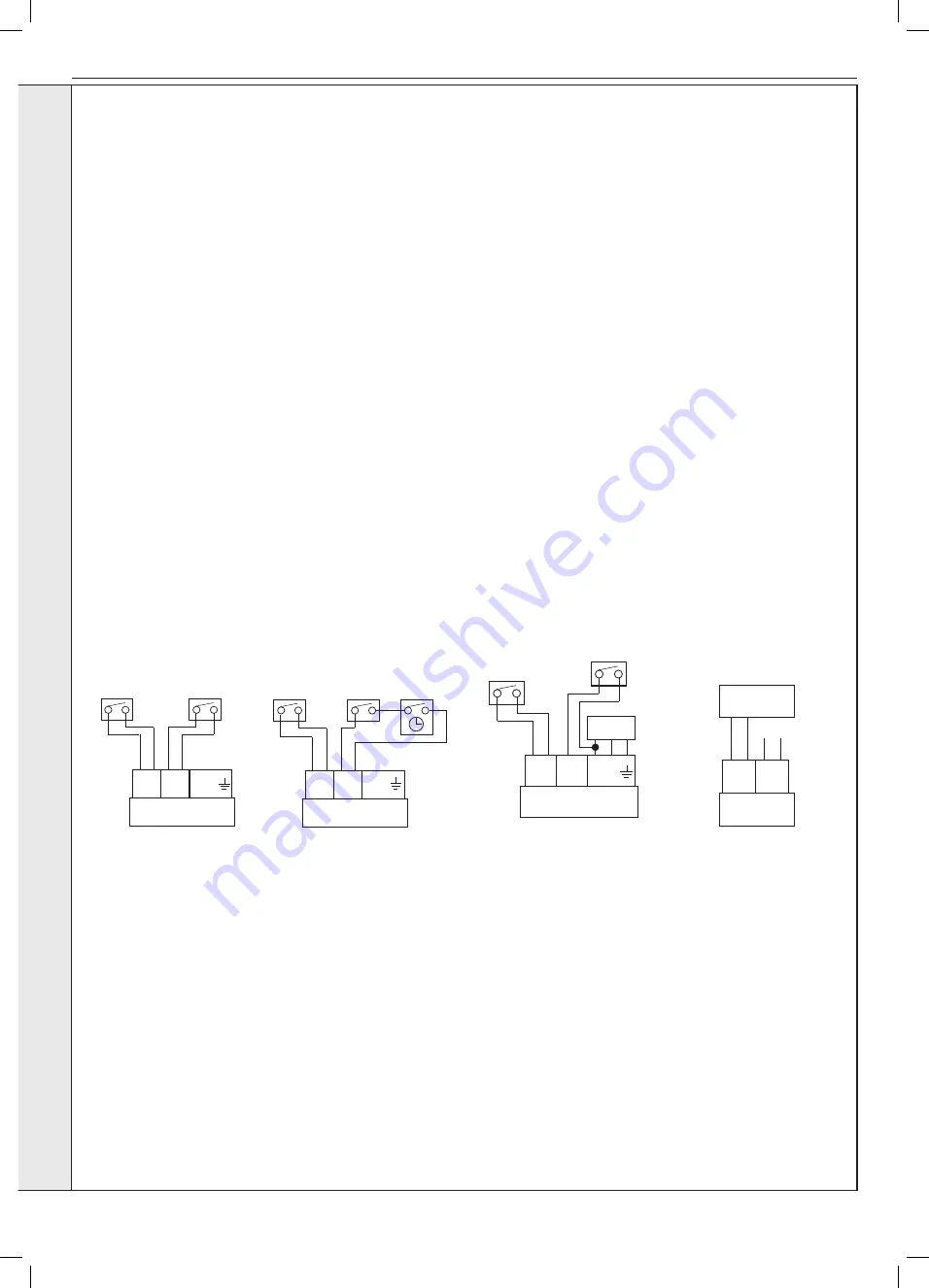
32
Installation and Servicing
SECTION 2 - INSTALLATION
2.19 EXTERNAL WIRING
DIAGRAM A:
DIAGRAM B:
Room Stat with External Timer
Programmable Room Stat or
Room Stat with Internal Timer
Optional
Room Stat or
Optional
Frost
Programmable
Frost
Stat
Room Stat
Stat
Room Stat
Timer
Frost
Room
Frost
Room
Stat
Stat/
L N
Stat
Stat/
L N
(Optional)
Timer
(Optional)
Timer
DIAGRAM C:
Use of General Live for Room Stat
Optional
Room Stat
Frost
Stat
Mains In
Frost
Room
Stat
Stat/
L N
(Optional)
Timer
DIAGRAM A:
DIAGRAM B:
Room Stat with External Timer
Programmable Room Stat or
Room Stat with Internal Timer
Optional
Room Stat or
Optional
Frost
Programmable
Frost
Stat
Room Stat
Stat
Room Stat
Timer
Frost
Room
Frost
Room
Stat
Stat/
L N
Stat
Stat/
L N
(Optional)
Timer
(Optional)
Timer
DIAGRAM C:
Use of General Live for Room Stat
Optional
Room Stat
Frost
Stat
Mains In
Frost
Room
Stat
Stat/
L N
(Optional)
Timer
DIAGRAM A:
DIAGRAM B:
Room Stat with External Timer
Programmable Room Stat or
Room Stat with Internal Timer
Optional
Room Stat or
Optional
Frost
Programmable
Frost
Stat
Room Stat
Stat
Room Stat
Timer
Frost
Room
Frost
Room
Stat
Stat/
L N
Stat
Stat/
L N
(Optional)
Timer
(Optional)
Timer
DIAGRAM C:
Use of General Live for Room Stat
Optional
Room Stat
Frost
Stat
Mains In
Frost
Room
Stat
Stat/
L N
(Optional)
Timer
DIAGRAM D:
OpenTherm Device
DO NOT CONNECT 230V TO THESE
TERMINALS OR THE BOILER ELECTRONICS
WILL BE DAMAGED
Outside
Sensor
Open
Therm
OpenTherm Device
E.G. Honeywell OT
Bridge R8810
External Controls – 230V 50Hz
Wiring a 230V 50Hz Room Thermostat,
Diagram A (with optional timer, Diagram B)
1. Remove the link wire from the room
stat/timer plug.
2. Connect the external cable from
the room stat/timer across these
two connections, if a general live
connection is used for the room stat
