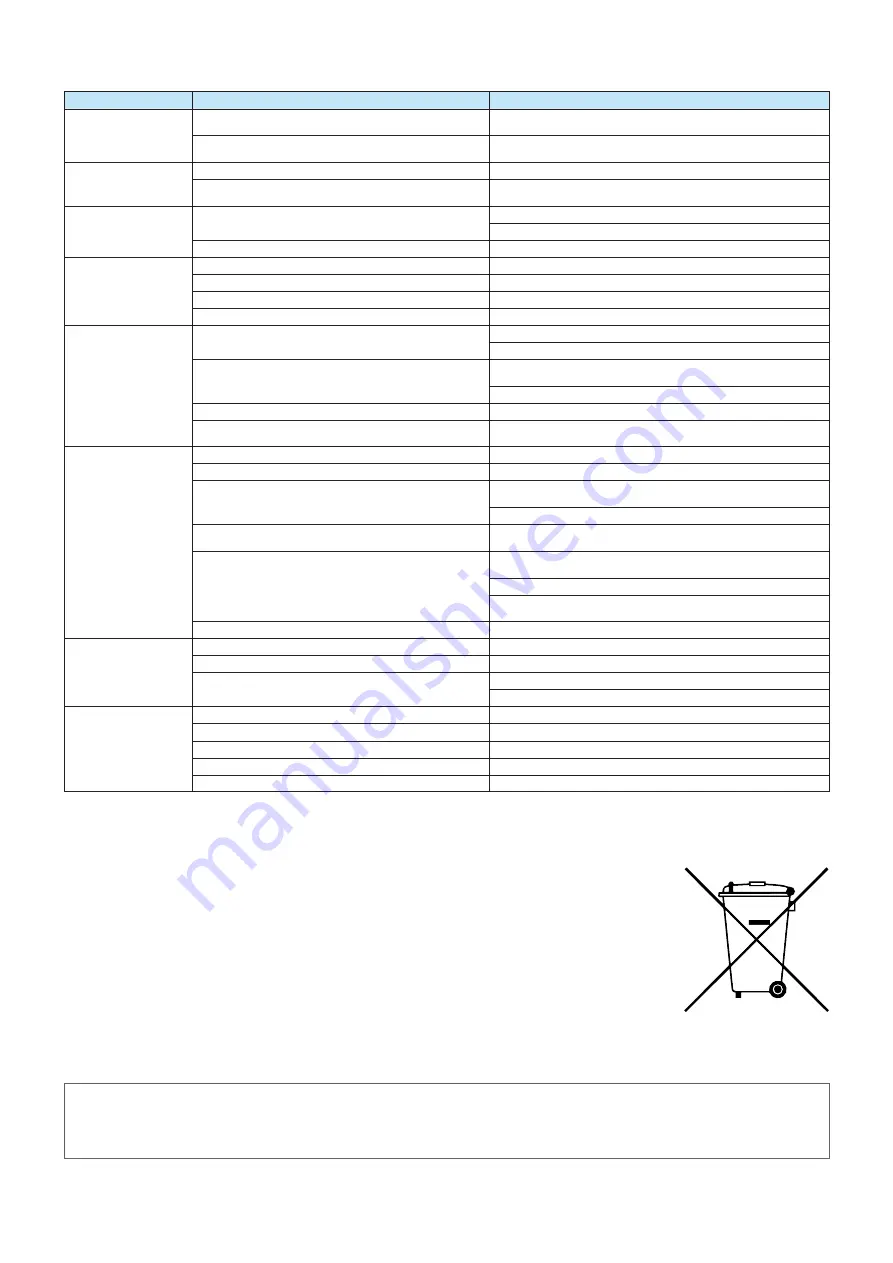
Maintenance
35
ANY ANOMALIES AND REMEDIES
ANOMALY
CAUSE
REMEDY
Safety valve(s) opening
Exceeding of the max pressure regulated on the valve that
must be equal to the appliance design pressure
Adjustment of block pressure switches and/or limit too high
Safety valve calibration loss
Check and subsequent calibration of the valve using a sample
pressure gauge
Small leak from the
safety valve(s) (leakage)
Dirt around the shutter seat
Cleaning of seat by sometimes acting on the manual opening lever
Scratched shutter seat
Valve disassembly and polishing of the internal seat with very fine
abrasive paste
Pump block
Disconnected pump thermal relay
Check motor absorption
Check thermal calibration
Blocked pump shaft
Electric pump maintenance
Block pressure switch
intervention
Calibrated limit pressure switch too high
Limit pressure switch calibration
Faulty limit pressure switch
Limit pressure switch replacement
Clogged pressure switch coil
Coil cleaning or replacement
Block pressure switch failure
Pressure switch replacement
Level 1 or 2 safety
intervention
Interrupted water level detection
Encrusted stainless steel rod
Interrupted connection cable
Faulty safety level relay
Temporary replacement of electronic safety relay with one of the two
relays in the panel
If the problem is solved, permanently replace the faulty relay.
Lack of water filling
See "Loading" Problems
Incorrect electrical panel probe power supply electrical
cable wiring
Wiring diagram check
Insufficient water
loading
Pump block
See "Pump block" Problems
Dirty pump intake filter
Filter cleaning
Level adjustment anomaly
Temporary replacement of electronic adjustment relay with one of
the two relays in the panel.
If the problem is solved, permanently replace the faulty relay.
Level adjustment probes short-circuit
Disassemble the adjustment probes to visually check the ceramic
insulation
Pump cavitation
Head (=height difference between the collection vessel level and the
pump) insufficient in relation to the water temperature
Pump intake filter cleaning
Reduce resistance of the duct between collection vessel and pump
by increasing the passage section
Pump rotation direction
Invert one of the phases (three-phase pump)
Burner always on
Incorrect connection to the electrical panel
See the wiring diagram
Faulty level safety relays
See "Level 1 or 2 safety intervention"
Block and/or adjustment pressure switches not active
Pressure switches calibration check
Check of pressure switch connections to the electrical panel
Burner always off
Burner problems
See specific Burner manual
Burner fuses interrupted
Fuses replacement
No consent to burner from adjustment pressure switch
Adjustment pressure switch replacement
No consent to burner from level safety relays
See "Level 1 or 2 safety intervention"
Incorrect connection to the electrical panel
See the wiring diagram
ENVIRONMENTAL PROTECTION AND DISPOSAL
Protection and respect for the environment is a fundamental principle for
ICI CALDAIE S.p.A.
.
The quality of products, lower costs and protection of the environment are of equal importance for the
company.
ICI CALDAIE S.p.A.
, also through ISO 14001 certification, strictly adheres to European laws and
standards for the protection and preservation of the environment.
In order to reduce its impact on the environment, the company uses the best technology and materials
in its production processes and always considers their economic impact.
System for 24 or 72 h operation without continuous supervision.
INFORMATION FOR THE DISPOSAL OF ELECTRICAL AND ELECTRONIC EQUIPMENT
m
IMPORTANT
This product contains electrical and electronic equipment which cannot be disposed of through the normal means
of municipal waste collection. There are separate collection centres for these products. Electrical and electronic
equipment must be treated separately and in compliance with the laws in force in the respective Country.
Cooke Industries - Phone: +64 9 579 2185 Email: sales@cookeindustries.co.nz Web: www.cookeindustries.co.nz