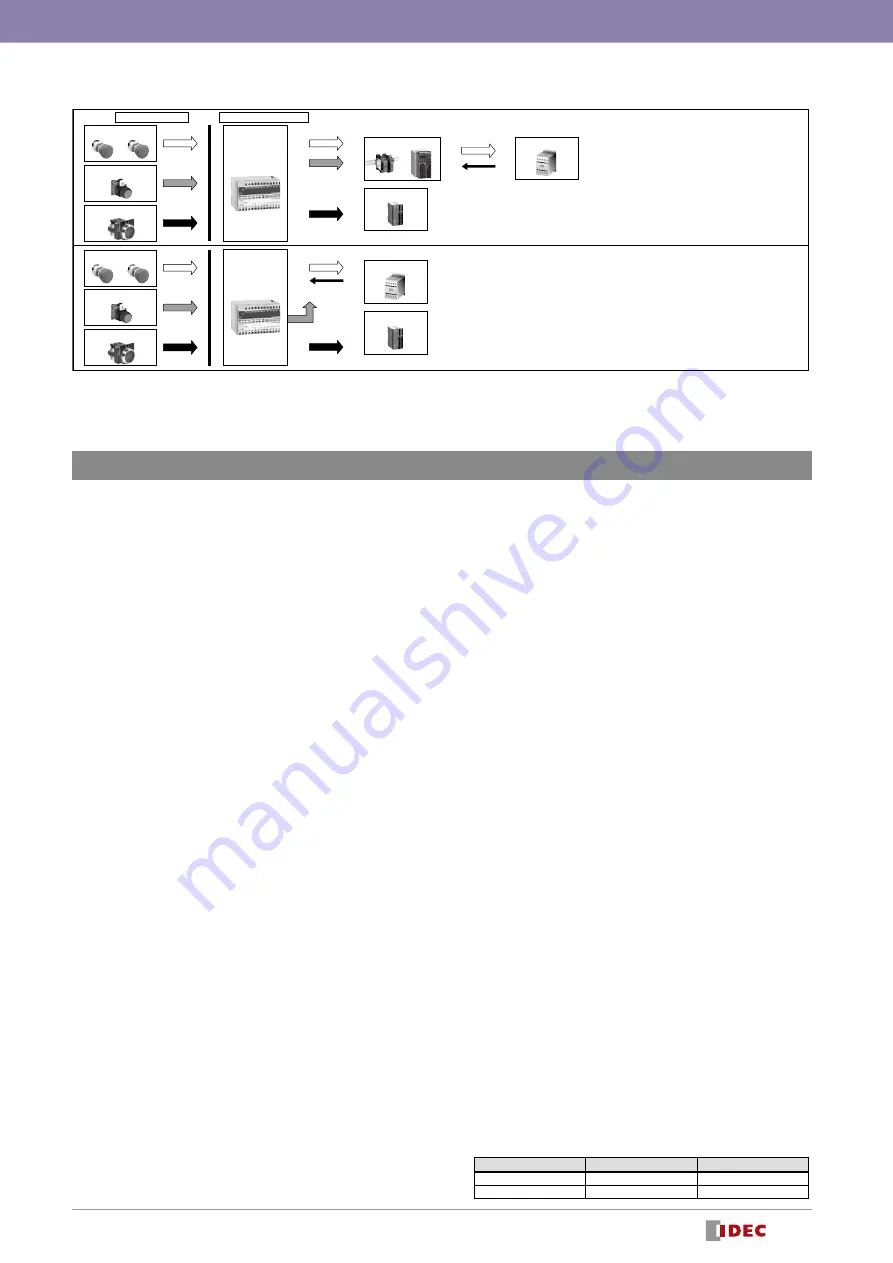
Safety Control Device
Reset (Start) Switch
Other Input Device
PLC
PLC
Safety Contactor
Safety Contactor
Safety Output
Backcheck Input
Installing a reset switch in a hazardous area, using auxiliary input and output
Barrier Safety Output
Reset (Start) Output
Other Output
EB3N-A2R5D
EB3N-M2R5D
Barrier Safety Output
Backcheck Input
Reset (Start) Input
Other Output
Hazardous Area
Non-hazardous Area
Safety Input Devices
…
Reset (Start) Switch
Other Input Device
Safety Input Devices
Safety Input Devices Connectable to Safety Input Terminals (Examples)
Emergency stop switch: (Non-illuminated) XW1E-BV402MFRH, XN4E-BL412MRH
Safety switch:
HS6B-02B05, HS1B-02R
Operating Instructions
Notes for Operation
1. Do not disassemble, repair, or modify the EB3N safety relay barrier,
otherwise the safety characteristics may be impaired.
2. Use the EB3N within its specification values.
3. The EB3N can be mounted in any direction.
4. Mount the EB3N on a 35-mm-wide DIN rail or directly on a panel surface
using screws. When mounting on a DIN rail, push in the clamp and use end
clips to secure the EB3N. When mounting on a panel surface, tighten the
screws firmly.
