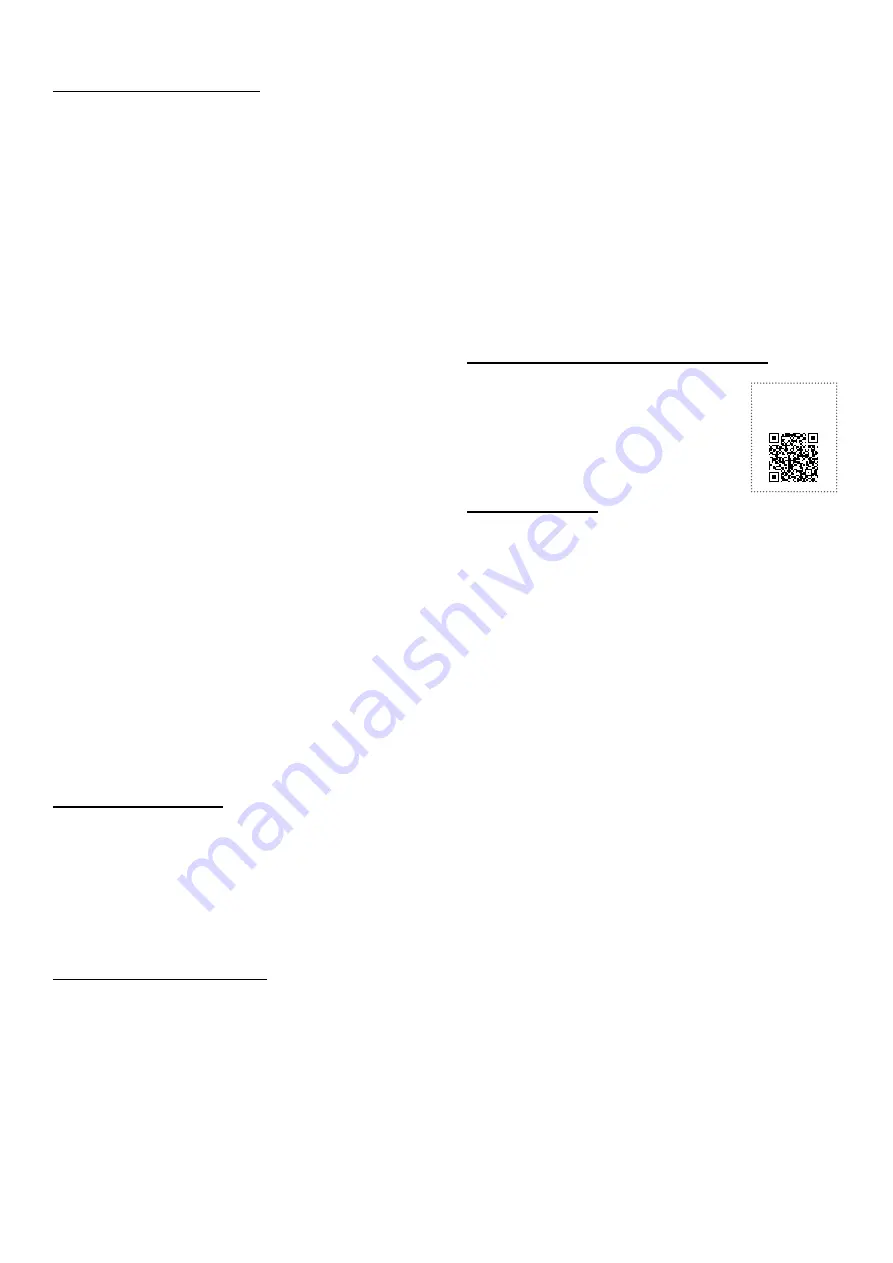
8
Installation and Servicing
Section 1 - General
1.1 INTRODUCTION
The Logic System
2
range of boilers are wall mounted,
condensing, system gas boilers.
