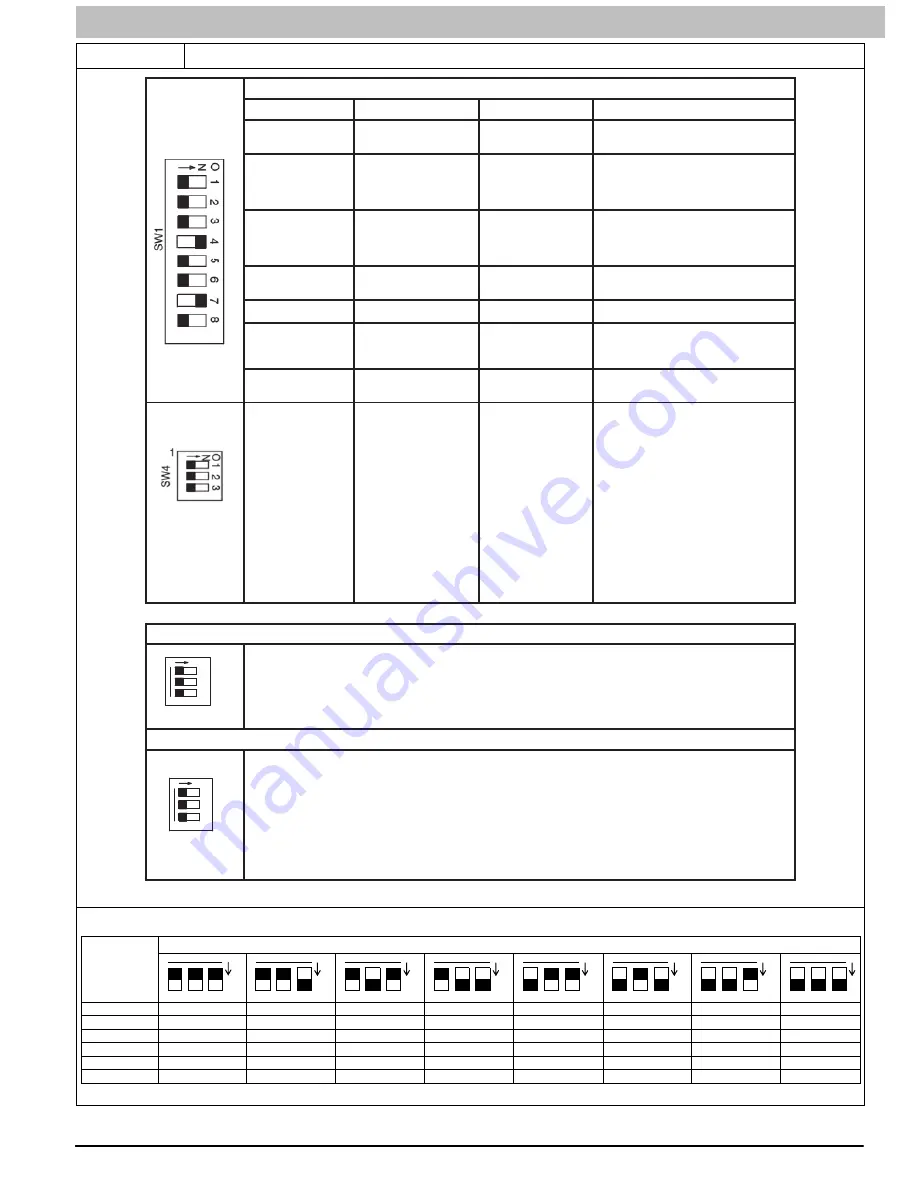
SERVICE AND TECHNICAL SUPPORT MANUAL
Gas Furnace: (F/G)9MVE
Specifications subject to change without notice.
