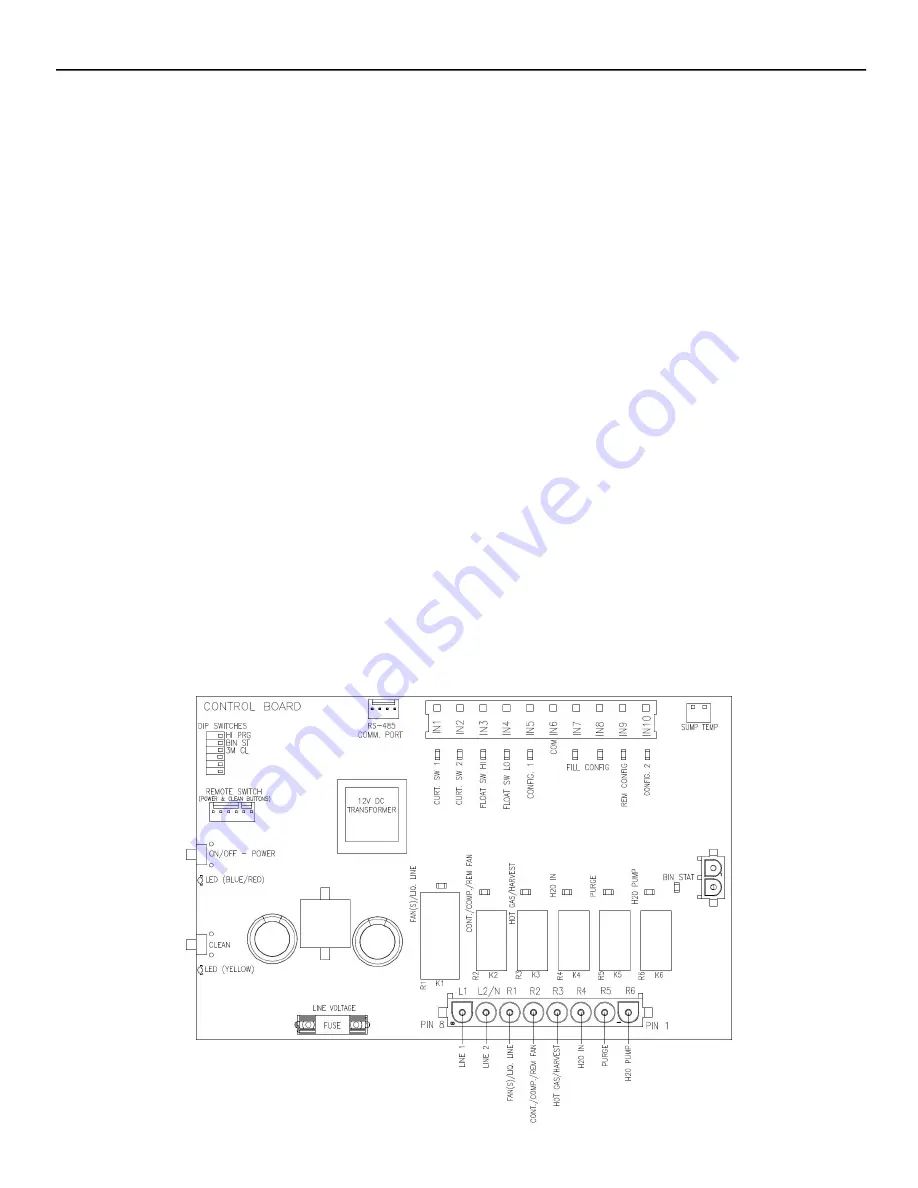
ELEVATION SERIES
HOW THE ICE MACHINE WORKS
11
Operation of the CIM Series Cuber
Freeze Cycle
A quick press and release of the ON/OFF button
will start operation of the unit. The Water Inlet
Valve is energized. Once the HI Water Float is in
the open position the Water Inlet is de-energized.
The Hot Gas Valve will open for 5 seconds. The
Compressor will be energized and 5 seconds later
the Hot Gas Valve will close, starting the Pre-chill
of the Evaporator. The Fan Motor (if applicable)
will start once the Fan Control closes. After the
Pre-chill ends, the Water Pump will be energized.
Water is now flowing across the Evaporator.
When the water temperature reaches a
predetermined factory set point (near freezing), the
unit will perform a 20 second shut down of the
Water Pump to assist in Anti-Slush of the water in
the Sump. At the conclusion of Anti-Slush, the unit
will continue in freeze mode until the Low Water
Float is satisfied (closes), indicating the formation
of a full slab of Ice on the Evaporator and will start
the harvest Cycle.
Harvest Cycle
The Fan Motor shuts down as the Hot Gas Valve,
Purge Valve and Water Inlet Valve are energized.
The Water Inlet Valve will stay energized for
additional time after the Purge Valve closes,
partially filling the Water Sump.
The unit continues in this mode until the Harvest
Assist Assembly helps push the ice slab from the
plate and the contacts in the Curtain Switch open as
the slab drops into the bin. If the Curtain Switch
remains open after the factory preset time in the
Harvest Cycle, the unit will shut down on a full
bin. If the Curtain opens and closes with the
harvest of the ice, the unit will restart the next
freeze cycle.
Proper bridge thickness, when measured at the
middle of the slab, on the CIM units is
approximately 3/16” thick for units less than 400
lbs. and 1/8” for 400 lbs. and above.
CIM Control Board