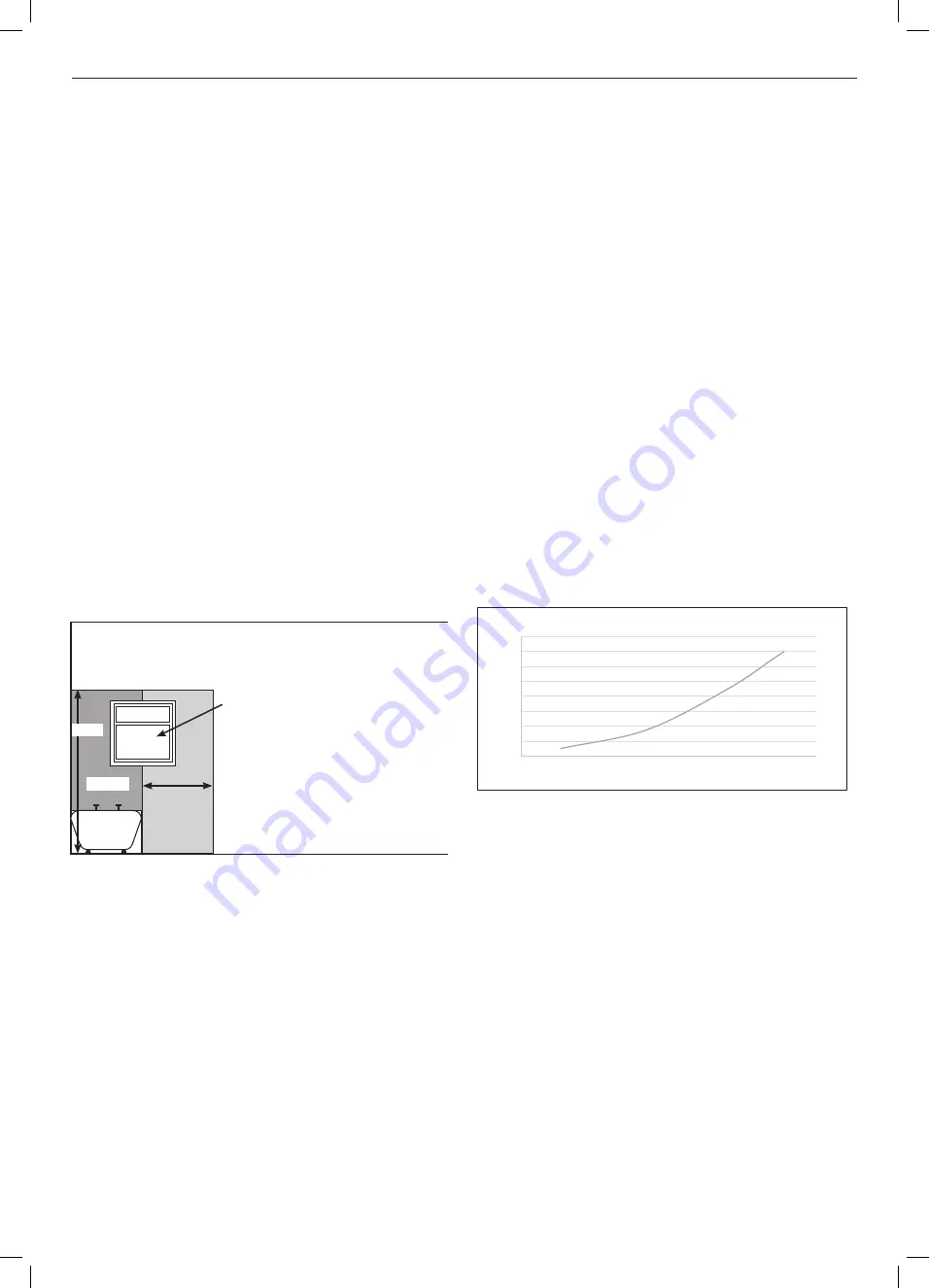
12
Installation and Servicing
SECTION 1 - GENERAL
1.8 GAS SUPPLY
The local gas supplier should be consulted, at the installation
planning stage, in order to establish the availability of an adequate
supply of gas. An existing service pipe must NOT be used without
prior consultation with the local gas supplier.
The boiler MUST be installed on a gas supply with a governed
meter only.
