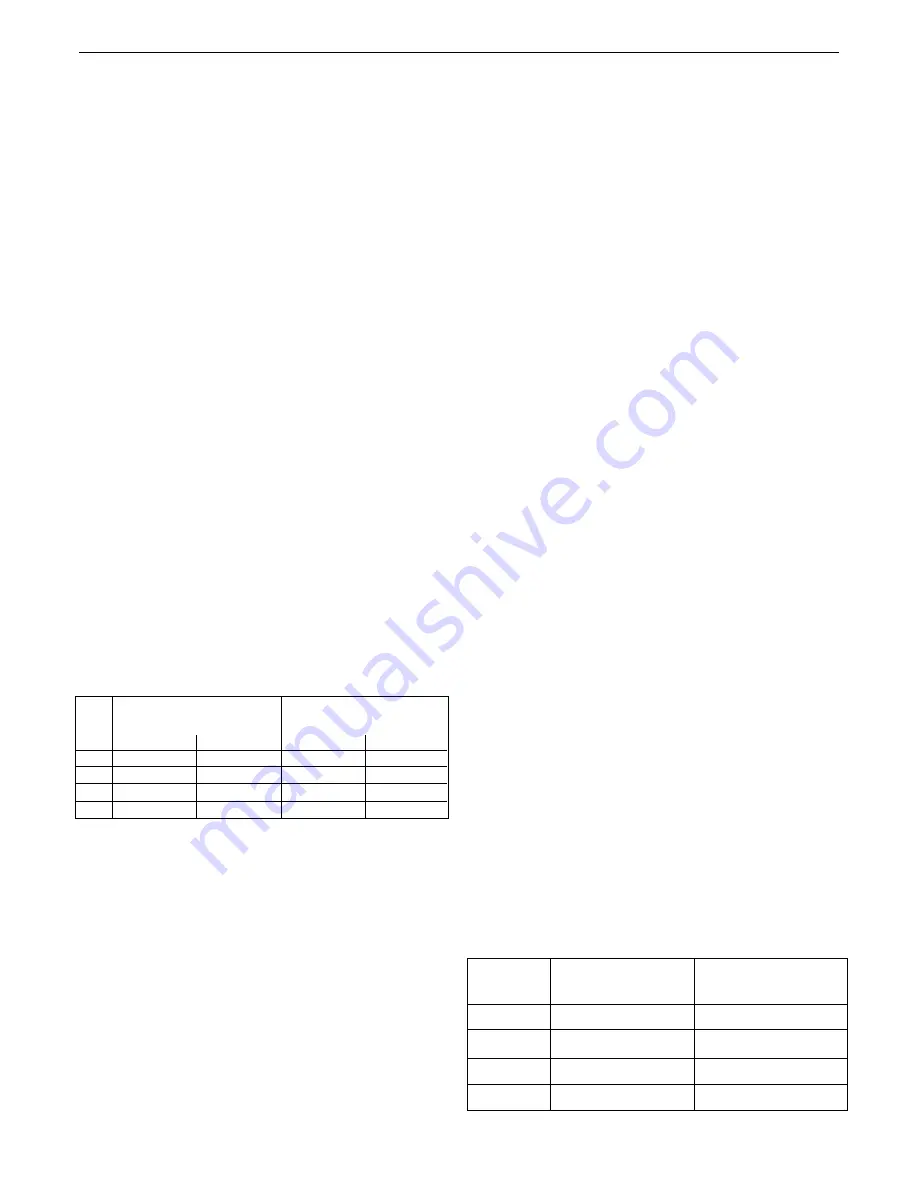
GENERAL
6
IMAX XTRA -
Installation & Servicing
WATER CIRCULATION SYSTEM
A circulation pump MUST be connected to the boiler, see below.
The boiler must NOT be used for direct hot water supply. The hot
water storage cylinder MUST be of the indirect type.
Single feed, indirect cylinders are not recommended and MUST
NOT be used on sealed systems.
The appliances are NOT suitable for gravity central heating nor
are they suitable for the provision of gravity domestic hot water.
The hot water cylinder and ancillary pipework, not forming part of
the useful heating surface, should be lagged to prevent heat loss
and any possible freezing - particularly where pipes run through
roof spaces and ventilated underfloor spaces.
The boiler must be vented. There must be no low points between
the boiler flow connection and a system vent point, which should
be positioned as close as practically possible to the boiler flow
connection.
