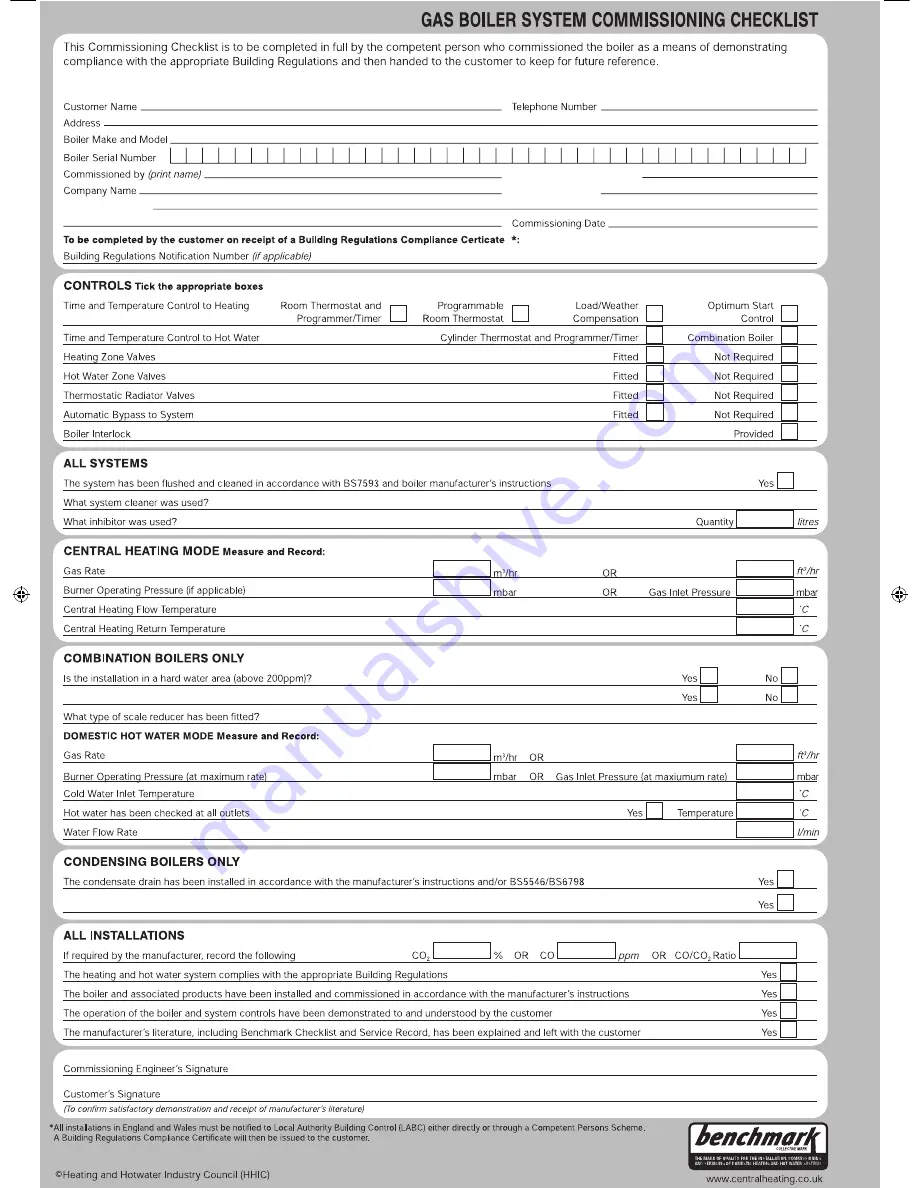
Gas Safe Register Number
Gas Safe Register Number
Gas Safe Register Number
Gas Safe Register Number
Gas Safe Register Number
Gas Safe Register Number
Gas Safe Register Number
Gas Safe Register Number
Gas Safe Register Number
Gas Safe Register Number
Gas Safe Register Number
Failure to install and commission according to the manufacturer’s instructions and complete this Benchmark Commissioning Checklist will invalidate the warranty. This
does not affect he customer’s statutory rights.
If yes, and if required by the manufacturer, has a water scale reducer been fitted?
If the condensate pipe terminates externally has the pipe diameter been increased and weatherproof insulation fitted?
Telephone Number
206279-1.indd 62
06/01/2011 09:10:53
Summary of Contents for LOGIC Code Combi 26
Page 2: ...2 Ideal Logic Code Combi Installation and Servicing ...
Page 61: ......