A gas meter can only be connected by the local gas supplier or
by a Gas Safe Registered Engineer. In IE by a Registered Gas
Installer (RGII).
An existing meter should be checked, preferably by the gas
supplier, to ensure that the meter is adequate to deal with the rate
of gas supply required.
It is the responsibility of the Gas Installer to size the gas installation
pipework in accordance with BS6891. Whilst the principle of the
1:1 gas valve ensures the Vogue Max Combi range is able to
deliver its full output at inlet pressures as low as 14mb, other gas
appliances in the property may not be as tolerant. When operating
pressures are found to be below the minimum meter outlet of 19mb
these should be checked to ensure this is adequate for correct and
safe operation.
Allowing for the acceptable pressure loss of 1mb across the
installation pipework, it can be assumed that a minimum permitted
operating pressure of 18mb will be delivered to the inlet of
the appliance. (Reference BS 6400-1 Clause 6.2 Pressure
Absorption).
The external gas cock could further reduce the operating pressure
when measured at its test point. The pressure drop is relative to
the heat input to the boiler (kW), refer to graph below.
0
0.02
0.04
0.06
0.08
0.1
0.12
0.14
0.16
0
5
10
15
20
30
35
40
45
50
Pre
ass
ure
Dro
p
(m
ba
r)
25
Heat Input (kW)
Gas Cock Pressure Drop (mbar)
IMPORTANT.
Ensure all gas valve connections are gas tight with a gas
soundness check up to the gas control valve.
Installation pipes must be fitted in accordance with BS.6891. In IE
refer to IS.813.
The complete installation MUST be tested for gas tightness and
purged as described in the above code.
1.9 FLUE INSTALLATION
Pluming will occur at the terminal so terminal positions where this
could cause a nuisance should be avoided.
The flue must be installed in accordance with the recommendations
of BS. 5440-1.
In IE refer to I.S. 813.
The following notes are intended for general guidance:
1.
The boiler MUST be installed so that the terminal is exposed to
external air.
2.
It is important that the position of the terminal allows the free
passage of air across it at all times.
3.
Minimum acceptable spacing from the terminal to obstructions
and ventilation openings are specified in Table 4.
1.7 LOCATION OF BOILER
The boiler must be installed on a flat and vertical internal wall,
capable of adequately supporting the weight of the boiler and any
ancillary equipment.
The boiler may be fitted on a combustible wall and insulation
between the wall and the boiler is not necessary, unless required
by the local authority.
For electrical safety reasons there must be no access available
from the back of the boiler.
T
he boiler must not be fitted outside.
Timber Framed Buildings
If the boiler is to be fitted in a timber Framed building it should be
fitted in accordance with the Institute of Gas Engineering document
IGE/UP/7 - Edition 2.
Bathroom Installations
This appliance is rated
IP20.
The boiler may be installed in any room or internal space, although
particular attention is drawn to the requirements of the current
IEE (BS.7671) Wiring Regulations and the electrical provisions
of the building regulations applicable in Scotland, with respect to
the installation of the boiler in a room or internal space containing
a bath or shower. For IE reference should be made to the current
ETCI rules for electrical installations and I.S. 813.
If the appliance is to be installed in a room containing a bath or
shower then, providing water jets are not going to be used for
cleaning purposes (as in communal baths/showers), the appliance
must be installed beyond Zone 2, as detailed in BS.7671.
0.6m
Zone 0
Recessed
window
Zone 2
Ceiling
3G8913a
2.25m
Zone 1
Compartment Installations
A compartment used to enclose the boiler should be designed and
constructed specially for this purpose.
An existing cupboard or compartment may be used, provided that
it is modified for the purpose.
Braces for compartments must be easily removable for service access.
In both cases, details of essential features of cupboard /
compartment design, including airing cupboard installation, are to
conform to the following:
•
BS 6798 (No cupboard ventilation is required - see ‘Air Supply’
for details).
•
The position selected for installation MUST allow adequate
space for servicing in front of the boiler.
•
For the minimum clearances required for safety and
subsequent service, see the wall mounting template and
Section 1.16. In addition, sufficient space may be required to
allow lifting access to the wall mounting plate.
Summary of Contents for VOGUE MAX COMBI 26
Page 4: ...4 Installation and Servicing...
Page 6: ...6 Installation and Servicing...
Page 74: ......