Draining taps MUST be located in accessible positions, which
permit the draining of the whole system - including the boiler
and hot water storage vessel. They should be at least 1/2" BSP
nominal size and be in accordance with BS. 2879. Do not use
the boiler drain tap to drain the system as this can induce sludge
into the heat exchanger.
The central heating system should be in accordance with the
relevant standards listed on page 4.
Due to the compact nature of the boiler the heat stored within the
castings at the point of shutdown of the burner must be dissipated
into the water circuit in order to avoid overheating. In order to
allow pump operation after burner shutdown the boiler control box
incorporates a 5 minute pump overrun facility. In order to make
use of this, a pump must be supplied from the terminals inside the
boiler. Note: for pumps requiring greater than 1.0 amp current,
they must be connected via a relay.
When sizing pumps, reference should be made to the Hydraulic
Resistance Table on page 6 which show the boiler resistance
against flow rates, to achieve the required temperature
differential.
Flow rates for common systems using either 11
o
C or 20
o
C
temperature differentials are given in the table below.
Water flow rate temp.
Water flow rate temp.
difference 11
o
C (20
o
F)
difference 20
o
C (36
o
F)
l/s m
3
/h l/s m
3
/h
E320
7.14 25.70 3.93 14.15
E400
9.02 32.47 4.96 17.86
E480
10.83 38.99 5.96 21.46
E560
12.63 45.47 6.95 25.02
Note
.
• With the boiler firing at maximum rate, the temperature
differential should not be less than 10
o
C. Higher flow rates
required for lower temperature differentials could lead to
erosion of the heat exchanger water ways.
• With the boiler firing at minimum rate, the temperature
differential should not be greater than 35
o
C. Lower flow rates
generating higher temperature differentials will lead to lock out
of the boiler.
• The lower the return temperature to the boiler, the higher the
efficiency. At return temperatures of 55
o
C and below, the
difference becomes marked because the water in the flue
gases starts to condense, releasing its latent heat.
In installations where all radiators have been provided with
thermostatic radiator valves, it is essential that water circulation
through the boiler is guaranteed. A mixing header will perform
this task. Alternatively this can be best achieved by means of a
differential pressure valve, which is installed in a bypass between
the flow and return pipes. The bypass should be fitted at least
6m from the boiler, and should be capable of allowing a minimum
flow rate to achieve a temperature differential of no greater than
35
o
C at minimum rate.
WATER TREATMENT
These boilers incorporate an ALUMINIUM heat exchanger
.
IMPORTANT.
The application of any other treatment to this
product may render the guarantee of
Ideal Boilers
INVALID.
Ideal Boilers
recommend Water Treatment in accordance with
Guidance Notes on Water Treatment in Central Heating Systems.
Ideal Boilers
recommend the use of Fernox Copal or MB1
or GE Betz Sentinel X100 inhibitors and associated water
treatment products, which must be used in accordance with the
manufacturers' instructions.
For further information contact:
Fernox Manufacturing Co. Ltd
., Cookson Electronics,
Forsyth Road, Sheerwater, Woking, Surrey, GU21 5RZ
Tel: +44 (0) 1799 521133 or
Sentinel Performance Solutions
.,
The Heath Business & Technical Park, Runcorn, Cheshire, WA7
4QX
Tel: 0800 389 4670. www.sentinel-solutions.net
1.
It is most important that the correct concentration of the water
treatment products is maintained in accordance with the
manufacturers' instructions.
2.
If the boiler is installed in an existing system any unsuitable
additives MUST be removed by thorough cleansing.
3.
In hard water areas, treatment to prevent limescale may be
necessary - however the use of artificially softened water is
NOT permitted.
4.
Under no circumstances should the boiler be fired before the
system has been thoroughly flushed.
ELECTRICAL SUPPLY
WARNING. This appliance must be earthed.
Wiring external to the appliance MUST be in accordance with
the current I.E.E. (BS7671) Wiring Regulations and any local
regulations which apply. For Ireland reference should be made to
the current ETCI rules for electrical installations.
The point of connection to the mains should be readily accessible
and adjacent to the boiler.
CONDENSATE DRAIN
Condensate drains are provided on the boiler. These drains must
be connected to a drainage point on site. All pipework and fittings
in the condensate drainage system MUST be made of plastic - no
other materials may be used.
IMPORTANT.
Any external runs must be insulated to avoid
freezing in cold weather causing blocking.
Boiler
Pressure Drop
Pressure Drop
(mbar) @ 20
o
C
(mbar) @ 11
o
C
E320
100
327
E400
105
354
E480
110
388
E560
120
425
HYDRAULIC RESISTANCE
- (
with optional water header pack fitted)