ICE1407A3 W3 ICE1807W3 and ICE2107W3 Wiring Schematic ...
Page 159: ...ICE Series Wiring Diagram Page G73 ICE1405 6R3 ICE1806R3 and ICE2106R3 Wiring Diagram ...
Page 160: ...ICE Series Wiring Diagram Page G74 ICE1405 6R3 ICE1806R3 and ICE2106R3 Wiring Schematic ...
Page 161: ...ICE Series Wiring Diagram Page G75 ICE1407R3 ICE1807R3 and ICE2107R3 Wiring Diagram ...
Page 162: ...ICE Series Wiring Diagram Page G76 ICE1407R3 ICE1807R3 and ICE2107R3 Wiring Schematic ...
Page 163: ...ICE Series Wiring Diagram Page G77 ICE1506R3 Wiring Diagram ...
Page 164: ...ICE Series Wiring Diagram Page G78 ICE1506R3 Wiring Schematic ...