5. Excessive noise may cause malfunction or damage to the EB3N. When the
internal voltage limiting circuit (thyristor) has shut down the power due to
noise, remove the cause of the noise before powering up again.
6. The internal power circuit contains an electronic fuse to suppress
overcurrents. When the electronic fuse has tripped, shut down the power,
remove the cause of the overcurrent before powering up again.
7. Use crimping terminals with insulation sheath for wiring. Tighten the terminal
screws, including unused terminal screws, to a recommended tightening
torque of 0.6 to N·m using a screwdriver of ø5.5 mm in diameter.
8. Before inspecting or replacing the EB3N, turn off the power.
Notes for Machine Safety
1. Operate the safety input device to check the EB3N functionality everyday.
2. For safety input devices, such as safety switches or emergency stop
switches, connected to the EB3N, use safety standard-compliant devices
with direct opening action and 2NC contacts.
3. Do not use the auxiliary input as a safety input.
4. For safety control devices connected with the EB3N, use machine safety
standard-compliant devices with a disparity detection function.
5. Use safety inputs and safety outputs in a circuit configuration compliant
with safety requirements.
6. To calculate the safety distance, take into consideration the response time
of all devices comprising the system, such as the EB3N and safety devices
connected to the EB3N.
7. Separate the input and output wiring from power lines and motor lines.
8. When using multiple EB3N safety relay barriers, do not connect one switch
to more than one EB3N. Use separate switches for each EB3N.
9. To ensure EMC, use shielded cables for safety inputs and auxiliary inputs.
Connect the shield to the FG of the control panel on which the EB3N is
mounted.
10. For protection against overcurrents, connect an IEC60127-2-compliant 2A
fast-blow fuse (5 × 20 mm).
11. Evaluate the ISO 13849-1 category and performance level in consideration
of the entire system.
Notes for Explosion Protection Safety
1. Install the EB3N in an enclosure capable of protecting against mechanical
shocks at a hazardous location in accordance with intrinsic safety ratings
and parameters.
2. Install and wire the EB3N so that the EB3N is not subject to electromagnetic
and electrostatic induction and does not contact with other circuits.
For example, keep a minimum spacing of 50 mm between intrinsically safe
and non-intrinsically safe circuits, or provide a metallic separating board
between the intrinsically safe circuit and non-intrinsically safe circuit. When
providing a metallic separating board, make sure that the board fits closely
to the enclosure (top, bottom, and both sides). Allowable clearance between
the board and the enclosure is 1.5 mm at the maximum.
When a motor circuit or high-voltage circuit is installed nearby, keep a wider
spacing than 50 mm between intrinsically safe and non-intrinsically safe
circuits.
3. Keep a minimum spacing of 3 mm between the terminal or relay terminal
block of the intrinsically safe circuit and the grounded metal parts of the
metal enclosure.
4. Connect the terminals so that IP20 is ensured.
5. To prevent disengaged wires from contacting with other intrinsically safe
circuits, bind together the end of wires.
6. Make sure that the voltage of the power supply for the devices connected
to the non-intrinsically safe circuit or the internal voltage of such devices
does not exceed 250V AC/DC 50/60 Hz or 250V DC under any normal and
abnormal conditions.
7. Make sure that the wiring of intrinsically safe circuits does not contact
with other circuits or is not subject to electromagnetic and electrostatic
inductions, otherwise explosion protection is not ensured.
8. When identifying intrinsically safe circuits by color, use light blue terminal
blocks and cables.
9. When wiring the intrinsically safe circuit, determine the distance to satisfy
the wiring parameters shown below.
a) Wiring capacitance Cw ≤ Co – Ci
Co: Intrinsically safe circuit allowable capacitance
Ci: Internal capacitance of switches
b) Wiring inductance Lw ≤ Lo – Li
Lo: Intrinsically safe circuit allowable inductance
Li: Internal inductance of switches
c) Wiring resistance ≤ Rw
Rw: Allowable wiring resistance
Switches in the Hazardous Area
1. A switch contains the switch contact, enclosure, and internal wiring. A
switch contact refers to an ordinary switching device which consists of
contacts only.
2. When the switch has internal wiring or lead wire, make sure that the values
of internal capacitance (Ci) and inductance (Li) are within the certified
values.
3. Enclose the bare live part of the switch contact in an enclosure of IP20 or
higher protection.
4. Depending on the explosion-protection specifications of TIIS, the exposed
area of plastic switch operator, when installed in Japan, is limited as
follows:
Certification
Explosion Protection
Exposed Area
TC15758
Exia II CT6
20 cm
2
maximum
TC15961
Exia II BT6
100 cm
2
maximum
BGLEN01A-Fa-EB3N July 2021
3
EBN Safety Relay Modules