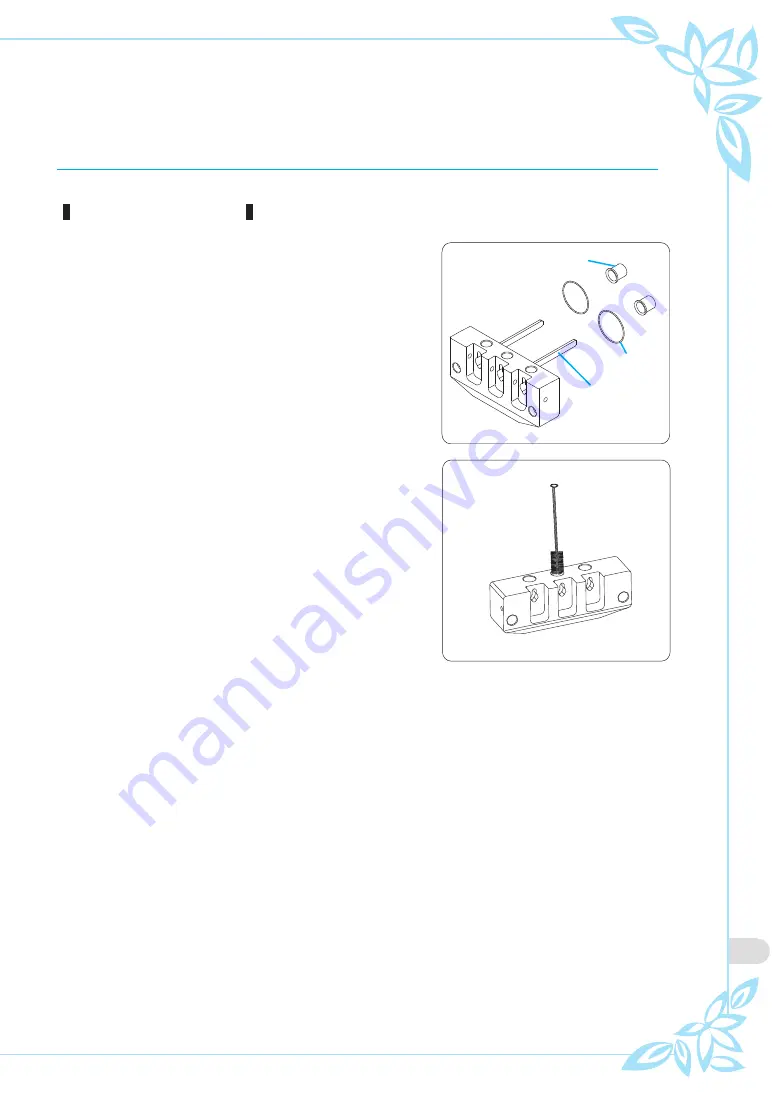
19
Cleaning method
20. Disassemble the dasher cover assembly,
wash all the parts using neutral detergent
and wipe them with soft cloth.
21. Clean the piston assembly hole of the
dasher cover with a brush and soft cloth.
패킹자바라
식용구리스
샤프트
대샤
DASHER COVER
PACKING
BEARING DASHER
MIXING SHAFT
Washing of each parts
패킹자바라
식용구리스
샤프트
대샤
DASHER COVER
PACKING
BEARING DASHER
MIXING SHAFT