or timer then connect this to the fused
spur, on the load side (see Diagram
C)
3. If the room thermostat has
compensation and requires a neutral
connection, make this connection to
the fused spur, on the load side.
Optional External Controls – Extra Low
Voltage
Wiring OpenTherm Room Control or other
OpenTherm Master Device, Diagram D.
1. Remove the timer link plug inside the
timer option cover, located on the
front of the control box
2. Unclip the timer link socket from the
aperture on the rear of the control box,
locate the plug on the same harness
branch and connect these together.
3. Using the rubber bung located
adjacent to these connections, insert
it into the open aperture.
4. Install an OpenTherm connecter (supplied
with OpenTherm Harness or Weather
Compensation kit) on the RHS of the
boiler installer connections and connect
the 2 core cable from the OpenTherm
device.
Frost Protection
If parts of the pipework run outside the
house or if the boiler will be left off for more
than a day or so then a frost thermostat
should be wired into the system.
This is usually done at the programmer, in
which case the programmer selector switches
are set to OFF and all the other controls MUST
be left in the running position.
The frost thermostat should be sited in a
cold place but where it can sense heat
from the system.
Wiring a system frost thermostat, see
digarams A, B and C. Wire the frost
thermostat across the two connections as
shown.
Note
.
If the boiler is installed in a garage it
may be necessary to fit a pipe thermostat,
preferably on the return pipework.
INST
ALLA
TION
Summary of Contents for INDEPENDENT COMBI 24
Page 4: ...4 Installation and Servicing...
Page 6: ...6 Installation and Servicing...
Page 63: ...63 Installation and Servicing...
Page 64: ......
Page 70: ...70 Installation and Servicing...
Page 71: ...71 Installation and Servicing...