440 04 4800 00
13
Figure 5
Furnace Setup Switch Description
L12F035
SETUP SWITCH
SWITCH NAME
NORMAL POSITION
DESCRIPTION OF USE
Furnace Setup Switch Description
SW1
ï
1
Status Code Recovery
OFF
Turn ON to retrieve up to 7 stored status codes for
troubleshooting assistance when R thermostat lead is
disconnected.
SW1
ï
2
Low Heat Only
(Adaptive Heat Mode when SW1
ï
2 is OFF)
OFF
When SW1
ï
2 is OFF allows two
ï
stage operation with
a single stage thermostat. Turn ON when using two
ï
stage thermostat to allow Low Heat operation when R
to W/W1 closes and High Heat operation when R to
W/W1 and W2 close.
SW1
ï
3
Low Heat Rise Adjustment
OFF
Turn ON to increase Low Heat airflow by 18 percent.
This compensates for increased return air
temperature caused with bypass humidifier. This also
increases the low heat inducer speed 15 percent.
SW1
ï
4
Comfort/Efficiency Adjustment
ON
Turn ON to decrease low heat airflow by 7 percent,
and high heat airflow 10 percent for maximum
comfort.
SW1
ï
5
CFM per ton adjust
OFF
Turn ON for 400 CFM per ton, Turn OFF for 350 CFM
per ton. See also SW4.
SW1
ï
6
Component Self Test
OFF
Turn ON to initiate Component Self Test for
troubleshooting assistance when R thermostat lead is
disconnected. Turn OFF when Self Test is completed.
SW1
ï
7 & SW1
ï
8
Blower OFF delay
ON or OFF
Blower Off Delay time – adjustable 90 seconds to 180
seconds. See table in Adjustments section or refer to
unit wiring diagram.
SW4
ï
3
CFM per ton Adjust
OFF
Allows additional CFM per ton selections when used
with SW 1
ï
5
325 CFM per ton (nominal) when SW 4
ï
3 ON and SW
1
ï
5 OFF
350 CFM per ton (nominal) when SW 4
ï
3 OFF and
SW 1
ï
5 OFF
370 CFM per ton (nominal) when SW4
ï
3 ON and SW
1
ï
5 ON
400 CFM per ton (nominal) when SW 1
ï
5 ON and SW
4
ï
3 OFF
See Air Delivery Tables for model specific CFM vs.
static pressure
AIR CONDITIONING (A/C) SETUP SWITCHES
SW 2, AC (Cooling Airflow) SETUP SWITCHES
O
N
1
1
2
The AC setup switch selects desired cooling or high stage cooling (two stage units) airflow.
See Cooling Air Delivery Tables for specific switch settings.
CONTINUOUS FAN (CF) SETUP SWITCHES
SW 3, CF (Continuous Fan) SETUP SWITCHES
The CF setup switch selects desired Continuous Fan Airflow
O
N
1
2
3
1
SW3
2
3
AC
SW2
The CF switch position is the low cooling airflow selection for two stage cooling units.
The CFM values are shown in the Air Delivery Tables below for SW 3 settings.
SW 3 cannot be set for airflow higher than SW 2.
See Continuous Fan Air Flow Table for specific switch settings.
3
CF
BASED ON 350 CFM/TON (Factory Default: SW1
−
5 = OFF, SW4
−
3 = OFF)
O
O
O
O
O
O
O
O
3
2
1
N
3
2
1
N
3
2
1
N
3
2
1
N
3
2
1
N
3
2
1
N
3
2
1
N
3
2
1
N
040-10
060-14
080-16
080-20
100-20
120-22
(
y
)
Model Size
CONTINUOUS FAN AND LOW COOLING AIRFLOW: SET-UP SWITCH SW3 POSITIONS
525
525
700
875
950
950
950
950
525
525
700
875
1050
1225
1400
1400
1400
1400
1225
1400
1750
525
525
700
875
1050
1225
525
525
700
875
1050
1400
1750
525
525
700
875
1050
1225
1400
1750
525
525
700
875
1050
1225
L11F097