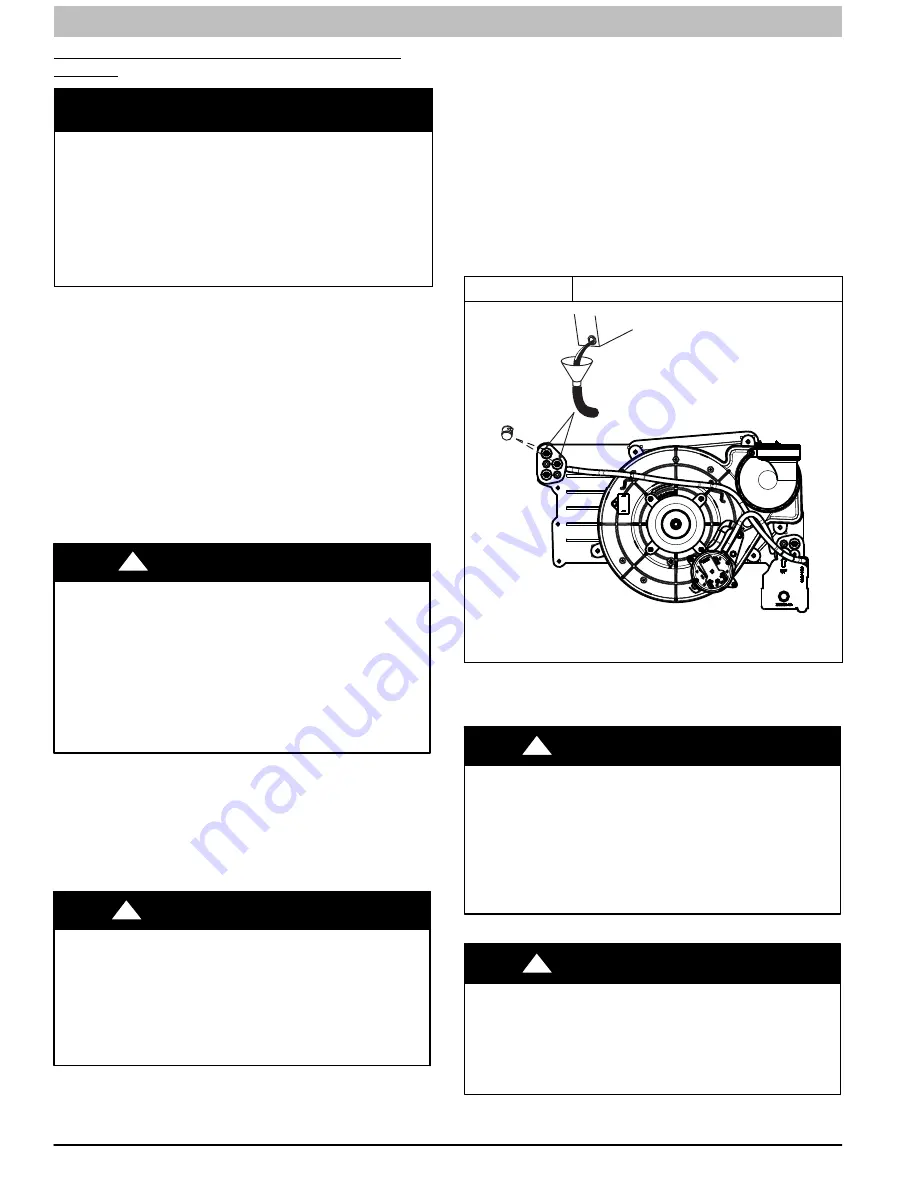
SERVICE AND TECHNICAL SUPPORT MANUAL
Gas Furnace: F9MES
Specifications subject to change without notice.
4
440 04 4900 02
START
−
UP, ADJUSTMENT, AND SAFETY
CHECK
NOTICE
IMPORTANT INSTALLATION AND START
−
UP
PROCEDURES
Failure to follow this procedure may result in a nuisance smoke
or odor complaint.
The manifold pressure, gas rate by meter clocking, temperature
rise and operation must be checked after installation. Minor
smoke and odor may be present temporarily after start
−
up from
the manufacturing process. Some occupants are more
sensitive to this minor smoke and odor. It is recommended that
doors and windows be open during the first heat cycle.
General
1. Furnace must have a 220
−
V 50Hz power supply properly
connected and grounded.
NOTE
: Proper polarity must be maintained for 220
−
V 50Hz
wiring. Control status indicator light flashes code 10 and
furnace does not operate if polarity is incorrect or if the furnace
is not grounded.
2. Thermostat wire connections at terminals R, W, G, and Y
must be made at 24-v terminal block on furnace control.
3. Natural gas service pressure must not exceed 0.5 psig
(14- in. w.c., 1125 Pa), but must be no less than 0.16
psig (4.5-in. w.c., 350 Pa).
4. Blower door must be in place to complete 220
−
V 50Hz
electrical circuit and supply power to the furnace
components.
UNIT OPERATION HAZARD
Failure to follow this caution may result in intermittent unit
operation or performance satisfaction.
These furnaces are equipped with a manual reset limit
switch in burner assembly. This switch opens and shuts off
power to the gas valve if an overheat condition (flame
rollout) occurs in the burner assembly/enclosure. Correct
inadequate combustion
−
air supply, improper gas pressure
setting, improper burner or gas orifice positioning, or
improper venting condition before resetting switch. DO
NOT jumper this switch.
CAUTION
!
Before operating furnace, check flame rollout manual reset
switch for continuity. If necessary, press button to reset switch.
EAC
−
1 (220vac) terminal is energized whenever blower
operates. HUM (220vac) terminal is only energized when the
draft inducer is energized in heating.
HUM (24vac) terminal is only energized on a call for heat (W)
and the LPS is closed.
Prime Condensate Trap with Water
CARBON MONOXIDE POISONING HAZARD
Failure to follow these warnings could result in personal
injury or death.
Failure to use a properly configured trap or NOT
water-priming trap before operating furnace may allow
positive pressure vent gases to enter the structure through
drain tube. Vent gases contain carbon monoxide which is
tasteless and odorless.
!
WARNING
1. Remove upper and middle collector box drain plugs
opposite of the condensate trap. (See
2. Connect field-supplied 5/8-in. (16 mm) ID tube with
attached funnel (see
drain connection.
3. Pour one quart (liter) of water into funnel/tube. Water
should run through collector box, overfill condensate
trap, and flow into open field drain.
4. Remove funnel; replace collector box drain plug.
5. Connect field-supplied 5/8-in. (16 mm) ID tube to middle
collector box drain port.
6. Pour one quart (liter) of water into funnel/tube. Water
should run through collector box, overfill condensate
trap, and flow into open field drain.
7. Remove funnel and tube from collector box and replace
collector box drain plug.
Figure 1
Priming Condensate Drain
L11F065
Representative drawing only, some models may vary in appearance.
Purge Gas Lines
If not previously done, purge the lines after all connections
have been made and check for leaks.
FIRE OR EXPLOSION HAZARD
Failure to follow this warning could result in personal injury,
death, and/or property damage.
Never purge a gas line into a combustion chamber. Never
test for gas leaks with an open flame. Use a commercially
available soap solution made specifically for the detection
of leaks to check all connections. A fire or explosion may
result causing property damage, personal injury or loss of
life.
!
WARNING
Adjustments
FIRE HAZARD
Failure to follow this warning could result in personal injury,
death and/or property damage.
DO NOT bottom out gas valve regulator adjusting screw.
This can result in unregulated manifold pressure and result
in excess overfire and heat exchanger failures.
!
WARNING