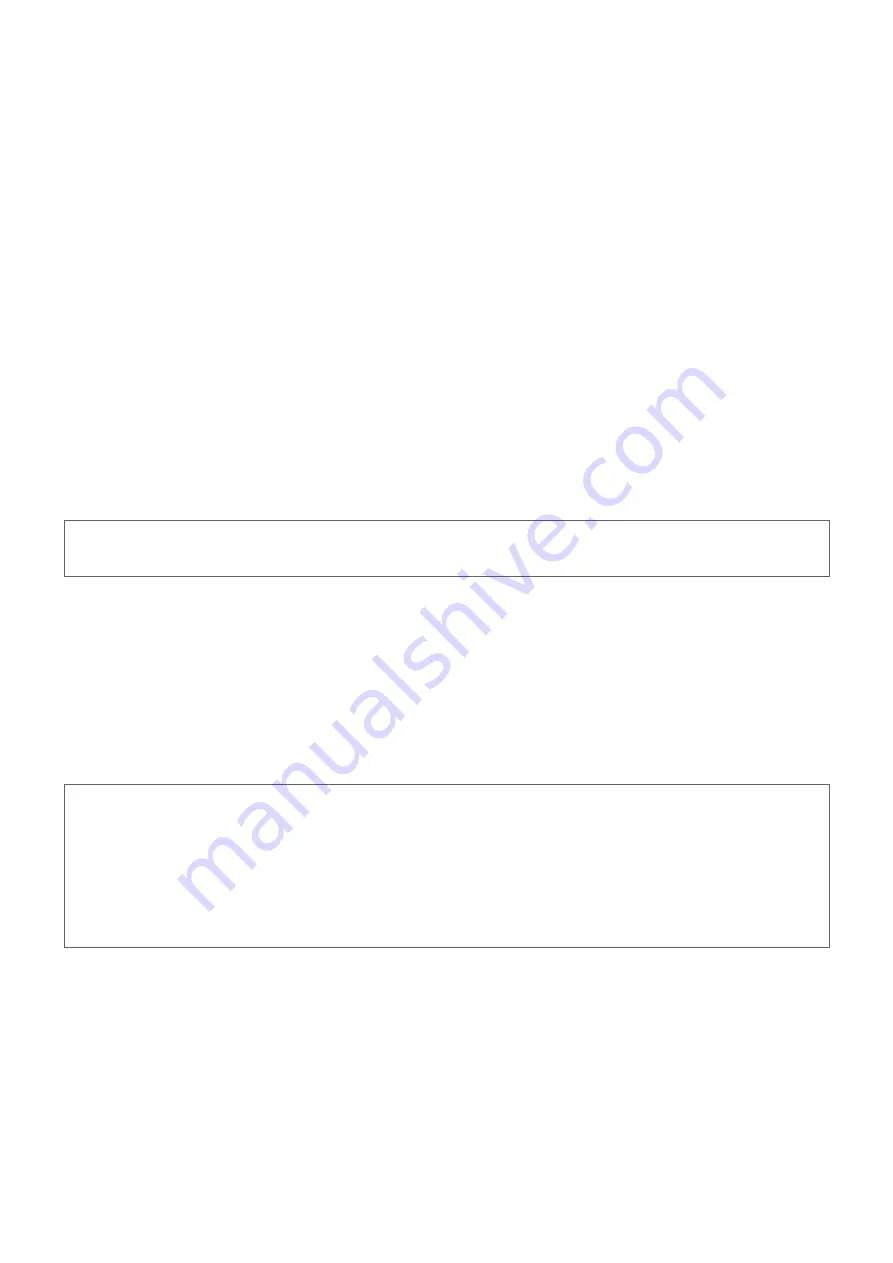
Maintenance
33
T(1)
Physical verification of the intervention of the devices (as described in the following paragraph "Checking of the minimum
level safety level switches").
T(2)
Physical verification of the intervention of the devices (as described in the following paragraph "Checking of the minimum
level safety level switches").
T(3)
Physical verification of the intervention of the devices (as described in the following paragraph "Checking of the minimum
level safety level switches").
T(4) Purge the level indicators.
T(5) Manually verify, using the selectors on the panel front, the opening of the valves.
T(6) Analysis of the water quality by taking a sample from the generator, check if it meets the specifications of EN12953-10 (see
paragraph "Water characteristics").
T(7)
Analysis of the water quality by taking a sample from the generator and check it meets the indications of the TDS automatic
control device.
T(8) Carefully check the load system, correspondence of level in the glass indicators with the parameters described in this
manual.
T(9) Verification of safety valves by applying a sample pressure gauge to the generator, as reference of the exact intervention
pressure. Verifications must be performed by qualified personnel.
T(10) Check correct seal, grease, lubricate where necessary.
T(11) Analysis of the water quality by taking a sample from the supply/treatment system, check if it meets the specifications of
EN12953-10 (see paragraph "Water characteristics").
T(12) Check the proper operation of all safety, electric and electronic circuits. Verifications must be performed by qualified
personnel.
T(13) Check the correct indications of the instrumentation with sample thermometers/pressure gauges. Verifications must be
performed by qualified personnel.
T(14) Check the burner, combustion control, safety devices. Verifications must be performed by qualified personnel.
T(15) Bench check of the safety devices. Verifications must be performed by qualified personnel.
a
ATTENTION
The electronic level relays inside the electrical panel must be replaced after 8 years of operation as they have reached
the end of their life-span.
METHODS FOR CHECKING THE SAFETY DEVICES
CHECKING OF THE MINIMUM LEVEL SAFETY LEVEL SWITCHES
Stand in front of the electrical panel, leave the steam outlet valve with removal regulator open, turn off the pump by putting the
selector to "0", wait for the natural lowering of the generator water level. To speed up the operation act on the mud discharge
valve.
m
IMPORTANT
The two safety devices must intervene when the water level reaches the "minimum" indicated on the side of the glass
indicators. Otherwise, check the entire level switch consisting of:
–
electronic level regulator; check it is intact and, if not, proceed with replacement
–
connection cable between electrical panel and probe; possible interruption and/or short circuit
–
level probe; check for possible breakage of the ceramic part and consequent loss of electrical insulation
–
level dipstick; possible scaling that prevents water-probe current pass or possible detachment of the dipstick.
If the check is positive, place the pump command to "AUT".
CHECKING OF THE MAXIMUM LEVEL SWITCH
Position the pump selector located on the electrical panel in the MAN position and wait for the water level in the generator to rise.
Check that the pump stops.
CHECK OF THE SAFETY PRESSURE SWITCH
The safety pressure switch calibration must be at least 0.5 bar below the calibration of the safety valves.
To check the correct intervention of the safety pressure switch, it is necessary to increase the calibration of the adjustment pressure
switch(es) and ensure the switch-off of the burner and activation of the block on the boiler electrical panel by visually following
the indication given by the pressure gauge.
Cooke Industries - Phone: +64 9 579 2185 Email: sales@cookeindustries.co.nz Web: www.cookeindustries.co.nz