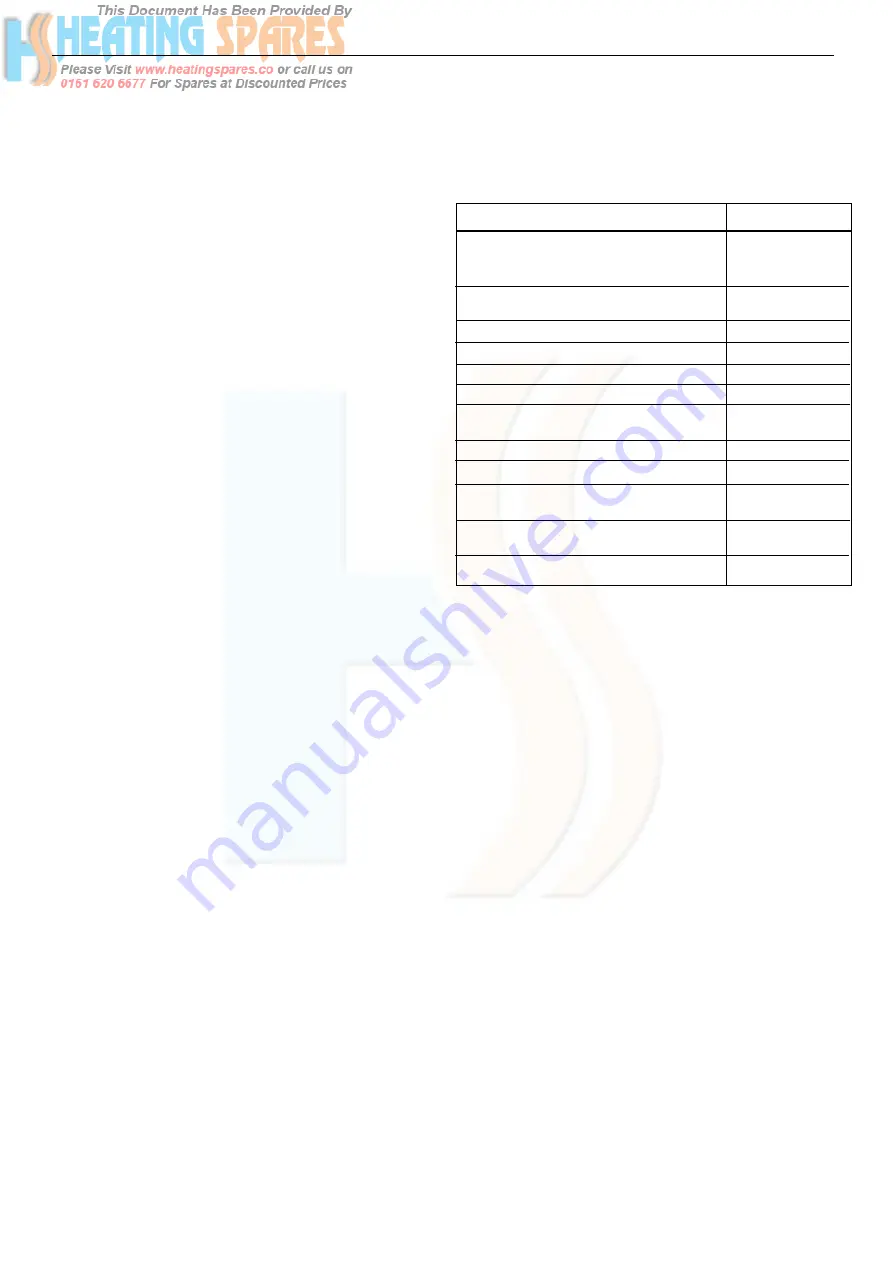
Supplied By www.heating spares.co Tel. 0161 620 6677
British Gas RD1
-
Installation & Servicing
7
GENERAL
IMPORTANT
. It is absolutely ESSENTIAL to ensure, in
practice, that products of combustion discharging from the
terminal cannot re-enter the building or any other adjacent
building through ventilators, windows, doors, other sources of
natural air infiltration, or forced ventilation/air conditioning.
If this should occur, the appliance MUST be turned OFF,
labelled 'unsafe' and corrective action taken.
