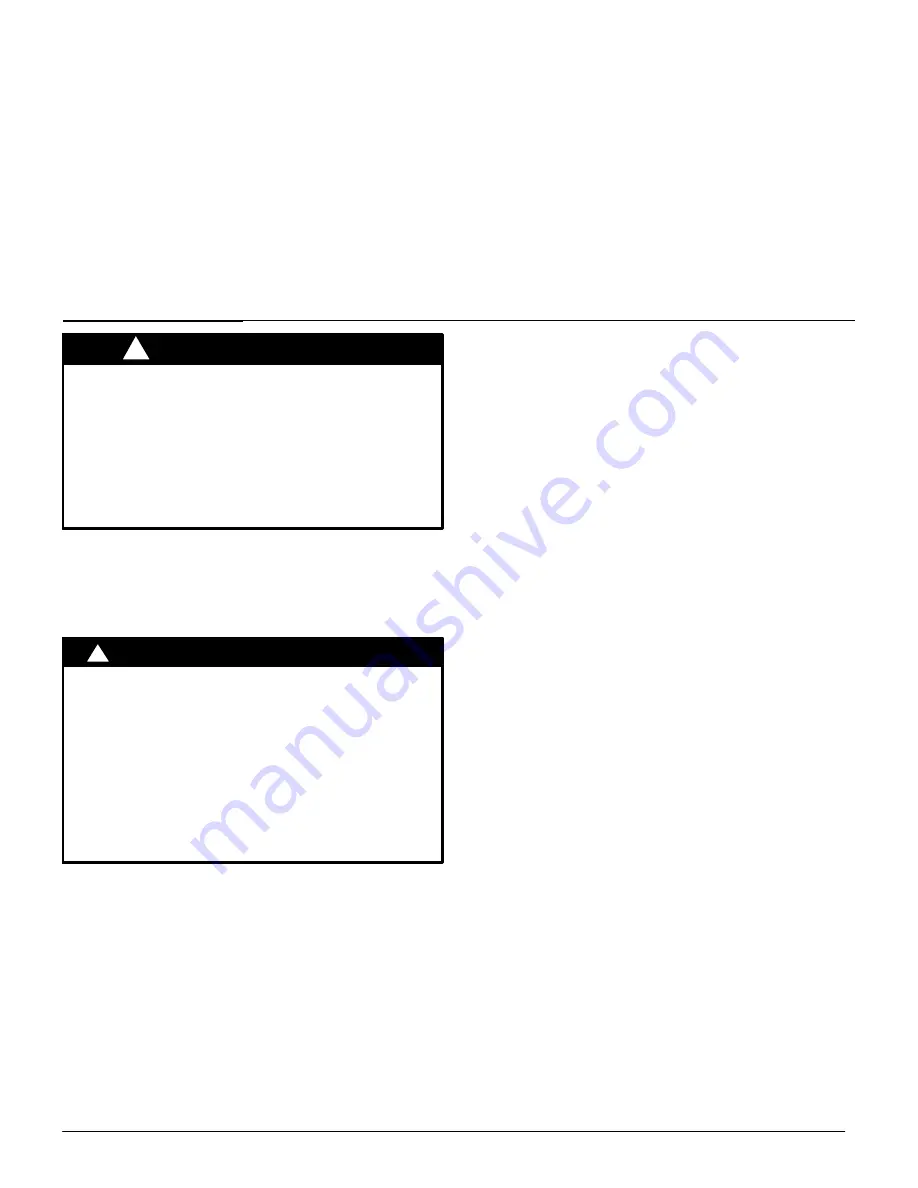
441 01 2314 06
Specifications are subject to change without notice.
4
Your furnace is designed solely to provide a safe and comfortable
living environment. The furnace is NOT designed to ensure that
water pipes will not freeze. It is equipped with several safety de-
vices that are designed to turn the furnace off and prevent it from
restarting in the event of various potentially unsafe conditions.
If your furnace remains off for an extended time, the pipes in your
home could freeze and burst, resulting in water damage.
If the structure will be unattended during cold weather you should
take these precautions.