Features:
• High efficiency
• Full sequence
• Automatic spark ignition
• Low water content
• Fanned flue
The boiler is supplied fully assembled with circulating pump,
pressure gauge, PRV and CH expansion vessel.
A variable temperature control is fitted on the user control.
The boiler includes as standard:
-
Boiler frost protection
-
Daily pump exercise.
Note.
The appliance must be wired with a permanent live
supply, or the boiler frost protection will not operate. The boiler
warranty will be invalid if this requirement is not complied with.
The boiler casing is of white painted mild steel with a white
polymer front panel.
The boiler temperature control is visibly located in the control
panel on the front of the boiler.
The heat exchanger is manufactured from cast aluminium.
The boiler is suitable for connection to fully pumped, sealed
heating systems ONLY. Adequate arrangements for completely
draining the system by provision of drain cocks MUST be
provided in the installation pipework.
Pipework from the boiler is routed downwards.
A PRV grommet is fitted to the boiler which requires the correct
fitting and securing of a clip (supplied) to ensure safe discharge
of the PRV should this occur.
Data Plate
The boiler model and serial number can be located on the
bottom of the boiler casing, shown in Section 1.16 - Water &
Gas Connection Diagram.
1.2 OPERATION
When there is a demand for CH, the heating system is supplied
at the selected temperature of between 30
o
C and 80
o
C.
The boiler features a comprehensive diagnostic system which
gives detailed information on the boiler status when operating,
and performance of key components to aid commissioning and
fault finding.
1.3 SAFE HANDLING
This boiler may require 2 or more operatives to move it to its
installation site, remove it from its packaging base and during
movement into its installation location. Manoeuvring the boiler
may include the use of a sack truck and involve lifting, pushing
and pulling.
Caution should be exercised during these operations.
Operatives should be knowledgeable in handling techniques
when performing these tasks and the following precautions
should be considered:
•
Grip the boiler at the base.
•
Be physically capable.
•
Use personal protective equipment as appropriate,
e.g. gloves, safety footwear.
During all manoeuvres and handling actions, every attempt
should be made to ensure the following unless unavoidable
and/or the weight is light.
•
Keep back straight.
•
Avoid twisting at the waist.
•
Avoid upper body/top heavy bending.
•
Always grip with the palm of the hand.
•
Use designated hand holds.
•
Keep load as close to the body as possible.
•
Always use assistance if required.
1.4 OPTIONAL ACCESSORIES
Please visit idealheating.com to access the
optional accessories for this boiler.
1.5 SAFETY
Current Gas Safety (installation and use) regulations or
rules in force:
The appliance is suitable only for installation in GB and should
be installed in accordance with the rules in force.
In GB, the installation must be carried out by a Gas Safe
Registered Engineer. It must be carried out in accordance
with the relevant requirements of the:
•
Gas Safety (Installation and Use) Regulations
•
Appropriate Building Regulations, either The Building
Regulations, The Building Regulations (Scotland), Building
Regulations (Northern Ireland).
•
Water Fittings Regulations or Water byelaws in Scotland.
•
Current I.E.E. Wiring Regulations.
Where no specific instructions are given, reference should be
made to the relevant British Standard Code of Practice.
The Boiler has been tested and certified to;
BSEN 15502-1, BSEN 15502-2, BSEN 15502-2-1,
BSEN 60335-1, BSEN 60335-2-102, BSEN 55014-1 and
BSEN 55014-2 for use with Natural Gas & Propane.
Detailed recommendations are contained in the following
British Standard Codes of Practice:
BS5440:1
Flues (for gas appliances of rated input not
exceeding 70 kW).
BS5440:2
Ventilation (for gas appliances of rated input
not exceeding 70 kW).
BSEN. 12828
Heating Systems in buildings: Design for
water based heating systems.
BSEN 12831
Heating Systems in buildings: Method for
calculation of the design heat load.
BSEN 14336
Heating Systems in buildings: Installation
and commissioning of water based heating
systems.
BS5546
Installation of gas hot water supplies for
domestic purposes (2nd Family Gases)
SCAN
for link