TERMINAL
The terminal assembly can be adapted to accommodate
various wall thicknesses. Refer to Frame 9.
AIR SUPPLY
Detailed recommendations for air supply are given in
BS.5440:2. The following notes are for general guidance:
1.
It is NOT necessary to have a purpose provided air vent in
the room or internal space in which the boiler is installed.
2.
If the boiler is to be installed in a cupboard or compartment,
permanent air vents are required (for cooling purposes) in
Compartment Installations
A compartment used to enclose the boiler MUST be designed
and constructed specially for this purpose.
An existing cupboard or compartment may be used, provided it
is modified for the purpose.
In both cases details of essential features of cupboards/
compartment design, including airing cupboard installation, are
to conform to the following :
BS. 6798.
The position selected for installation MUST allow adequate
space for servicing in front of the boiler and for air circulation
around the boiler. Refer to 'Air Supply' on page 8.
For the minimum clearances required for safety and
subsequent service refer to the Wall mounting diagram,
Frame 2. In addition, sufficient space may be required to
allow lifting access to the wall mounting plate.
GAS SUPPLY
The local gas supplier should be consulted, at the installation
planning stage, in order to establish the availability of an
adequate supply of gas. An existing service pipe must NOT be
used without prior consultation with the local gas supplier.
The boiler is to be installed only on a gas supply with a
governed meter.
A gas meter can only be connected by the local gas supplier or
by a local regional contractor.
An existing meter should be checked, preferably by the gas
supplier, to ensure that the meter is adequate to deal with the
rate of gas supply required. A MINIMUM pressure of 20 mbar
MUST be available at the boiler inlet with the boiler operating.
Installation pipes MUST be fitted in accordance with BS. 6891.
Pipework from the meter to the boiler MUST be of an adequate
size.100 models should be piped in 22mm minimum. The final
1metre may be run in 15mm if it is visible.
The complete installation MUST be tested for gas soundness
and purged as described in the above code.
FLUE INSTALLATION
The flue must be installed in accordance with the recommendations
of BS. 5440:1.
The following notes are intended for general guidance:-
1
. The boiler MUST be installed so that the terminal is exposed
to external air.
2.
It is important that the position of the terminal allows the free
passage of air across it at all times.
3.
Minimum acceptable spacing from the terminal to
obstructions and ventilation openings are specified in Table
3.
4.
Where the lowest part of the terminal is fitted less than 2m
(6'6") above a balcony, above ground or above a flat roof to
which people have access then the terminal MUST be
protected by a purpose designed guard.
Terminals guards are available from boiler suppliers - ask for
Tower Flue Guard, Model K1.
In case of difficulty seek advice from:
Tower Flue Components Ltd.,
Vale Rise, Tonbridge, Kent TN9 1TB (Model K1)
Telephone No. 01732 351 555
Ensure that the guard is fitted centrally.
5.
Where the terminal is fitted within 1000mm (39
1/2
") of a plastic
or painted gutter or 500mm (19
1/2
") of painted eaves then an
aluminium shield at least 1000mm (39
1/2
") long should be
fitted to the underside of the gutter or painted surface.
6.
The air inlet/products outlet duct and the terminal of the boiler
MUST NOT be closer than 25mm (1") to combustible material.
Detailed recommendations on the protection of combustible
material are given in BS.5440: 1990.
Table 3 - Balanced flue terminal position
Terminal Position
M i n i m u m S p a c i n g
1.
Directly below or alongside an
opening window, air vent or other
ventilation opening
300 mm (12")
2.
Below guttering, drain pipes or soil
pipes
75 mm
( 3")
3
.
Below eaves
200 mm
( 8")
4.
Below balconies or a car port roof
200 mm
( 8")
5.
From vertical drain pipes or soil pipes
75 mm
( 3")
6.
From internal or external corners
300 mm ( 12")
7.
Above adjacent ground, roof or
balcony level
300 mm (12")
8.
From a surface facing the terminal
600 mm (24")
9.
From a terminal facing a terminal
1200 mm (48")
10.
From an opening in a car port
(e.g. door or window) into dwelling
1200 mm (48")
11.
Vertically from a terminal on the
same wall
1500 mm (60")
12.
Horizontally from a terminal on the wall
300 mm (12")