1. Turn off the water supply to the structure and drain the water
lines if possible and add an antifreeze for potable water to
drain traps and toilet tanks. Open faucets in appropriate
areas.
−
or
−
2. Have someone check the structure frequently during cold
weather to make sure it is warm enough to prevent pipes
from freezing. Instruct them on a service agency to call to
provide service, if required.
−
or
−
3. Install a reliable remote sensing device that will notify some-
body of freezing conditions within the home.
2. Installation
CARBON MONOXIDE POISONING HAZARD
Failure to follow this warning could result in
personal injury or death.
If this furnace is replacing a previously common-
vented furnace, it may be necessary to resize the
existing vent system to prevent oversizing prob-
lems for the other remaining appliances(s). See
Venting and Combustion Air Check
in the
Gas Vent
Installation
section of this instruction
.
!
WARNING
Location and Clearances
If furnace is a replacement, it is usually best to install the furnace
where the old one was. Choose the location or evaluate the exist-
ing location based upon the minimum clearance and furnace di-
mensions
(Figure 1)
.
CARBON MONOXIDE POISONING HAZARD
Failure to follow this warning could result in
personal injury or death.
Do NOT operate furnace in a corrosive
atmosphere containing chlorine, fluorine or any
other damaging chemicals, which could shorten
furnace life.
Refer to
Combustion & Ventilation Air
section,
Contaminated Combustion Air for combustion air
evaluation and remedy.
!
WARNING
Installation Requirements
1. Install furnace level.
2. This furnace is
NOT
to be used for temporary heat of buildings
or structures under construction.
3. Install furnace as centralized as practical with respect to the
heat distribution system.
4. Install the vent pipes as short as practical. (See
Gas Vent
Installation
section).
5. Do
NOT
install furnace directly on carpeting, tile or other com-
bustible material. See
Ductwork and Filter
Sub
−
base for Com-
bustible Floors.
6. Maintain clearance for fire safety and servicing. A front clear-
ance of 24
″
(609.6mm) required and 30
″
(762mm) recommen-
ded for access to the burner, controls and filter. See clearance
requirements in
Figure 1.
7. Use a raised base if the floor is damp or wet at times.
8. Residential garage installations require:
•
Burners and ignition sources installed at least 18
″
above
the floor.
•
Furnace must be located or physically protected from
possible damage by a vehicle.
9. If the furnace is to be suspended from the floor joists in a base-
ment or a crawl space or the rafters in an attic, it is necessary to
use steel pipe straps or an angle iron frame to attach the fur-
nace. These straps should be attached to the furnace bottom
side with sheet metal screws and to the rafters or joists with
bolts. The preferred method is to use an angle iron frame
bolted to the rafters or joists.
10. This furnace may be used for construction heat provided that:
•
The furnace is permanently installed with all electrical wir-
ing, piping, venting and ducting installed according to
these installation instructions. A return air duct is provided,
sealed to the furnace casing, and terminated outside the
space containing the furnace. This prevents a negative
pressure condition as created by the circulating air blower,
causing a flame rollout and/or drawing combustion prod-
ucts into the structure.
•
The furnace is controlled by a thermostat. It may not be
“hot wired” to provide heat continuously to the structure
without thermostatic control.
•
Clean outside air is provided for combustion. This is to
minimize the corrosive effects of adhesives, sealers and
other construction materials. It also prevents the entrain-
ment of drywall dust into combustion air, which can cause
fouling and plugging of furnace components.
•
The temperature of the return air to the furnace is main-
tained between 55
°
F (13
°
C) and 80
°
F (27
°
C) , with no
evening setback or shutdown. The use of the furnace
while the structure is under construction is deemed to be
intermittent operation per our installation instructions.
•
The air temperature rise is within the rated rise range on
the furnace rating plate, and the firing rate has been set to
the rating plate value.
•
The filters used to clean the circulating air during the
construction process must be either changed or thorough-
ly cleaned prior to occupancy.
•
The furnace, ductwork and filters are cleaned as neces-
sary to remove drywall dust and construction debris from
all HVAC system components after construction is com-
pleted.
•
Verify proper furnace operating conditions including igni-
tion, gas input rate, air temperature rise, and venting ac-
cording to these installation instructions.